Welding of metals
1986/04/01 Rodriguez Ibabe, Jose Maria Iturria: Elhuyar aldizkaria
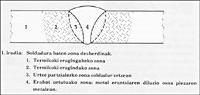
In the welding procedure changes the state of a material (for example, temperature), so it normally also changes its original characteristics. Therefore, it is important to know how the piece is welded, since in many cases the subsequent break of the piece begins at the place where the welding is located. For this reason, currently the quality controls of the welds are as important as the welding procedures.
In most welding procedures, the union of the two parts is achieved by melting part of the material through a heat source. Sometimes another material is added to facilitate the binding procedure. Consequently, the welding zone is not homogeneous and different parts can be distinguished, as shown in figure 1:
In thermally affected areas, changes in the microstructure can appear, such as the increase in grain size, the appearance of the structure of the temple (by rapid cooling), etc. Consequently, in these areas the pieces will be more fragile compared to any other part of the piece. Therefore, from the point of view of the breaking of the piece, zones 2 and 3 are the most dangerous.
Diffuse welding systems can be grouped into two main groups: cast welding and pressure welding. In the first group, the welding between the two components requires the subsequent fusion and solidification of the material, the application of any external force has great importance, wishing and in some cases heating the parts. 1. Some examples of each type of welding are presented in the table.
Welding by casting
1. Welding to gas
Within this group, oxyacetylenic welding is the most important and known. In this system the source of heat, acetylene and oxygen is easily obtained:
C 2 H 2 +O 2 2CO+H 2 +106'5 Kcal
and reactions to the air:
CO+1/2O 2+2N 2 CO 2 +2N 2 +68 Kcal H 2 +1/2O 2+2N 2 H 2 O+2N 2 +56 Kcal
The temperature of the inflammation point is 3100°C.
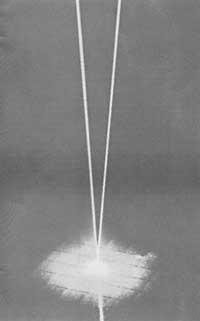
Compared to Bese welding systems, for example, with arc welds, it is slower and difficult to control, so at this time it is little used in the industry.
2. Welding by arc
There are different arc welding systems, but all of them are based on the principle that between the soldering piece and an electrode an electric arc is created. The electrode is a metal with non-metallic coating. The bow melts the plate or soldering metal and induces it. The molten metal, when resembling the lake, is removed from the arch. On the other hand, the electrode is melted forming drops that, by action of the arc, are thrown to the place where the molten metals leave.
A part of the coating produces a gas crust when evaporating so that the solder does not touch the air; the rest of the coating melts mixing it with the metal and when collecting the dirt generates slag
Within this group is also the submerged arc welding. In this case, the electrode is composed exclusively of metals. At the edges of the piece and at the point of the electrodes, fusion occurs simultaneously. The latter, with a constant advancement movement, supplies additional metals, while with the application of a special powder the oxidation procedure is escaped during welding. Figure 3 presents the outline of this welding system.
Among the welding systems that are made automatically, that is, the most used, especially in boats, buckets for bridge, etc.
3. Welding by electron bombardment
The welding pieces are introduced into a vacuum chamber and through the electron beam the area surrounding the joint is melted. This type of systems presents some advantages such as cleaning and the lack of oxidation procedures. In addition, the welding area is precisely located, making it useful in difficult and imperceptible welds. However, electron bombardment soldering is very costly and considerably limits the needs of the vacuum chamber.
4º Laser welding
It is used in substitution of welding by bombardment of electrons. Its main advantage is the concentration of large energy densities in very small areas, so it is very appropriate for this type of welding in electronics. For example, by means of the laser, threads of 0'01 mm can be welded.
This system has significantly increased the amount of automation and welding production. Likewise, the quality of the welding form is so good that the final controls have been reduced. However, its greatest limitation lies in the depth of welding. It is currently quite difficult to exceed 5 mm and is usually not used in those cases where a depth of more than one millimeter is required.
Pressure Welding Pressure Welding
1. Soldering by explosion
This type of welding is based on the principle that among the soldering parts by means of a pump is obtained a high speed explosion. During the explosion there appears a phenomenon similar to that of the txirimola, eliminating the particles of surface oxide and causing a great plastic deformation, obtaining a total union between the two pieces (see figure 4). It is mainly used in pressure vessel exchange joints and aluminium/aluminium/steel alloys.
2. Forging soldering iron
In this case, by means of the diffusion and recristalization of the coarse through the contact surface, under the combination of a limited heating without reaching the pressure or the thaw, the pieces are welded.
It is usually used in stainless steels, especially in cases in which cast welding is inadequate.
3. Welding of resistance
Although it enters the area of pressure welding, the resistance welding is a mixed fusion and pressure system. Among the different types, spot welding is the most well-known.
The most commonly used electrode is Cu-Co-Be alloy. Their forms are very different to cover the needs of each case
To weld any stainless steel, welding by points is very adequate, since by means of this system the heat emission is low, since the stainless properties and the mechanical characteristics of the microstructure are not modified. As an example, Figure 6 shows the distribution of sweet steel plates in soldering by points.
Through this procedure, thin and medium plates (from 0'10 to 5 mm) are welded between two and three at a time. If the thickness of the plates is greater, the arc welding will be used.
4º Ultrasonic welding
To meet the needs of microelectronics, that is, by the limitation and smallness of the elements to weld, in recent years new types of welding have appeared. One of them is ultrasound.
To weld very small gold and aluminium threads (25 m) in the electronic circuit without almost heating, the following system is used: by means of the hydrogen flame the threads are heated up to give shape of ball to its points. Ultrasonic vibrations are then applied by pressing the ball against the surface of the circuit. In this way, the temperature increases until the piece is welded.
This type of welding is automated and it must also be said that it is very fast. For example, to weld a thin thread, you need only 0'005 seconds.
We finish this way this small presentation of the welding systems. As already mentioned at the beginning of the article, we should not forget the other problem related to welding, that is, quality control. Although it is not specified here, in almost all cases (especially in the field of transport and nuclear energy), after the welding it is necessary to know the quality of the welding. Consequently, the existing systems or techniques for quality control are of great importance.
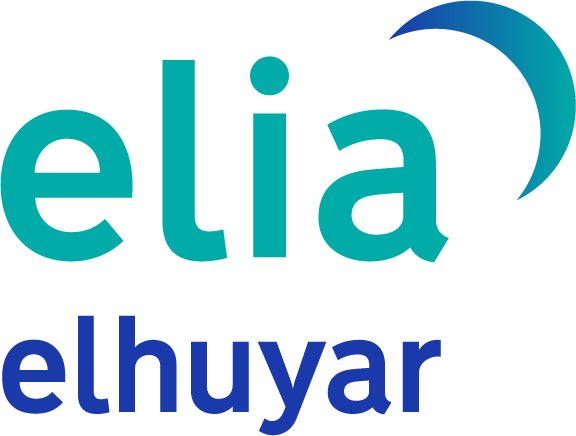
Gai honi buruzko eduki gehiago
Elhuyarrek garatutako teknologia