Lindane in Barakaldo: the end of the nightmare closer
1999/08/01 Mujika, Alfontso - Elhuyar Fundazioa Iturria: Elhuyar aldizkaria
A little history
XX. At the beginning of the second half of the 20th century the chemical industry grew rapidly in Bizkaia, but this growth occurred behind the backs of environmental problems and left an unfortunate legacy: pollution and,
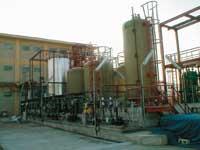
In particular, waste and contaminated land. Lindane is an organochlorinated pesticide, one of the isomers of hexachlorocyclohexane, known as HCH, to summarize. HGH contains 5 isomers, but only one of them, the gamma isomer, serves to kill insects, which is lindane.
The raw materials for lindane production are benzene and chlorine. The reaction is obtained by mixing the five isomers, then separating the lindane from the rest. The rest of isomers are useless, that is, they are waste. To produce one kilogram of lindane 9 kilograms of HGH waste are generated. HGH is very toxic and dangerous to human health and the environment. In fact, the World Health Organization recommends the management of HGH as a carcinogen. Two companies located in Bizkaia manufactured lindane for decades and most of the HGH waste was uncontrollably deposited in the area's landfills. In addition, the company Bilbao Chemicals de Barakaldo closed its factory in 1987 leaving accumulated in its pavilions four thousand five hundred tons of pure HGH. This unfortunate "legacy" has been and is a nightmare of vizcaínos and above all of Barakaldo.
Looking for solutions
The Department of Environment of the Basque Government addressed the problem and, through the Public Environmental Management Company IHOBE, after analyzing all possible solutions or solutions, proposed two solutions, one for contaminated land and one for pure HGH.
Safety cell for contaminated soils
Because there is currently no technically and simultaneously economically viable process of eliminating HGH mixed with soil and other industrial wastes, it has been chosen to store these contaminated soils temporarily, that is, until finding the necessary technological solution to definitively solve the problem, in security deposits (More information on this can be found in the February 1996 issue of Elhuyar Zientzia eta Teknika).
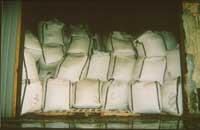
Safety Cells are structures for the storage of hazardous substances that isolate and prevent access to the environment. This solution has already been used in other countries, such as France or the Netherlands, and is internationally recognized. The problem of lindane waste is not only ours, but also international.
A security cell has been built in Loiu for the deposition of contaminated land in the right valley of the Nervión. It ended a year ago. Contaminated soils in the left meadow will also be stored in a safety cell like Loiu. The cell will be located on the slopes of Mount Argalario in Barakaldo and construction works will begin shortly.
What to do with pure HGH?
IHOBE technicians have sought technological solutions for the definitive destruction of pure HGH. To do this, in 1991 the Environmental Agency, EPA, traveled to the United States to learn about a new process of decomposition (decloration) of the organochlorine compounds that was being developed in the Cincincinnati laboratory at a temperature below 200 °C and without producing dioxins or other toxic by-products. This process is patented and known as Based Catalyzed Decomposition (BCD). There are other alternatives to the treatment of HGH, such as incineration, cracking or inertization, but they are very expensive or cause serious environmental problems.
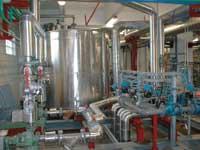
BCD technology has been used in the United States to remove other organochlorine compounds, but to date it has not been used to remove HGH. Therefore, in order to ensure the actual feasibility of the process, IHOBE, after the acquisition of the patent, carried out numerous trials in 1992 and 1993, first in the laboratory and later in a pilot plant built in Zamudio, whose results demonstrated the suitability of the process for the treatment of pure HGH. Once this has been verified, the construction phase of the industrial plant has begun. It has been built in Barakaldo, specifically on the site where the company Bilbao Chemicals was located, since this site is contaminated by HCH. The first of them was the conditioning of the old pavilion (roofs, accesses, etc. ), so the remains of pure HCH were introduced in large sacks and moved to that pavilion in 1993. There it has been stored until it has begun to treat in a closed enclosure. The plant began its activity last month and it is estimated that the treatment of the four thousand five hundred tons of pure HGH will take place for two years.
How is HGH removed?
The goal is to eliminate chlorine from HGH, mixing caustic soda in liquid medium and accompanied by a catalyst. In this way a commercial product is obtained, trichlorobenzene, also known as TCB, which is used as raw material in the industry. In turn you get a by-product, brine, salt and water. Let's look at the process in parts:
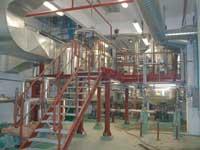
The first step is the discharge of the waste. The HCH is stored in large sacks: it is removed, the hips are broken and crushed in a mill to be pulverised again and the HCH powder is sent by an elevator to the feeder. These works are carried out in a closed enclosure, equipped with a system of suction and filtering of dust and air. Subsequently, the HCH is mixed with the TCB (since the liquid medium necessary for the reaction to occur is the TCB itself) in a tank and the dispersion is carried to one of the two reactors. Reactors are the heart of the facility, where the chemical reaction occurs. Once the HCH and TCB are inserted into the reactor, soda and catalyst are added.
The chemical reaction is exothermic, that is, it expels the heat. This heat comes out of the reactor in different ways and a thermal control system is used to ensure that the temperature inside the reactor does not exceed 150ºC. The reaction lasts 30 minutes and the whole process lasts about an hour. During this period a ton of HCH provides 600 liters of TCB, in addition to generating salt and water, ie brine.
Once the chemical reaction is finished, the reactor is emptied and a filter is driven. There the salt –solid– and the TCB –liquid– that are the result of the reaction are separated. From there everyone needs their own debugging process.
The TCB generated in the reaction is taken to the tanks (a part is redirected to the reactor) and then passed to the distillation process. In the distillation column isomers are separated to obtain the commercial TCB (1,2,4 TCB) which is stored in an external tank for sale. This will obtain 3,000 tons of commercial TCB.
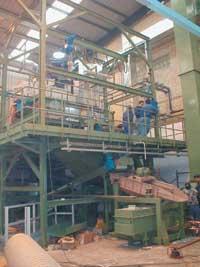
Moreover, the saline solution accumulates at the bottom of the reactor, but this brine contains an excess of caustic soda that must be neutralized with hydrochloric acid to obtain a neutral pH. When the brine is soaked by TCB it is centrifuged, separating two liquid phases depending on the density. The clean phase passes through an active carbon filter where the organic matter and the final remnants of TCB and HCH are absorbed, and the brine is stored in an external tank. Then it is poured into the estuary, as it is only water and salt. The dirty phase, with TCB, is passed through a filter press to remove moisture. After drying there is a solid residue.
The Barakaldo plant is the first to be built in the world to eliminate HGH. Safety measures include flameproof materials, dust, air and gas suction systems, automatic safety stop and automatic operating control systems. In addition, all existing pumps in the plant are duplicated. The controls are carried out continuously to ensure that the emissions from the installation do not exceed the maximum allowed limit. In these controls the concentration of pollutants is measured in air, soil and water. They were carried out before the construction of the installation, have been carried out during the construction and the controls will be carried out once the facilities have been completed.
Two years after the commissioning, after the total elimination of pure HGH, the disassembly of the plant, the demolition of the building and the excavation of the soil will proceed. The waste, debris and land of the site will be transferred to the security
cell of Argalario.This facility will allow to completely close the cycle of pure HGH. Therefore, it can be said that the end of the lindane nightmare is now closer.
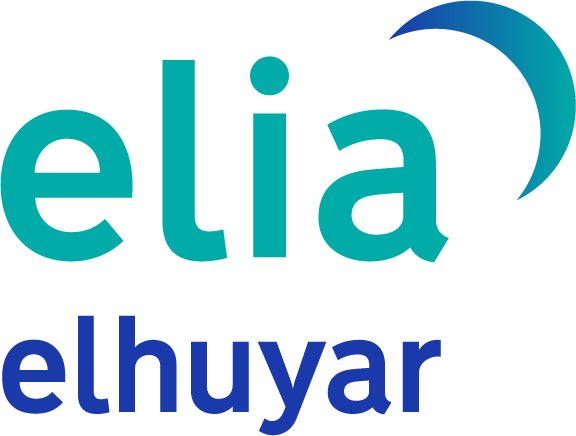
Gai honi buruzko eduki gehiago
Elhuyarrek garatutako teknologia