Soldadura de metales
1986/04/01 Rodriguez Ibabe, Jose Maria Iturria: Elhuyar aldizkaria
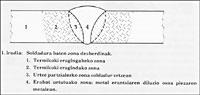
En el procedimiento de soldadura cambia el estado de un material (por ejemplo, la temperatura), por lo que normalmente también cambia sus características originales. Por lo tanto, es importante saber cómo se solda la pieza, ya que en muchos casos la posterior rotura de la pieza comienza en el lugar donde se encuentra la soldadura. Por ello, actualmente los controles de calidad de las soldaduras son tan importantes como los procedimientos de soldadura.
En la mayoría de los procedimientos de soldadura se consigue la unión de las dos piezas al fundir parte del material mediante una fuente de calor. En ocasiones se añade otro material para facilitar el procedimiento de unión. En consecuencia, la zona de soldadura no es homogénea y se pueden distinguir distintas partes, como se observa en la figura 1:
En las zonas afectadas térmicamente pueden aparecer cambios en la microestructura como el aumento del tamaño del grano, la aparición de la estructura del temple (por enfriamiento rápido), etc. En consecuencia, en estas zonas las piezas serán más frágiles comparándolas con cualquier otra parte de la pieza. Por ello, desde el punto de vista de la rotura de la pieza, las zonas 2 y 3 son las más peligrosas.
Los sistemas de soldadura difusos se pueden agrupar en dos grupos principales: la soldadura por fundición y la soldadura a presión. En el primer grupo, la soldadura entre los dos componentes requiere la fusión y solidificación posterior del material, la aplicación de cualquier fuerza externa tiene una gran importancia, deseando y en algunos casos calentando las piezas. 1. En la tabla se presentan algunos ejemplos de cada tipo de soldadura.
Soldadura por fundición
1. Soldadura a gas
Dentro de este grupo, la soldadura oxiacetilénica es la más importante y conocida. En este sistema se obtiene fácilmente la fuente de calor, acetileno y oxígeno:
C 2 H 2 +O 2 2CO+H 2 +106'5 Kcal
y reacciones al aire:
CO+1/2O 2+2N 2 CO 2 +2N 2 +68 Kcal H 2 +1/2O 2+2N 2 H 2 O+2N 2 +56 Kcal
La temperatura del punto de inflamación es de 3100°C.
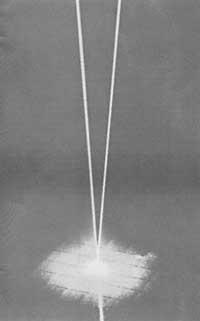
Comparado con los sistemas de soldadura Bese, por ejemplo, con las soldaduras de arco, es más lento y difícil de controlar, por lo que en este momento es poco utilizado en la industria.
2. Soldadura por arco
Existen distintos sistemas de soldadura en arco, pero todos ellos se basan en el principio de que entre la pieza de soldadura y un electrodo se crea un arco eléctrico. El electrodo es un metal con revestimiento no metálico. El arco funde la plancha o metal de soldar y lo induce. El metal fundido, al parecerse al lago, se aleja del arco. Por otro lado, el electrodo se funde formando gotas que, por acción del arco, son arrojadas al lugar donde dejan los metales fundidos.
Una parte del recubrimiento produce una corteza de gas al evaporarse para que la soldadura no toque el aire; el resto del recubrimiento se funde mezclándolo con el metal y al recoger la suciedad genera escoria
Dentro de este grupo se encuentra también la soldadura por arco sumergido. En este caso, el electrodo está compuesto exclusivamente por metales. En los bordes de la pieza y en el punto de los electrodos se produce la fusión simultáneamente. Esta última, con un movimiento de avance constante, suministra metales adicionales, mientras que con la aplicación de un polvo especial se escapa el procedimiento de oxidación durante la soldadura. En la figura 3 se presenta el esquema de este sistema de soldadura.
Entre los sistemas de soldadura que se realizan de forma automática, es decir, el más utilizado, especialmente en embarcaciones, cubetos para puente, etc.
3. Soldadura por bombardeo de electrones
Las piezas de soldeo se introducen en una cámara de vacío y mediante el haz de electrones se funde la zona que rodea la junta. Este tipo de sistemas presenta algunas ventajas como la limpieza y la falta de procedimientos de oxidación. Además, la zona de soldadura se localiza con precisión, por lo que es útil en soldaduras difíciles e imperceptibles. Sin embargo, la soldadura por bombardeo de electrones es muy costosa y limita considerablemente las necesidades de la cámara de vacío.
4º Soldadura láser
Se utiliza en sustitución de la soldadura por bombardeo de electrones. Su principal ventaja es la concentración de grandes densidades energéticas en zonas muy pequeñas, por lo que es muy apropiado para este tipo de soldadura en electrónica. Por ejemplo, por medio del láser se pueden soldar hilos de 0'01 mm.
Este sistema ha permitido aumentar notablemente la cantidad de automatización y producción de la soldadura. Asimismo, la calidad de la forma de la soldadura es tan buena que se han reducido los controles finales. Sin embargo, su mayor limitación radica en la profundidad de soldadura. Actualmente es bastante difícil superar los 5 mm y normalmente no se utiliza en aquellos casos en los que se requiere una profundidad superior a un milímetro.
Soldadura a presión
1. Soldadura por explosión
Este tipo de soldadura se basa en el principio de que entre las piezas de soldadura por medio de una bomba se obtiene una explosión de alta velocidad. Durante la explosión aparece un fenómeno similar al de la txirimola, eliminando las partículas de óxido de superficie y provocando una gran deformación plástica, obteniendo una unión total entre las dos piezas (ver figura 4). Se utiliza principalmente en juntas de cambio de recipientes a presión y aleaciones aluminio/aluminio/acero.
2. Soldadura de forja
En este caso, mediante la difusión y la recristalización de las grumas a través de la superficie de contacto, bajo la combinación de una calefacción limitada sin llegar a la presión ni al deshielo, las piezas se soldan.
Normalmente se utiliza en aceros inoxidables, sobre todo en casos en los que la soldadura por fundición es inadecuada.
3. Soldadura de resistencia
Aunque entra en la zona de soldadura a presión, la soldadura de resistencia es un sistema mixto de fusión y presión. Entre los diferentes tipos, la soldadura por puntos es la más conocida.
El electrodo más utilizado es de aleación Cu-Co-Be. Sus formas son muy diferentes para cubrir las necesidades de cada caso
Para soldar cualquier acero inoxidable, la soldadura por puntos es muy adecuada, ya que por medio de este sistema la emisión de calor es baja, ya que las propiedades inoxidables y las características mecánicas de la microestructura no se modifican. A modo de ejemplo, en la figura 6 se muestra la distribución en planchas de acero dulce en soldadura por puntos.
Mediante este procedimiento, las planchas finas y medias (de 0'10 a 5 mm) se sueldan entre dos y tres a la vez. Si el espesor de las planchas es mayor, se utilizará la soldadura por arco.
4º Soldadura por ultrasonidos
Para satisfacer las necesidades de la microelectrónica, esto es, por la limitación y pequeñez de los elementos a soldar, en los últimos años han aparecido nuevos tipos de soldadura. Uno de ellos es de ultrasonidos.
Para soldar hilos de oro y aluminio muy pequeños ( 25 m) en el circuito electrónico sin casi calentarse, se utiliza el siguiente sistema: mediante la llama de hidrógeno se calientan los hilos hasta dar forma de bola a sus puntos. A continuación se aplican vibraciones ultrasónicas presionando la bola contra la superficie del circuito. De esta manera, la temperatura aumenta hasta que se solda la pieza.
Este tipo de soldadura se encuentra automatizada y además hay que decir que es muy rápida. Por ejemplo, para soldar una rosca delgada, se necesitan sólo 0'005 segundos.
Finalizamos así esta pequeña presentación de los sistemas de soldadura. Como ya se ha mencionado al inicio del artículo, no debemos olvidar el otro problema relacionado con la soldadura, es decir, el control de calidad. Aunque aquí no se especifique, en casi todos los casos (sobre todo en el ámbito del transporte y la energía nuclear), tras la soldadura es necesario conocer la calidad de la soldadura. En consecuencia, los sistemas o técnicas existentes para el control de la calidad tienen una gran importancia.
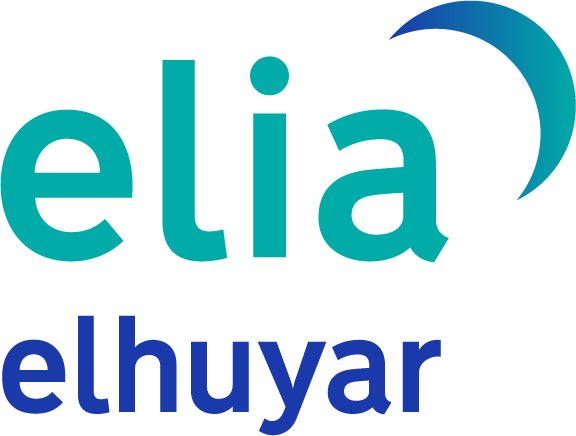
Gai honi buruzko eduki gehiago
Elhuyarrek garatutako teknologia