Analysis of the aging of composites
2023/12/05 Rubén Seoane Rivero - seoane@gaiker.esGAIKER (BRTA), Konposite Jasangarriak eta Polimero Funtzionalak Saila | Koldo Gondra Zubieta - gondra@gaiker.esGAIKER (BRTA), Konposite Jasangarriak eta Polimero Funtzionalak Saila Iturria: Elhuyar aldizkaria
The use of composite materials reinforced with fiberglass is increasingly frequent when replacing conventional materials. Increased demands in industrial sectors such as sustainability and chemical resistance must be taken into account. Therefore, this paper presents the design of glass fiber reinforced composites and the characterization of superficial aging.
Composite materials have very interesting characteristics: low density, low production cost, specific mechanical properties, corrosion resistance, dimensional stability against chemical or physical agents and good electrical and magnetic isolators[1,2,3,4]. They can be found in various sectors, but it should be noted that in the European market the construction sector is the one with the highest percentage of production, since the percentage of production of composite materials in this sector has doubled from the 1990s [5] to the present [6]. In the transport sector, the high percentage of production also stands out, which includes areas such as automotive and aeronautics.
This article analyzes the mechanical behaviour of BMC (Bulk Moulding Compounds) glass fibre reinforced composites and the aesthetic quality of the material surface under conditions that may occur in corrosive or outdoor environments. In recent years, the use of BMC in external applications has acquired special relevance, so it is necessary to know the influence of environmental factors and, in particular, the influence of UV radiation from sunlight, moisture or exposure to corrosive substances.
To analyze the properties of BMC different material formulations have been made, varying some of their components: resin, thermoplastic additive, filling and pigmento.El material has been shaped by the compression molding method. Test specimens have been machined for bending, tensile, colour and gloss tests. The results obtained were statistically treated by the ANOVA method using the Minitab 9.1 software. This statistical analysis has made it possible to draw conclusions about the relationship between BMC components and the material's mechanical and aesthetic characteristics, as well as to detect possible interactions between BMC components.
In total, 32 different formulations have been analyzed with 4 different resins (orthodox, vinilester, maleic and isoftálica), two additives (polystyrene and polyvinyl acetate), two fillers (hydrated alumina and calcium carbonate) and, finally, two types of pigments (titanium dioxide). These raw materials have been supplied by industrial partners and confidentiality agreements make it impossible to know the exact composition of these components.
The aging treatments performed have been based on the UNE standard; chemical treatments UNE 53316:2012 and UNE EN ISO 4892-3 UV exposure: Performed according to the 2016 standard. Bending tests (ISO 14125:1998/A1: 2011), tensile test (UNE-EN ISO 527-4: 1997), Barcol hardness tests (UNE 53270), colour measurements (UNE EN ISO 11664-1: 2011), gloss measurements (UNE-EN ISO 2813:1999) and composite filling content (UNE EN ISO 1172).
Figure 1 clearly shows that the type of resin is the most determining factor in variations of the average bending modulus. It highlights the low value of isoftalic resin (about 7 PG) and the high value of vinilester resin (over 9 PG). These results are based on information provided by other authors, who also show the same order in the values of the bending module (but in different magnitude) between isophthalic, orthophthalic and vinilester resins [6].
Regarding the tensile modulus, maleic resin presents a much greater rigidity than the rest of resins (greater than 10 PG), as shown in Figure 1. Other authors have reported this difference in tensile strength between orthophthalic and isophthalic resins [7].
Furthermore, the importance of the type of resin in the hardness values and, to a lesser extent, in the types of load and additives is highlighted. Maleic resin provides the highest Barcol hardness values (over 45), while isoftalic resin has a hardness value of about 36 Barcol, making it a softer resin. It is known that vinilester resin, when hybrid between polyester and epoxy, has higher values than orthophthalic resins and isoftallin6. Alumina presents higher hardness values than calcium carbonate. These results were expected because calcium carbonate is a soft material [8]. The type of additive also affects the results of hardness Barcol, since better results are obtained with PVAc.
Moreover, as expected, acid aging reduces the mechanical properties of the material, especially after the expansion of H+ ions in acidic solution to the surface of the fiberglass [9]. Resins, loads, additives and reinforcements contain a large number of sulphuric acid soluble elements which, upon contact with it, can be leached and released from the matrix and cause BMC degradation. Calcium carbonate is the worst exposure to acid. However, its use offers better stiffness results. In spite of chemical aggression, alumina use is still very beneficial for material hardness, since a 10 Barcol hardness unit difference has been obtained with respect to calcium carbonate.
Ultraviolet (UV) radiation from sunlight or other sources can cause degradation of polymeric materials, altering the molecular weight and reticular structure. This degradation or aging is usually attributed to the photooxidation mechanism. In long polymeric chains, this radiation causes the breakdown of carbon-carbon bonds to form vinyl, methyl and aldehyde, giving the material a yellowish color [10].
The main effect of UV radiation is the dark surface of composites, although in most cases long radiation causes an alteration of mechanical properties[11,12]. In the case of color change, there are two factors that especially influence the results: the type of resin and the type of filling. It is worth mentioning that orthophthalic resin is the least harmful due to UV degradation, although it also highlights the good response of maleic and isophthalic resins to UV radiation. As for fillers, calcium carbonate is less harmful than alumina.
Regarding gloss, the only significant factor after UV exposure is the type of resin. In this case, maleic and isophthalic resins are the most aesthetically damaged.[13] The influence of UV radiation on BMC formulations is shown in Figure 2.
This article analyzes the main mechanical and aesthetic properties of BMC composites after chemical aging and UV radiation. Some of the conclusions obtained in this study are:
- Vinilester resin has better mechanical properties than orthophthalic and isophthalic resins.
- Aluminium filling is more suitable than calcium carbonate filling for applications requiring high stiffness and hardness with respect to bending.
- Higher hardness values are obtained with maleic resin, polyvinyl acetate supplement and filling alumina.
- Regarding the aesthetic aspects (color and gloss), it is generally observed that attacks affect less orthophthalamic resins than vinilester resin.
Finally, it should be noted that the work performed is an excellent analysis for a wide range of applications that allows selecting the best BMC formulation for protective coatings for the automotive, electricity and construction sectors, among others.
Bibliography
1 Thread, V.N., Abdulrahman, A.S., Zubairu, P.T., Isezuo, S.L., Abdulrahman, M.A. and Onuoha, D.C. 2014. “Prospects and Challenges of Composites in a Developing Country”. ARPN Journal of Engineering and Applied Sciences .9. 1070-1075.
2 López, F.S., Ferrer, C., Salvador, M.D. and Friend, V. 2002. “Flexural Characteristics of Tango-Aged Polyester Composites: Influence of Processing Protectors”. Journal of Testing and Evaluation. 30. 20-26.
3 Ilhan, R. and Feyzullahoglu, E. 2021. “Investigation of adhesive wear properties of glass fiber reinforced polyester composites having different chemical compositions”. Journal of Engineering Tribology. 236. 156-173.
4 Winkler, M. 1990. “Automotive Under-the-Hood Applications in Vinyl Ester Resin SMC/BMC”. Journal of Materials and Manufacturing. 99. 675-690.
5 Witten, E. and Mathes, V. 2020. The Market for Glass Fibre Reinforced Plastics (GRP) in 2020: Market developments, trends, outlook and challenges. AVC.
6 in Zweb, C.H. and Beaumont, P. 2017. “Comprehensive Composite Materials II”. 2. 360-400
7 Middleton, B. 2015 “Design and Manufacture of Plastic Components for Multifunctionality”. William Andrew. 1. 53-101.
8 Miravete, A. – Your Technology and Recent Developments.” Miravete. March 2019. Vol.1. p.12-26.
9 Sahin, Ö.S., Akdemir, A., Avci, A. and Gemi, L. 2008. “Fatigue Crack Growth Behavior of Filament Wound Composite Pipes in Corrosive Environment”. Journal of Reinforced Plastics and Composites. 28. 2957-2970
10 Segovia, F., Ferrer, C., Salvador, M.D. And Amigó, V. 2000. “Influence of processing on mechanical characteristics of sunlight aged solvent-glass fibre composites”. Polymer Degradation and Stabilizer. 71.179-184.
11 Peters, S.T. 2018. “Handbook of Composites”. Springer, Boston, MA... 2.
12 Barczewski, M. and Matykiewicz, D. 2016. “Application of waste bulk moulded composite (BMC) as a filler for isotactic polypropylene composites” J. Adv. R. 7. 373-380.
13 Matykiewicz, D. and Barczewski, M. 2015 “Morphology and thermomechanical properties of epoxy composites highly filled with waste bulk molding compounds (BMC)” J. Polym. Eng. 35, 805-811.
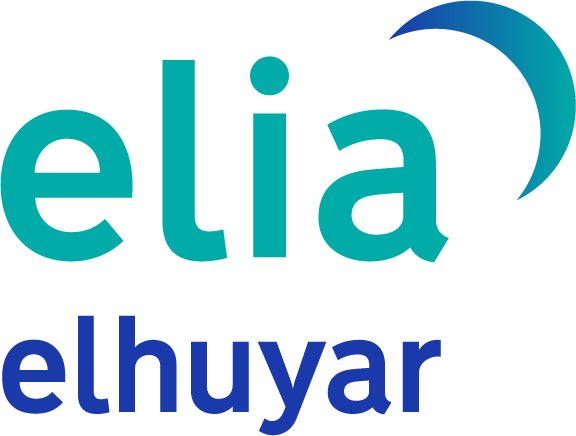
Gai honi buruzko eduki gehiago
Elhuyarrek garatutako teknologia