The robot on foot prepares for a hard ride
1986/08/01 Lizaso, Pili - Informatika SailaElhuyar Fundazioa Iturria: Elhuyar aldizkaria
At the International Conference on Advances in Robotics last year in Tokyo, the most surprising piece of hardware was the robot on foot.
The haul robot is known as an adapted suspension vehicle (ASV) and was built with the help of 5 million dollars offered by the Agency for the Defense of Advanced Research Projects in the US.
ASV looks like a mixture between the camel of three concave and the blanket of nuns. But Kenneth Waldron, head of the group that built the robots at Ohio State University, says it's the most sophisticated test ever done among walking vehicles."
This vehicle is designed to travel on ploughed land. The advantage of this tool with wheeled vehicles is the ease of passing over a major obstacle.
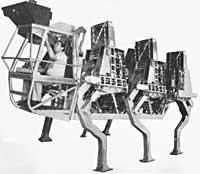
It is considered that the ASV is able to pass without avoiding ditches three meters wide and obstacles two meters high.
In addition to the body, it is important to have device sensors. "Having an optical sensor won't be too helpful if you don't know the direction being pointed out," says Waldon.
ASV has a length of 5 meters, weighs 2.72 tons and is able to transport 90 kilos.
It works with an adapted 50 kilowatt moped motor and can reach a speed of 3 kilometers per hour.
An optical radar located at the top of the cabin of this vehicle indicates to the driver the direction of its march.
A gallium arsenide laser produces an infrared ray that is reflected in a mechanical mirror system and analyzes the front of the vehicle. These reflected infrared rays are analyzed using five single-function computers. Another 10 single-function computers coordinate the movement of the legs, reading orders from the guide and sending information to the cockpit screens.
At the top of the cabin there are two screens. The one on the left indicates the legs on the floor at all times. The right is the exact state of all legs.
To complete and launch the construction of ASV, Waldron and his team had to solve a number of technical problems. One of the biggest problems was the supply of a large number of pieces that move independently, with great efficiency and good control.
"You have to achieve great efficiency, you have to equip yourself with capabilities," says Waldron.
This year, when all software modules are ready, ASV will have six types of operations to meet its objectives in different areas. For this it is necessary that the concrete step when the operator has each leg under control, a closed circuit mechanism in which the computer of the useful channels each leg; a fully automated mechanism, in which the succession of the legs is not predefined, since it depends on the ground; a crossed mechanism designed to move faster through rough terrain, and a push mechanism, which in its entirety is similar to the crossed mechanism, but eliminating with more information of a sensors.
ASV was built in May. The week before the realization her individual legs moved for the first time. Initially the tests were performed using a desktop system. However, this year will be fully automated.
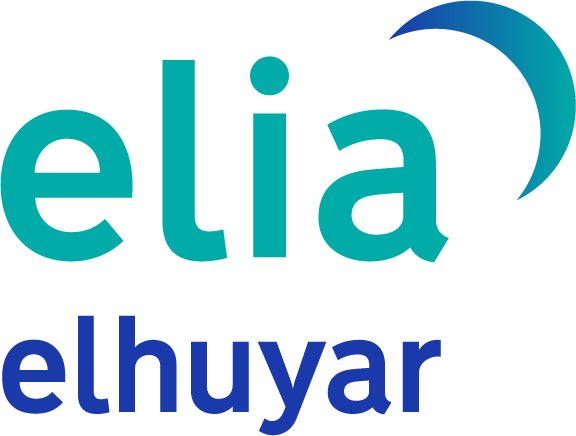
Gai honi buruzko eduki gehiago
Elhuyarrek garatutako teknologia