Aceiro: nin líquido, nin sólido
2014/01/01 Kortabarria Olabarria, Beñardo - Elhuyar Zientzia Iturria: Elhuyar aldizkaria
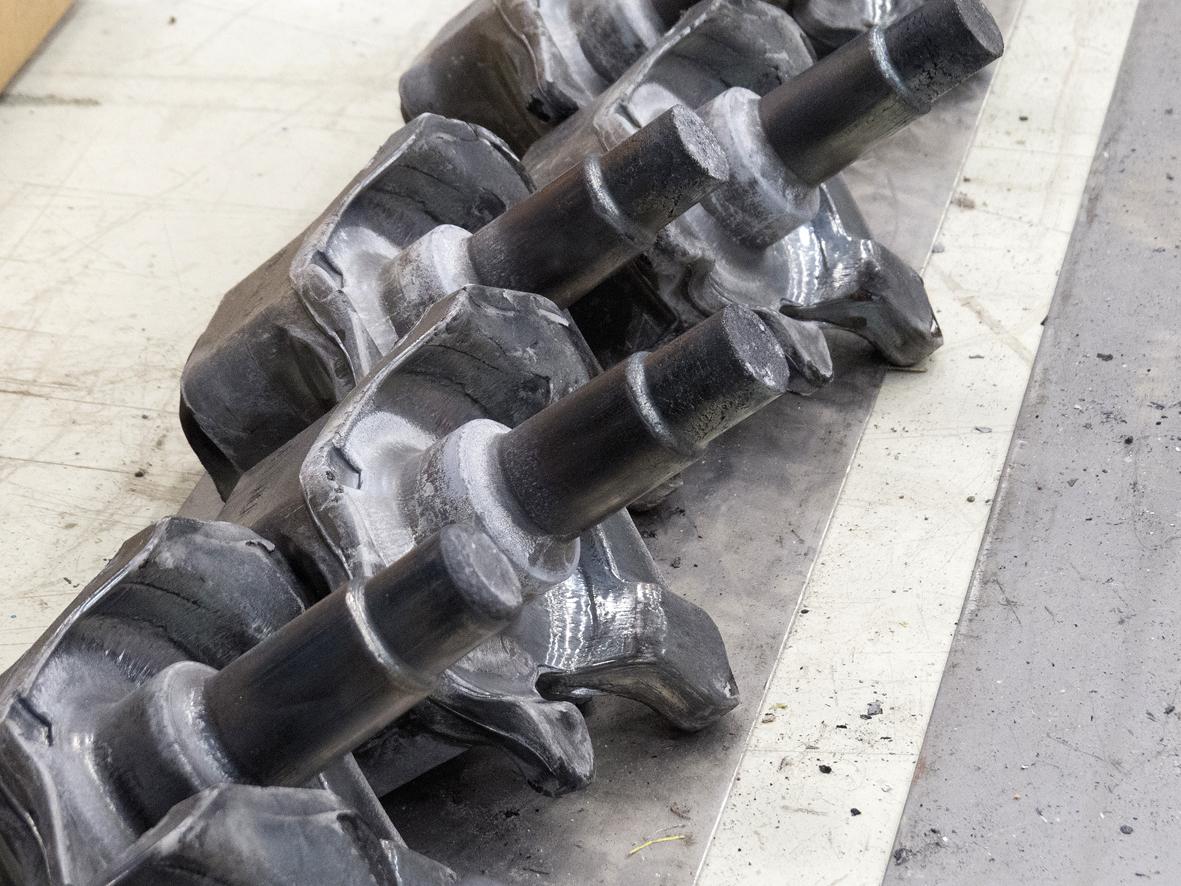
Mondragon Unibertsitatea, CIE Automotive e CIC Margune colaboran paira trasladar a tecnoloxía do tixoconformado á industria do aceiro. De feito, as sesións de laboratorio realizadas até a data demostraron que a tixoconformación pode ser una oportunidade real paira traballar o aceiro. "A nivel industrial aínda non se utiliza --as palabras son de Jokin Lozares, investigadores que traballan en Mondragon Unibertsitatea sobre a tixoconformación. No caso do aluminio houbo algo, pero hoxe en día non se fai demasiado. O magnesio, pola súa banda, é un proceso industrial denominado tixomolding. No mundo do aceiro non hai ninguén que fabrique pezas por tixoconformación, polo que é un proceso innovador".
--> Ver “Traballando con aceiro brando”, reportaxe de Teknopolis
Do aluminio ao ferro
Jokin mencionou o aluminio. Hai uns anos, en Mondragon Unibertsitatea, levou a cabo un proxecto paira traballar o aluminio mediante a tixoconformación. Isto débese a que a posta en estado semi-líquido semi-sólido facilita o corte e moldeo. Este estado semisólido fai especial o material, do mesmo xeito que a pasta de dentes, que se atopa en forma sólida dentro do bote, pero que debe "licuarse" paira a súa extracción e volver compactarse ou aumentar a viscosidad cando está fóra paira manter a súa forma, é dicir, os esforzos de corte diminúen a viscosidad aumentando a fluidez e, ao desaparecer estes esforzos, a viscosidad volve a valores anteriores. Trátase dun comportamento tixotrópico que se obtén a unha temperatura determinada.
O aluminio é un dos metais máis utilizados na industria --por detrás do ferro- pola súa lixeireza e pola súa resistencia a pesar do seu peso. Con todo, fórxaa tradicional e a inxección son as formas máis comúns de fabricar pezas de aluminio, una en sólido e outra en líquido. En cambio, o seu estado semi-sólido permite obter pezas moito máis complexas que a forxa, obtendo á súa vez una porosidad moito menor e mellores propiedades mecánicas que cando é totalmente líquido.
Primeiro hai que quentar o aluminio. Quentar até 700ºC e deixar arrefriar. O segredo está en bater o aluminio a 620ºC cando empeza a solidificarse. Colócase nun campo magnético e a medida que se axita, o aluminio vai adquirindo una estrutura especial, cambiando o tamaño e forma do gran ou gran. En lugar da estrutura dendrítica ramificada e alargada que caracteriza ao aluminio, obtense una estrutura granular máis redondeada.
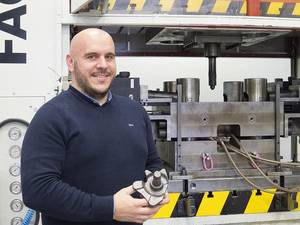
En Mondragon Unibertsitatea están convencidos de que este método permite obter formas máis complexas e de maior calidade que a forxa tradicional, apostando por iso. O reto agora é o aceiro, segundo Jokin Lozares, e estanse ensaiando cunha peza real que levan os coches: "É una peza que se coloca nun determinado modelo de coche, un pivote situado na roda sobre o que vai, entre outras cousas, o freo de disco. É una peza crítica de xeometría complexa".
Actualmente fabrica esta peza en CIE Legazpia. Mikel Intxausti é o responsable de produción da planta de Legazpi. "O proceso comeza por unha barra laminada. Cortándoo conseguimos un taco ou taco de aceiro. Estes tacos cárganse na instalación e quéntanse a 1.250 graos nun forno de indución. Despois, nunha prensa mecánica dunhas 2.500 toneladas, dáse o primeiro golpe e sácase o tallo. Damos un segundo golpe á atalaia, de onde salgue una forma similar á do final. Cun terceiro golpe salgue a peza terminada e á beira quítanselle as rebabas noutra prensa mecánica até conseguir a peza final".
De 3 a 1 golpe
A técnica que se está traballando en Mondragon Unibertsitatea é máis curta que a de Lantegi. "Facémolo nun só golpe -di Jokin Lozares-, é dicir, o proceso que hoxe necesita tres pasos facémolo nun só. Quentamos o palanquilla de case tres quilos ao forno. Una vez quentado, colócase o palanquilla no molde e dáse forma cunha prensa nun só golpe".
Segundo a investigadora de Mondragon Unibertsitatea, ademais de facilitar o proceso, esta técnica permitiu aforrar material. Se se compara coa peza realizada en Forxa, no proceso de tixoconformación prodúcese un aforro do 20-25% no peso da peza, entre outras razóns pola ausencia de rebaba.
Segundo Jokin Lozares, a temperatura é a clave paira conformar ben o aceiro: "No noso caso pomos líquido entre o 15 e o 20% do palanquilla, quedando o resto en estado sólido. Cando se aplica a forza, a viscosidad do material diminúe, faise máis branda. E iso é o que permite facer a peza nun só paso".
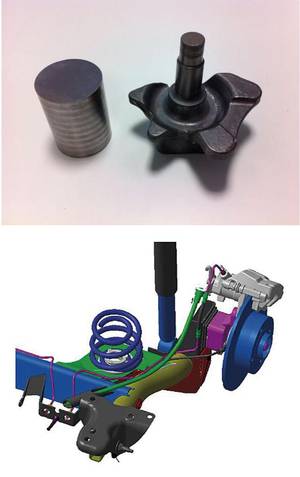
Colocan o aceiro a uns 1.400 ºC, 200 ºC máis que en fórxaa convencional. En fórxaa quente todo está sólido, nunca pasa a estado líquido. Debido á necesidade dun quecemento homoxéneo na tixoconformación, tiveron problemas de manter o aceiro a unha temperatura homoxénea, sen fundilo, xa que foi difícil paira eles. "Pero o superamos -comenta Lozares-. A temperatura é o factor crítico".
A pesar de que xa superaron as fluctuaciones da temperatura, ao longo do proceso tiveron outras dificultades. Segundo Lozares, a duración dos troqueles foi una delas. "De feito, na tixoconformación hai una gran diferenza de temperatura entre o troquel e o palanquilla, uno a 300 graos e o outro a 1.400 graos. Durante a forza da prensa prodúcese un forte choque térmico e a consecuente fatiga térmica provoca gretas".
A redución da duración do troquel non foi un problema de ningún tipo e paira combatelo utilizáronse sprays de cera. Desta forma solucionáronse os problemas térmicos, pero os restos de cera tamén poden quedar pegados ao troquel.
Os comportamentos tixotrópicos non son novos. XX. Coñécense desde os anos 70 do século XX. Os ceramistas, por exemplo, coñecen moi ben o comportamento tixotrópico. Nos aceiros comezou a estudarse a partir dos anos 80. Mondragon Unibertsitatea quere chegar máis lonxe: "Agora estamos a traballar co aceiro até ver como xestionar estas altas temperaturas e tamén estamos a pensar en saltar a outros materiais con maior temperatura de fusión, como o titanio".
O reto do laboratorio ao taller
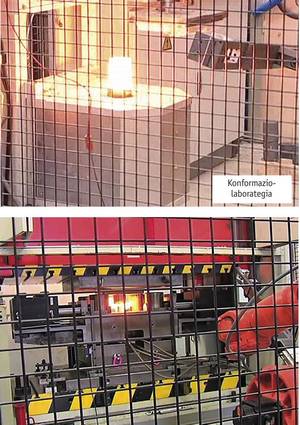
No laboratorio está a mirarse lonxe, pero segundo Mikel Intxausti aínda hai que traballar máis a tixoconformación antes de entrar no taller. "Aínda non está totalmente involucrado no proceso --di Intxaustik-. Si en Tixoforja existen algunhas dificultades paira poder forxarse totalmente industrialmente, hai que destacar que a duración dos troqueles é un gran problema e que a segunda é conseguir unhas características mecánicas adecuadas das pezas. No laboratorio estamos a avanzar no camiño, pero aínda non se pode incorporar ao proceso produtivo". Por tanto, aínda queda camiño por percorrer.
Tamén Jokin Lozares fala así. "A tixoconformación permítenos construír muros de aceiro máis finos, a posibilidade de facer máis nervios, superficies máis precisas, é dicir, a capacidade de facer pezas complexas. A diferenza de fórxaa, realizaremos pezas máis complexas, pero non tan complexas como as que se obteñen por fundición. Tamén se utiliza menor cantidade de material, o mesmo palanquilla inicial é un 20-25% menor e non se produce rebaba no proceso. En canto ás características mecánicas, as pezas presentan mellores propiedades mecánicas que en fundición, pero peores que as forxas. Ese é o reto".
O proxecto queda pendente de mellorar as características das pezas e axustar o proceso produtivo á industria. O presidente do CIC Margune, Iñigo Loizaga, con todo, ve con bos ollos o proxecto: "A tixoconformación non é nova, pero non avanzou o suficiente. Cando empezamos a mostrar o noso interese por este tema, na Universidade de Aachen, referente en Europa, dixéronnos que atopariamos grandes inconvenientes. E tivémolos, pero non tanto. Nun tempo razoable estamos a obter resultados optimistas e con pezas complexas. A propia empresa ha visto que a tixoforja pode pasar de laboratorio a fabricación. Non só iso, senón que nos demos conta de que podemos ir máis aló da automoción e do aceiro, por exemplo, á aeronáutica, con materiais basicamente de titano".
Ademais, desde o punto de vista do CIC, Iñigo Loizaga afirma que a experiencia está a ser excelente. "Dado que a tixoconformación é un salto tecnolóxico relativamente grande, é imprescindible a implicación dos investigadores de investigación básica, pero cunha visión moi competitiva e totalmente tradicional da industria forxa", destacou.
Ambos os mundos, as necesidades de investigación e industria, a colaboración entre empresa e universidade, recoñecen que non foi fácil, xa que as formas de traballo son moi diferentes. Con todo, conseguiron formar un equipo que leva anos xuntos, áxil e dinámico, o que lles leva a ver que as cousas están a saír. "Vemos que ten futuro, se superamos as dificultades que quedan, se rompemos as barreiras, teremos una vantaxe que nos axudará a ser máis competitivos", afirmou Loizaga.
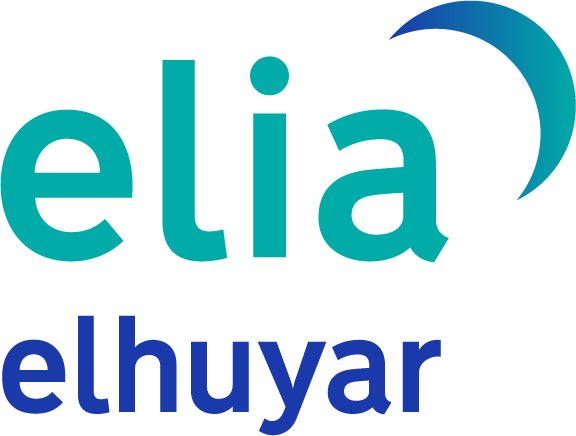
Gai honi buruzko eduki gehiago
Elhuyarrek garatutako teknologia