Soldadura de metais
1986/04/01 Rodriguez Ibabe, Jose Maria Iturria: Elhuyar aldizkaria
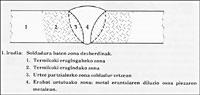
No procedemento de soldadura cambia o estado dun material (por exemplo, a temperatura), polo que normalmente tamén cambia as súas características orixinais. Por tanto, é importante saber como se solda a peza, xa que en moitos casos a posterior rotura da peza comeza no lugar onde se atopa a soldadura. Por iso, actualmente os controis de calidade das soldaduras son tan importantes como os procedementos de soldadura.
Na maioría dos procedementos de soldadura conséguese a unión das dúas pezas ao fundir parte do material mediante unha fonte de calor. En ocasións engádese outro material paira facilitar o procedemento de unión. En consecuencia, a zona de soldadura non é homoxénea e pódense distinguir distintas partes, como se observa na figura 1:
Nas zonas afectadas térmicamente poden aparecer cambios na microestructura como o aumento do tamaño do gran, a aparición da estrutura do amorne (por arrefriado rápido), etc. En consecuencia, nestas zonas as pezas serán máis fráxiles comparándoas con calquera outra parte da peza. Por iso, desde o punto de vista da rotura da peza, as zonas 2 e 3 son as máis perigosas.
Os sistemas de soldadura difusos pódense agrupar en dous grupos principais: a soldadura por fundición e a soldadura a presión. No primeiro grupo, a soldadura entre os dous compoñentes require a fusión e solidificación posterior do material, a aplicación de calquera forza externa ten una gran importancia, desexando e nalgúns casos quentando as pezas. 1. Na táboa preséntanse algúns exemplos de cada tipo de soldadura.
Soldadura por fundición
1. Soldadura a gas
Dentro deste grupo, a soldadura oxiacetilénica é a máis importante e coñecida. Neste sistema obtense facilmente a fonte de calor, acetileno e osíxeno:
C 2 H 2 +Ou 2 2CO+H 2 +106'5 Kcal
e reaccións ao aire:
CO+1/2Ou 2+2N 2 CO 2 +2N 2 +68 Kcal H 2 +1/2Ou 2+2N 2 H 2 Ou+2N 2 +56 Kcal
A temperatura do punto de inflamación é de 3100°C.
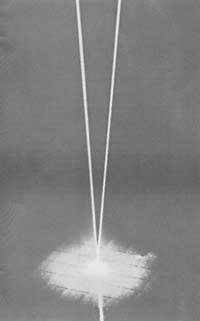
Comparado cos sistemas de soldadura Bique, por exemplo, coas soldaduras de arco, é máis lento e difícil de controlar, polo que neste momento é pouco utilizado na industria.
2. Soldadura por arco
Existen distintos sistemas de soldadura en arco, pero todos eles baséanse no principio de que entre a peza de soldadura e un electrodo créase un arco eléctrico. O electrodo é un metal con revestimento non metálico. O arco funde o ferro ou metal de soldar e indúceo. O metal fundido, ao parecerse ao lago, afástase do arco. Doutra banda, o electrodo fúndese formando pingas que, por acción do arco, son arroxadas ao lugar onde deixan os metais fundidos.
Una parte do recubrimiento produce una cortiza de gas ao evaporarse para que a soldadura non toque o aire; o resto do recubrimiento fúndese mesturándoo co metal e ao recoller a sucidade xera escoria
Dentro deste grupo atópase tamén a soldadura por arco mergullado. Neste caso, o electrodo está composto exclusivamente por metais. Nos bordos da peza e no punto dos electrodos prodúcese a fusión simultaneamente. Esta última, cun movemento de avance constante, fornece metais adicionais, mentres que coa aplicación dun po especial escápase o procedemento de oxidación durante a soldadura. Na figura 3 preséntase o esquema deste sistema de soldadura.
Entre os sistemas de soldadura que se realizan de forma automática, é dicir, o máis utilizado, especialmente en embarcacións, cubetos paira ponte, etc.
3. Soldadura por bombardeo de electróns
As pezas de soldeo introdúcense nunha cámara sen carga e mediante o feixe de electróns fúndese a zona que rodea a xunta. Este tipo de sistemas presenta algunhas vantaxes como a limpeza e a falta de procedementos de oxidación. Ademais, a zona de soldadura localízase con precisión, polo que é útil en soldaduras difíciles e imperceptibles. Con todo, a soldadura por bombardeo de electróns é moi custosa e limita considerablemente as necesidades da cámara sen carga.
4º Soldadura láser
Utilízase en substitución da soldadura por bombardeo de electróns. A súa principal vantaxe é a concentración de grandes densidades enerxéticas en zonas moi pequenas, polo que é moi apropiado paira este tipo de soldadura en electrónica. Por exemplo, por medio do láser pódense soldar fíos de 0'01 mm.
Este sistema permitiu aumentar notablemente a cantidade de automatización e produción da soldadura. Así mesmo, a calidade da forma da soldadura é tan boa que se reduciron os controis finais. Con todo, a súa maior limitación radica na profundidade de soldadura. Actualmente é bastante difícil superar os 5 mm e normalmente non se utiliza naqueles casos nos que se require una profundidade superior a un milímetro.
Soldadura a presión
1. Soldadura por explosión
Este tipo de soldadura baséase no principio de que entre as pezas de soldadura por medio dunha bomba obtense una explosión de alta velocidade. Durante a explosión aparece un fenómeno similar ao da txirimola, eliminando as partículas de óxido de superficie e provocando una gran deformación plástica, obtendo una unión total entre as dúas pezas (ver figura 4). Utilízase principalmente en xuntas de cambio de recipientes a presión e aliaxes aluminio/aluminio/aceiro.
2. Soldadura de forxa
Neste caso, mediante a difusión e a recristalización das grumas a través da superficie de contacto, baixo a combinación dunha calefacción limitada sen chegar á presión nin ao desxeo, as pezas se soldan.
Normalmente utilízase en aceiros inoxidables, sobre todo en casos nos que a soldadura por fundición é inadecuada.
3. Soldadura de resistencia
Aínda que entra na zona de soldadura a presión, a soldadura de resistencia é un sistema mixto de fusión e presión. Entre os diferentes tipos, a soldadura por puntos é a máis coñecida.
O electrodo máis utilizado é de aliaxe Cu-Co-Be. As súas formas son moi diferentes paira cubrir as necesidades de cada caso
Paira soldar calquera aceiro inoxidable, a soldadura por puntos é moi adecuada, xa que por medio deste sistema a emisión de calor é baixa, xa que as propiedades inoxidables e as características mecánicas da microestructura non se modifican. A modo de exemplo, na figura 6 móstrase a distribución en ferros de aceiro doce en soldadura por puntos.
Mediante este procedemento, os ferros finos e medios (de 0'10 a 5 mm) se sueldan entre dous e tres á vez. Se o espesor dos ferros é maior, utilizarase a soldadura por arco.
4º Soldadura por ultrasonidos
Paira satisfacer as necesidades da microelectrónica, isto é, pola limitación e pequeñez dos elementos a soldar, nos últimos anos apareceron novos tipos de soldadura. Uno deles é de ultrasonidos.
Paira soldar fíos de ouro e aluminio moi pequenos ( 25 m) no circuíto electrónico sen case quentarse, utilízase o seguinte sistema: mediante a chama de hidróxeno quéntanse os fíos até dar forma de bóla aos seus puntos. A continuación aplícanse vibracións ultrasónicas presionando a bóla contra a superficie do circuíto. Desta maneira, a temperatura aumenta ata que se solda a peza.
Este tipo de soldadura atópase automatizada e ademais hai que dicir que é moi rápida. Por exemplo, paira soldar unha rosca delgada, necesítanse só 0'005 segundos.
Finalizamos así esta pequena presentación dos sistemas de soldadura. Como xa se mencionou ao comezo do artigo, non debemos esquecer o outro problema relacionado coa soldadura, é dicir, o control de calidade. Aínda que aquí non se especifique, en case todos os casos (sobre todo no ámbito do transporte e a enerxía nuclear), tras a soldadura é necesario coñecer a calidade da soldadura. En consecuencia, os sistemas ou técnicas existentes paira o control da calidade teñen una gran importancia.
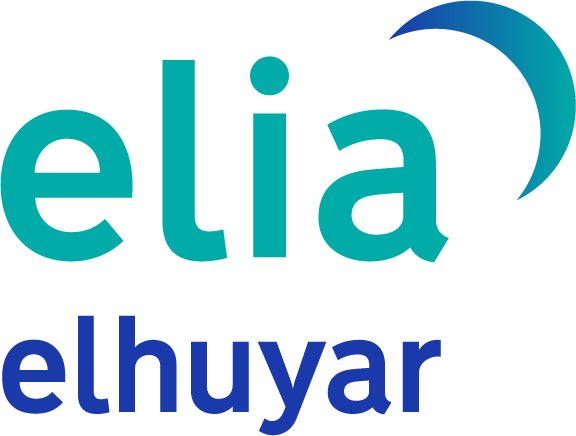
Gai honi buruzko eduki gehiago
Elhuyarrek garatutako teknologia