Sustainable alternatives for the development of thermostable materials
2024/10/14 Eider Fuentes Aguirre - eider.fuentes@gaiker.esGAIKER (BRTA), Konposite Jasangarriak eta Polimero Funtzionalak Saila | Patricia Ares Elejoste - ares@gaiker.esGAIKER (BRTA), Konposite Jasangarriak eta Polimero Funtzionalak Saila | Aitziber Iturmendi Aguirrebeitia - iturmendi@gaiker.esGAIKER (BRTA), Konposite Jasangarriak eta Polimero Funtzionalak Saila | Koldo Gondra Zubieta - gondra@gaiker.esGAIKER (BRTA), Konposite Jasangarriak eta Polimero Funtzionalak Saila | Rubén Seoane Rivero - seoane@gaiker.esGAIKER (BRTA), Konposite Jasangarriak eta Polimero Funtzionalak Saila Iturria: Elhuyar aldizkaria
Concerns about the environmental impact of current thermostable composites have led to the search for more sustainable alternatives. Sustainable reinforcements have been used for this purpose, and new thermostable resins with biological content and recyclable systems have been developed. Advances, further research is needed in search of new alternatives.
One of the most serious problems today is the depletion of crude oil, i.e. the shortage of oil-based products, but there are also serious environmental problems associated with oil consumption, such as pollution and climate change. This is why it is increasingly turning to research on renewable alternatives in composite materials. (2)
In recent years thermo-stable resins have been developed from renewable sources. They are not recyclable, but they represent a great improvement in terms of sustainability. For these materials to be more sustainable, the use of renewable reinforcements has increased.
THERMOSTABLE AND SUSTAINABLE RESINS
There is great interest in the development of these resins due to their properties. This type of resins, once polymerized, have the ability to form cross networks which contribute to the composite excellent chemical, mechanical and thermal properties. Epoxy, polyester, binylesters and bencoxacin (phenolic) stand out in this group of resins.
PFA resin
Furan resin is obtained from agricultural by-products, namely furan furfural, through biomass catalytic hydrolysis. This becomes an alcoholic femur that, by condensation reaction, gets the furan resin. This resin is suitable to replace the phenolic resin due to its thermal stability and good mechanical properties and durability.
Benzoxacin resin of biological origin
Thermostable benzoxacin resin is classified in the phenol family. In recent years great interest has been generated for its advantages: good thermal stability, absence of contractions... It is sustainable and flexible in molecular design and allows synthesis with phenols and amines from natural sources, such as lignin, from which compounds such as vanillin, eugenol and guayacol are obtained. These compounds allow the development of polybentzoxacin materials with different properties.
Epoxy resin of biological origin
Currently, epoxy resins are the most developed resins of biological origin. Its characteristics include low contraction, easy adaptation, good adhesion and high outdoor resistance.
Biological epoxy resins are obtained through two main routes: on the one hand, direct reaction with biological compounds and, on the other hand, epoxidation of double bonds. Biofuncated epoxy resins are divided into three groups: aromatic, aliphatic and completely biological. Cardinas, lignin and gallic acid are used as sources to produce aromatic resins. Vegetable oils, such as soy and castor, are used for aliphatic resins, as shown in Figure 2.
Polyester resin
Polyester resins are generated by condensation of acids and alcohols, forming cross nets. They have good mechanical properties and, compared to epoxy resins, they have a low cost. Interest in the use of renewable raw materials for the synthesis of resins such as itaconic acid has increased in recent times.
SUSTAINABLE REINFORCEMENTS
Natural fibres
Natural fibers, being resistant and rigid, have the appropriate qualities for their use in composites. Compared to traditional composites, composites made of natural fibres have attracted a great deal of attention in the industry, particularly because of their density and respect for the environment. Natural fibers are made up of numerous long chains of cellulose and lignin that bind together by hydrogen bonds to give solidity and stiffness. In addition to vegetable fibers, there are animal fibers such as wool, feathers and animal hairs, all of which are important resources.
Natural fibres - composite polymers
Natural fiber composites are materials formed by a polymer matrix. Robust natural fibres such as flax and jute are used for this purpose. Natural fibers are increasingly used, as they have a similar stiffness and resistance to glass fibers. Moisture, the hydrophilic character of the fibers and the number of fibers influence their properties. The chemical composition of fibers (cellulose, hemicellulose, lignin and waxes) is also determinant. Studies have been conducted on the suitability of these fibers, on the one hand with varied matrices and, on the other hand, with manufacturing processes for surface change.
Hybrid composites
Hybrid compositions of reinforced natural fibers are being developed with the objective of being environmentally more appropriate and responding to the demands of industries seeking sustainability. Hybrid composites develop by placing two or more natural fibers in a single matrix. Today, many researchers are trying to choose the best combination of natural fibers to harness them and minimize inconveniences.
Sustainable cores
Sandwich composite structures are two layers attached to a core that provide high compressive strength and bending, as well as higher stiffness, without significant weight gain. They are particularly useful in the aerospace industry, shipbuilding and the transport and construction industries.
Growing environmental awareness in recent years has led to research and development of sustainable cores. These materials, obtained from renewable and recyclable sources, offer benefits such as biodegradability and thermal and acoustic insulation.
RECYCLING OF COMPOSITES
In recent years, the accumulation of waste composite materials has generated some concern. That is why many countries have begun to study the reuse and recyclability of these materials.
This section will not describe each available recycling method for composite materials (mechanical, thermal and chemical recycling), but will present the most recent studies and developments on recyclable thermostable resins. Recent advances in recyclable thermostable resins include:
- Recyclable phenolic resins: A fully recyclable phenolic resin has been developed, with good recyclability and high thermal resistance, comparable to bitrimers. (4)
- Self-balancing epoxy resins: Self-rated and recyclable epoxy resin has been investigated, and mechanical and thermal properties have been obtained through the use of disulfide in its composition. (5)
- Recyclamine technology: enables the recycling of composite materials based on epoxy resin, for the recovery of reinforcements and the proper preservation of properties, using the diluted solution of acetic acid. (3)
- Elium resin: Recyclable thermoplastic resin based on acrylic monomers, with good mechanical properties and ease of processing.
- Akelite resin: It is an acrylic resin that can be recycled by immersing in the acetone, with good mechanical properties and thermoforming capacity.
These developments reflect a significant advance in the sustainability of composite materials. In addition, suitable mechanical and thermal properties are obtained, as well as increasing recyclability.
APPLICATIONS
Applications of biocomposites have become increasingly strong in Europe as a result of environmental regulations. In addition, Directive (1) EURO 6 penalises cars with CO2 emissions above 95 g/km and promotes the use of biocomposites to reduce these emissions. In addition, Directive 2000/53/EC sets the target of recycling 95% of the weight of cars, promoting the use of biocomposites.
Biocomposites have applications in different sectors. Among others: advanced electronics, aeronautics, automotive, etc.
In addition, the use of biocomposites is expected to increase in the coming years. According to a study, in the period 2018-2030, the composites market has been valued at $24.59 billion in 2021 and is expected to increase by 16.1% (1).
CONCLUSIONS
In conclusion, the review analyzes sustainable alternatives to conventional thermostable systems and highlights the need for further studies for the development of resins of higher biological content. Recyclable and thermostable systems have generous properties, and some, like Recyclamin, allow the material to be reused in the second life. Despite advances in sustainability, it is necessary to analyze more alternatives to address the environmental problem holistically.
BIBLIOGRAPHY
1 Andrew, J.J.; Dhakal H.N. 2022. “Sustainable biobased composites for advanced applications: Recent trends and future opportunities”. Compos.
2 Ares-Elejoste, P. Seoane- Rivero, R., Gándarias, I., Iturmendi, A. The gondola, named K. 2023.“Sustainable Alternatives for the Development of Thermoset Composites with Low Environmental Impact” Polymers 15 (13).
3 La Rosa, A.D.; White, I.; Banatao D.R. ; Pastine, S.J. ; Björklund, A.; Cicala G. 2018.“Innovative Chemical Process for Recycling Thermosets Cured with Recyclamines® by Converting Bio-Epoxy Composites in Reusable Thermoplastic—An LCA Study.” Materials 11, 353.
4 Liu, x.; Li, Y.; Shing, X.; Zhang, G. Jing, 10. 2021. “Fully recyclable and high performance phenolic resin based on dynamic urethane bonds and its application in self-repairable composites.” Polymer, 229.
5 Zhang, Y.; Yuan, L.; Liang, G. We, A. 2018. “Developing Reversible Self-Healing and Malleable Epoxy Resins with High Performance and Fast Recycling through Building Cross-Linked Network with New Disulfide-Containing Hardener.” Chem. Res.57, 12397–12406.
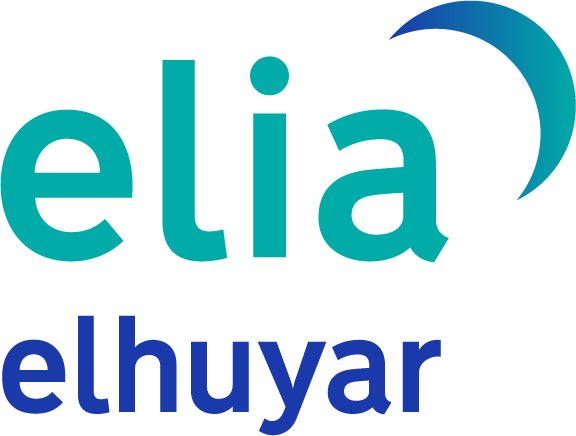
Gai honi buruzko eduki gehiago
Elhuyarrek garatutako teknologia