State-of-the-art technology in tunnels
2003/02/01 Kortabarria Olabarria, Beñardo - Elhuyar Zientzia Iturria: Elhuyar aldizkaria
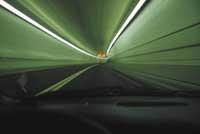
The tunnels are very special works, since most of the time they are underground works. The sizes can be large, like those of La Mancha, with numerous kilometers of 6-8 meters in diameter, medium or very small, to the point that humans cannot enter. In towns and cities tunnels can be an opportunity to improve transport routes or improve sewer and water service.
Before starting with the execution of the tunnels, it is necessary to conduct thorough studies of the soil, especially to know the type of terrain on which it will be found and see if there is groundwater or not. Depending on the characteristics of the ground, the existence or not of groundwater and the use to be given to the tunnel, the tunnel execution system is determined.
If the ground is stable, drilling work can be done mechanically. If large amounts of groundwater are not found in the surveys carried out before construction, in most cases it is not necessary to pressurize the areas in which the work is to be carried out. If water is detected, on the contrary, these areas are pressurized to prevent water from reaching the work areas.
Both for the construction of large road tunnels and for the railroad, when the terrain is stable, drilling can be done by machine. These machines are called TBM ( Tunnel Boring Machine). They are machines that pierce the entire front of the tunnel. The truth is that it is a train made up of several machines, each with its own engine, which allows them to move on the track. On the front the TVDs have a cutting head. This head turns and pulls back everything that pierces and breaks the rock. Behind the cutting head is hidden. In addition to providing protection, the tunnel coverage is placed through the shield. To do this, in secret, despite the lack of space, the necessary equipment is available to move and place the candles. The work is not easy, since dovelas are usually pieces of more than a ton.
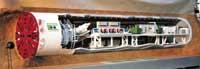
be seen in the model, due to the size of the machine, inside there are numerous places for both operators and tools.
Some of the most outstanding features of this machine are:
8,430 millimeters.
9,070 millimeters.
9.330 millimeters.
8,830 millimeters.
capacity: 2,000 kW.
Electrical capacity of tunnel machine: 4,000 kVA.
With this type of tools the dovelas of the coating rings are placed in position, being able to be filled between rings with lime grout. In turn, the hidden tooling sends back all the sand extracted from the hole. Also hidden are the electric motors and hydraulic pumps that drive the movement of the rotary head and move the tools that place the cranks in position.
When the earth is not stable, that is, it cannot be hidden, it is pierced in another way. In these cases cutting machines are used on the front of the tunnel. The rubble falls to the ground and collects the excavators and transports them to trucks. Through this technique, tunnels that do not have a circular section are constructed. In
these cases, it is necessary to cover the tunnel as it progresses, since the terrain does not have the sufficient resistance to remain complete without coverage. Falling ceilings and walls of tunnels if not covered is very easy, which makes accidents frequent. The coatings are made with concrete, either by prefabricated structures or by metal structures located in the tunnel itself.
When the earth is very hard, hard rock, the forehead is usually opened by an explosion: small holes are made, the explosive is placed and the hole is extended. The construction works of the tunnel begin next. That said, the work seems simple, but getting the amount of explosives needed is very difficult. In fact, if you hit, you get rocks of suitable size that fall where necessary. This facilitates the extraction of all these rubble. In hard rock tunnels, most of the time no cover is made, but they are cut to have a flush surface. However, in the event that the rock is easily broken and there is a risk of detachment of rock fragments, the coatings are made with prefabricated concrete.
The choice of one or another tunnel construction system does not exempt the importance of making suitable accesses both for the entry of work material and for the evacuation of debris. The lack of space is usually one of the biggest drawbacks of the construction of the tunnelling, since it is usually limited in its front and the possibility of other works inside the tunnel is usually not excessive.
Drilling or exploding?
The balance between time and security has made for many years an open debate in the manufacture of tunnels, what is the best tunnel construction system? The debate has been between supporters and detractors of the use of drilling machines for tunnel construction.
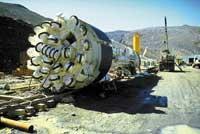
As for the safety of the personnel going to make the tunnel, it seems clear that the use of tunnel construction machinery is much better. In fact, in open-front tunnels and large diameters accidents and subsidence are relatively frequent.
TVD in long tunnels
The world's longest large section tunnels have been built for roads and roads. Hydraulic tunnels can also be long, but generally have a much smaller section. Until the end of the Seiki tunnel in Japan, most of the world's largest tunnels, except those in La Mancha, have been built without tunnel machines, drilled and caused by the explosion. However, the Seikan tunnel has served to modify the construction of the tunnels.
In Japan there were many problems with drilling and explosions. The construction projects of the large tunnels that have been launched since then are being carried out with giant tunnel machines. The new San Gotemá, two 57 km tunnels, the new Loetschberg, two 45 km tunnels, Guadarrama, two 30 km tunnels, Mont Cenis Lyon-Torino, two 45 km tunnels, and, in general, the giant drilling machines for the construction of large railway tunnels and high-speed tunnels. Therefore, tunnel machines are being imposed.
The Channel of La Mancha is one of the largest tunnels built with tunnel machines and one of the most built in the world, although 10 operators died in construction. As is known, the canal consists of three tunnels, two of nine meters in diameter for the train, among which is a service tunnel of six meters in diameter. The construction work of each of these tunnels was divided into two parts, the French and the English.
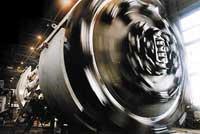
Each of these parts was divided into two other parts, the marine and land, so the project was built in 12 parts. However, in the construction of the tunnels only 11 tunnel machines were used, since two tunnels of the French land, of more than 17 kilometers, were drilled with the same machine. In the work of La Mancha the English used open machines to manufacture tunnels and the French used closed machines to build tunnels. The English drilled an average of 800 meters a month, while the French did 700. In fact, open tunnel machines are faster than closed ones, since in order to continue drilling they do not need to place a ring.
Logically, when drilling, in addition to the type of machine, the characteristics of the ground or rock have a great importance, since depending on it you will have to choose a drilling system or another.
According to experts, tunnel machines are only cost-effective when tunnels are long. This type of machine is made to order and takes a year to become one. This argument has often been mentioned by supporters of using open front systems for tunnel construction. However, it seems that the debate is coming to an end.
Underground but safe
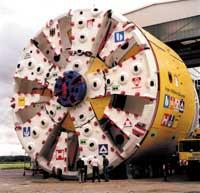
The accidents that have occurred in European tunnels in recent years, with many injuries and deaths and large economic losses, have highlighted the need for efficient safety and rescue systems in tunnels. To date, the safety factor has not been very important when designing tunnels. There was no possibility of accidents, so safety and rescue systems were scarce. The accident in March 1999 in the Mont Blanc tunnel revealed the need to start doing things differently.
In fact, the tunnel construction technique has advanced a lot. This has allowed us to build longer and more dense tunnels, especially for trucks. Therefore, the chances of accident are also greater. Experience has shown that tunnel accidents are serious.
The countries of the alpine area are the ones that have advanced the most when it comes to combining tunnelling and safety due to the most terrible accidents: France, Switzerland, Italy and Germany. During the Mont-Blanc accident, these four countries constituted a security commission to analyze the state of the long tunnels. This committee issued a report that concluded that in terms of safety, the tunnels of the Alps had much to improve. Following this report, the French government completely modified tunnel regulations, establishing safety as a priority. In addition, a working group on tunnel safety has been established, which meets every two years in France. The renovated Mont Blanc tunnel ( http://www.atmb.net/) is the clearest example that is changing things.
However, in the tunnels there are not too many accidents. The number of accidents on the other roads is much higher. Tunnel accidents do not account for a third of the total. Most of the accidents that occur in the tunnels are due to collisions with the side walls and cars that go in front or come back. In dual-direction tunnels, frontal collisions are also relatively frequent. If there is no fire in these accidents, if there is no dumping of dangerous substances… the accident will not have a great impact, but when disasters occur the society is altered. Experts say that if 20 accidents occur outside the tunnels and 20 people die, nothing happens, but if in a single accident occurred in the tunnel 20 people are spoken of…
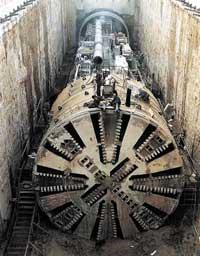
However, more and more measures are being taken to ensure tunnel safety.
Arcenes and sidewalks are
mandatory in all new tunnels. The arcenes will have a minimum length of two meters and the sidewalks of a meter and a half. In double-steering tunnels of more than 300 meters, with trucks broken to its edge, they must be enough to cross two vehicles without obstacles.
Protection zones for people must have a capacity of between 50 and 100 people. To date they have been placed between 700 and 1,000 meters, but are currently being placed 500 meters from 350. In order to receive external messages they must have speakers and television screens. Also, they should be prepared to stay long. These protection areas have an independent ventilation system, independent of the tunnel ventilation system. According to the new regulations, the protection zones must be able to go outside through the evacuation routes.Fire and safety niches They are holes of more than
two meters in height, equipped with light reflectants, electrical panels, emergency postcards and extinguishers. They will be located at a distance of 200 meters on both sides of the tunnel.In case of a
breakdown or accident, the tunnels are located to the right of the direction of traffic. They must allow long trucks to enter.People's escapes are galleries that
must allow direct exit to the outside of the tunnel. When it is not possible directly, they can link with ventilation tunnels or false ceilings, whenever possible their exit.Direct evacuation
tunnels outside the tunnel.Diverse equipment
Fire water network, compressed air systems and waste recovery systems.Safety moat in the Mont Blanc tunnel.ATMBThermal doors
This safety system was first used in the Frejus tunnel between France and Italy after the Mont Blanc accident. It has given very good results. The goal of the system is to control whether trucks entering the tunnel are overheated. Before entering the tunnel, a truck stop zone was enabled. It passes through the thermal door and the scanner of the truck is carried out with the help of the computer. The thermal sensors installed on the door allow obtaining the vehicle temperature map. Control of tires, brake pads, motor, driver's cab, etc.The
signalling system is basic to ensure traffic safety. The user is informed of the location of the protection areas, location of the wall or fire pits, stop, speed to which it can circulate... Traffic lights, message panels, tunnel closure barriers, alarm lights, reflective paints leading to the escape routes, etc. are placed.Ventilation is of great importance in the usual
use of tunnels, while in the case of fires the proper ventilation system is essential. In addition, several systems are needed: the natural tunnel, which is obtained by fans, exhaust ventilation systems, etc.Communications Their
importance is that they serve users to indicate at all times the state of tunnel traffic. He is currently implementing and using telephony, television and radio systems.The
control system is using closed TV circuits and automatic accident detection systems. In the tunnels are installed television cameras that can be monitored from the control room. Mainly used for traffic control. The automatic image detection system aims to detect in real time possible traffic incidents. This system is based on digital image processing techniques.Fire
detectors Smoke detectors, heat detectors and TV fire detectors are used.
For the tunnels to become safer, the situation of the soil, the density of traffic, the existence of many or few curves, the lighting against claustrophobia… are factors to consider and necessary because, despite the few accidents, those of the tunnels are a dramatic accident.
Longer tunnels
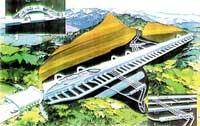
The longest road tunnel in the world is San Sebastian, in Switzerland, which became famous for the 2001 accident. It opened in 1980 and has 16.3 kilometres. In Switzerland there are also the two tunnels of Seelisberg, with 9 kilometers each. Arlberg, in Austria, has 13,973 kilometers; Frejus between France and Italy, 12,8 kilometers; Mont-Blanc, which joins both countries, 11,6 kilometers. In addition, the list of the longest include three Japanese tunnels: Kan-etsu tunnel 10.86 kilometers, Asa 8.6 kilometers and Ena-San 8.4 kilometers.
The longest tunnels on the tracks are in Japan, Seika with 53.9 kilometers and Dai Shimizu with 22.23 kilometers. One of the largest tunnels in Europe are the Alps and Apennines: Simplon Switzerland of 19.8 kilometers; the tunnel of the Apennines that connects Florence with Bologna; the Mont Cenis of the Alps of 13.6 kilometers; San Gotardo of 15 kilometers; the tunnel of Lötschberg of 14.6 kilometers, etc.
A little history The history of tunnels and mining begins at once. The oldest mine in the world is 40,000 years before Christ, located on the Bomvu hill in Swaziland. This mine was used for hematite extraction. The first tunnels were opened with fire. Where they had to start to pierce it became fire and suddenly it was extinguished with water. Thus, due to the temperature variation, the rock was cracked and therefore they could start working. About 2,500 years ago, the architect Eupalinos built a tunnel of more than a kilometer in length that led to the Greek city of Samos. His men worked on both sides and found themselves in the center. Nobody knows what the Greek did while working so that the tunnel would not be filled with water, but with a suitable slope he managed to move the water from Mount Kastron to the city. Years later, 35 years before Christ, near the city of Naples, opened a tunnel of 1,500 meters in length and 4 meters in width. There are other examples of ancient tunnelling, such as the gold mines opened at the time of Trajan (98-117), Lugo (Montefurado) and Leon (Las Medulas). XII channel construction tunnels. It began to be manufactured in the 20th century in France with the Midi channel. Although there were already many advanced techniques (note that in the time of the Eupalines the tunnel had not even been sent), the tunnel revolution was about to arrive. That XIX. It was in the 18th century that British engineer Marc Isambard Brunel came up with the idea of using a cylindrical tunnel protection to protect tunnel workers. As they drilled the cylinder was carried forward and they could take the floor out. After the drills, the stonemasons built the tunnel wall. This technique was first used in a tunnel under the Thames in 1843. Undoubtedly, the advance was remarkable, since until then there was no protection in the manufacture of tunnels. Around it, the tunnel of the port of Lizarraga is the same way, as it began to be built in 1853 and ended in 59. For the tunnelling industry it was more important than the tool of the engineer Brunel the appearance of the train. Trains don't like to go up and down, or move around curves. Thus, for the bridge and tunnel industry, XIX. The second half of the 20th century was more prosperous than prosperous. The great tunnels of the Alps, such as Mont-Cenis, San Gotardo or Simple, are from that time. In the coming years, tunnel manufacturing has great challenges. High-speed trains or urban underground trains require as flat and straight routes as possible. Therefore, tunnelling is currently on the rise. |
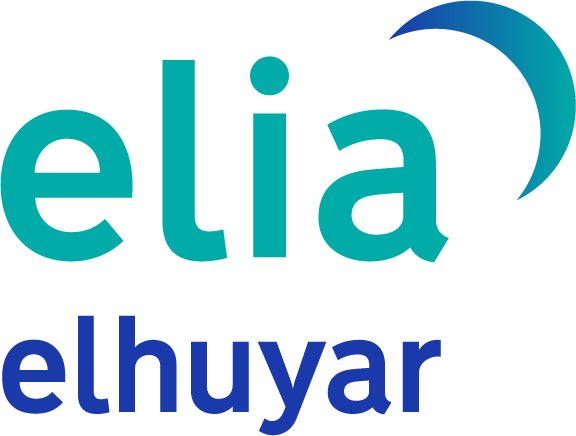
Gai honi buruzko eduki gehiago
Elhuyarrek garatutako teknologia