Diseño microestructural de cerámicos y cermets para herramientas
1995/02/01 Barandika Argoitia, Miren Gotzone - Kimika Ez-organikoa saileko ikertzaileaEHU Iturria: Elhuyar aldizkaria
La tecnología actual sigue el aumento de la velocidad de corte (Figura 2). Desde el punto de vista de las herramientas de corte, este aumento de la velocidad genera dos efectos principales: por un lado, las tensiones que deben soportar las herramientas son cada vez mayores y, por otro, las temperaturas que se alcanzan durante el corte son cada vez mayores. Para estas condiciones adversas es necesario utilizar materiales adecuados, es decir, materiales resistentes y resistentes a altas temperaturas. La dificultad también es importante en los procesos no continuos, ya que los materiales deben ser capaces de soportar choques mecánicos.
En este trabajo se analizará el diseño microestructural de cerámicos y cermets para herramientas, ya que las propiedades de estos materiales son adecuadas a las duras condiciones de corte mencionadas. Debido a la falta de dificultad de los cerámicos, las características de estos materiales no se han entendido ni utilizado correctamente. Sin embargo, en la última década se han investigado más sobre estos materiales que en los últimos 40 años. El desarrollo de las cercas ha sido completamente diferente, con la utilización de carburos cementados desde hace tiempo. No obstante, debido a que el diseño de estos materiales tiene mucho que ver con la problemática de los cerámicos, conviene analizarlos conjuntamente. Por otro lado, con el fin de aclarar algunos aspectos de esta obra, se han comparado materiales metálicos, ya que el comportamiento de estos materiales es más conocido para todos.
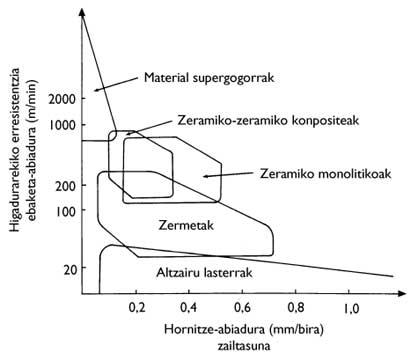
De los compuestos al material: microestructura
Las cerámicas estructurales se basan en compuestos químicos como los siguientes: nitruros (Si 3 N 4 , TiN, ...), carburo (WC, SiC, ...), óxido (Al 2 O 3 , ZrO 2 , ...) y boruro (TiB 2 , Zr2 , principalmente ...) Desde el punto de vista de la fabricación de herramientas, la idoneidad de estos compuestos radica en las relaciones químicas entre sus elementos. Dado que estas uniones son muy resistentes y direccionales, las estructuras cristalográficas de estos compuestos son muy resistentes y rígidas (casi indeformables), manteniéndose estas propiedades a temperaturas muy altas. Asimismo, estos compuestos, por su estabilidad química, son capaces de mecanizar prácticamente cualquier tipo de material. Sin embargo, las características de las cerámicas estructurales no sólo están presentes en los compuestos sino también en la microestructura.
En general, la fabricación de cerámicos se realiza mediante tecnología de polvo (Figura 3), al inicio del proceso, utilizando componentes de materiales (compuestos químicos) como polvo. Debido a que las partículas de estos polvos son monocristales del compuesto, su comportamiento es intrínseco. La fabricación de cerámicas estructurales a partir de estos polvos se limita a la generación de uniones entre partículas. Esto último se consigue mediante la fijación y sinterización de los polvos. En estos dos procesos, la temperatura y/o la presión permiten obtener un material compacto formado por ejemplares monocristalinos.
En el proceso ideal, no debe haber huecos entre partículas en todo el volumen del material, por lo que la densidad del material debe corresponder al compuesto químico. Desgraciadamente, a lo largo del volumen del material se pueden encontrar a menudo poros. También pueden existir impurezas derivadas del proceso de fabricación (Figura 4). Por otro lado, las denominadas dimensiones, morfología y distribución de los ejemplares condicionan las uniones entre los mismos. Por tanto, los aspectos mencionados definen la microestructura. Por ello, los materiales elaborados con el mismo compuesto pueden presentar diferentes microestructuras (Figura 5).
Debido a la distorsión de la distribución espacial entre los elementos tanto en defectos de la microestructura (huecos e impurezas) como en los límites entre los granos, sus uniones son más lentas que entre los átomos del interior de los granos (Figura 6). Por tanto, los límites y defectos son puntos débiles de la microestructura. Esto hace que las propiedades mecánicas de los materiales sean peores que las de sus componentes monocristalinos (compuestos químicos).
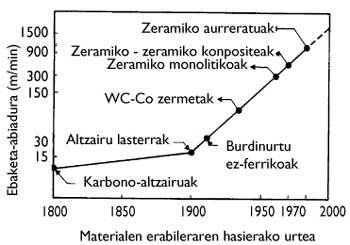
Problemática de los cerámicos
En el campo de los materiales estructurales, el comportamiento mecánico se describe con las siguientes propiedades: dureza, rigidez, resistencia a la rotura y dificultad.
Debido a la dureza de los cerámicos, son materiales muy apropiados para la fabricación de herramientas de corte de alta resistencia al desgaste. Por otra parte, su rigidez hace que su deformación sea muy reducida cuando se encuentran bajo la zona de tensión. En la figura 7 se puede observar que los materiales cerámicos son capaces de soportar tensiones superiores a las metálicas.
Sin embargo, la problemática de la aplicabilidad de los materiales cerámicos radica en su comportamiento frente a la rotura. Tal y como se indica en la Figura 7, la superación de la tensión máxima soportada por los cerámicos permite una rotura inmediata de los materiales. Debido a la falta de deformabilidad, estos materiales no pueden ajustar la tensión “sobrante”. Por tanto, la rotura de cerámicos es catastrófica (como cuando un plato cae al suelo). Los materiales metálicos, una vez superada la tensión máxima correspondiente, se deforman plásticamente antes de romperse. Estos materiales hacen que las tensiones se adapten mediante la deformación, ya que los granos de la microestructura son dúctiles. A modo de ejemplo, en caso de impacto, se pueden citar los escalones que se producen en los automóviles.
El rendimiento de los procesos es muy importante en cualquier actividad industrial. Por lo tanto, desde este punto de vista, las herramientas que se rompen catastróficamente parecen poco adecuadas. Sin embargo, teniendo en cuenta que el resto de propiedades de los materiales cerámicos son muy adecuadas, se ha realizado un esfuerzo científico importante para mejorar el comportamiento frente a la rotura de los cerámicos.
Los parámetros que definen la rotura son la resistencia a la rotura (que indica la máxima tensión soportada por los materiales) y la dificultad (que es proporcional a la energía absorbida por los materiales en el momento de su rotura). Por supuesto, la escasa dificultad de los materiales cerámicos es el mayor problema en las operaciones de corte.
Como se ha comentado anteriormente, el comportamiento de los materiales debe definirse en dos niveles: compuestos químicos y microestructuras. Dado que el comportamiento intrínseco de los compuestos químicos es inmutable, la única forma de mejorar el comportamiento mecánico es mediante el cambio de la microestructura. Para ello es conveniente conocer el procedimiento de rotura.
En la rotura de materiales intervienen dos procesos:
- formación de grietas (cuando se supera la tensión crítica)
- incremento de fisuras (aprovechando la energía suministrada por la zona de tensión)
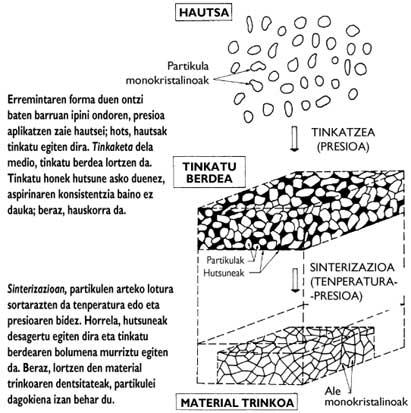
Fundamentos de diseño de cerámicos
Teniendo en cuenta los procesos implicados en la ruptura se puede concluir que:
- cuanto más difícil es crear fisuras, mayor es la resistencia a la rotura
- cuanto mayor es la energía absorbida por la fisuración, mayor es la dificultad
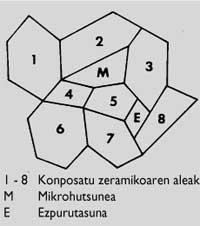
En cuanto a las cerámicas monolíticas, se ha actuado sobre las siguientes. Por un lado, las microestructuras están logrando cada vez más limpias, es decir, microestructuras con pocos defectos. De este modo, la probabilidad de formación de grietas disminuye y la resistencia a la rotura de la microestructura se acerca al valor correspondiente al grano monocristalino. Asimismo, si los defectos están más alejados entre sí (por su escasa presencia), el material debe absorber más energía para que las grietas crezcan, ya que el crecimiento de las grietas se debe a la interconexión de microfibras generadas en los defectos. Por lo tanto, también se puede mejorar la dificultad. Por otro lado, se están obteniendo microestructuras cada vez más finas, ya que cuanto más pequeños sean los granos, mayor es la resistencia a la rotura.
Para lograr los dos objetivos indicados, los polvos utilizados son de alta pureza y partículas reducidas. Asimismo, para que la densificación sea total y no se contagien los recalces, se están utilizando sofisticadas técnicas de fabricación.
Si bien el comportamiento mecánico de las cerámicas monolíticas así obtenidas es significativamente mejor, no es la única vía de diseño. De hecho, desde cerámicos monolíticos se han desarrollado composites cerámico-cerámicos y cerámico-metálicos.
Composites cerámico-cerámicos
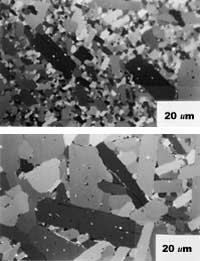
Estos composites están formados por dos compuestos “cerámicos”. La estructura granular compuesta por el mayor número de compuestos se denomina matriz. Los ejemplares del otro compuesto se distribuyen homogéneamente a lo largo de la matriz. En función de la función de esta segunda fase se distinguen principalmente dos materiales cerámicos de corte:
- Reforzados con partículas
- Reforzados por una fase transformable
Los ejemplares del segundo compuesto de composites reforzados por partículas, al no estar unidos entre sí, se denominan partículas (Figura 8). Debido a que las matrices provocan una fuerza contra las partículas para dispersar las tensiones externas, éstas dependen de una zona de tensión compresiva. Por tanto, para soportar la zona de tensión, las partículas deben ser más rígidas que las matrices. Este campo de tensión impide tanto la formación de fisuras como el crecimiento de fisuras. En cuanto a la formación de fisuras, debido a que las partículas se convierten en puntos de acumulación de tensiones, el material puede soportar una mayor tensión.
Por otra parte, la aparición de grietas hace que las partículas dificulten el crecimiento de las grietas, ya que éstas no pueden atravesar la zona tensional que rodea a las partículas. Por tanto, al aproximarse a una partícula, la fisuración cambia de dirección (Figura 8). Así, el camino que deben recorrer las grietas es mucho más largo y los materiales deben absorber más energía, es decir, la dificultad es mayor. En este campo se pueden citar los composites Si 3 N 4 (Figura 9) reforzados con partículas SiC y SiC reforzados con partículas TiB 2.
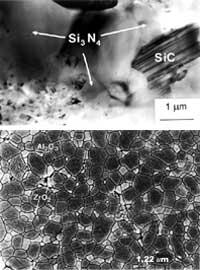
En los composites reforzados por una fase transformable, la segunda fase cerámica rodea los granos de la matriz. Esta segunda fase se encuentra en una situación metaestable. Así, cuando está sometida a tensión crítica, esta fase se transforma a su estado estable. La absorción de energía en esta transformación aumenta la dificultad del composite. Por otra parte, en algunos casos, junto con la transformación, también aumenta el volumen de la segunda fase.
Esta fase produce entonces fuerzas de compresión sobre la fase principal. Por lo tanto, comparando con los composites reforzados con partículas, aunque se produce un efecto contrario, se consigue el mismo efecto. Así, las grietas deben absorber más energía para atravesar estas zonas de tensión. Por tanto, esta es otra vía para mejorar la dificultad. En estos composites cerámico-cerámicos la resistencia no aumenta, ya que las grietas se generan bajo la máxima tensión que puede soportar la matriz. En estos composites cerámico-cerámicos se puede citar el Al 2 O 3 reforzado mediante la fase transformable ZrO 2 (Figura 9).
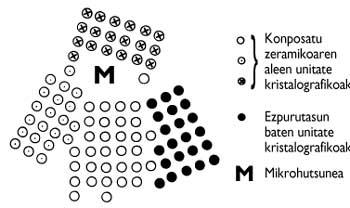
Composites cerámico-metal: cermets
La base del diseño de estos materiales es muy simple, es decir, consiste en dotar a los ejemplares indeformables de cerámicos de una capacidad de dispersión de tensiones. Para ello, las cercas, en torno a los granos duros, presentan una fase dúctil que hace que las tensiones se modifiquen. Por supuesto, esta fase dúctil es metálica y las cercas son híbridas entre cerámicos y metales. Por ello, la resistencia, dureza y rigidez a la rotura de las cercas son menores que las cerámicas, mientras que la dificultad es mucho mayor (Figura 7).
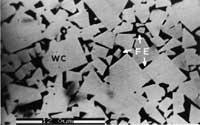
Para que el par “Compuesto cerámico fase dúctil” sea adecuado es necesario cumplir una serie de requisitos. Es decir, que las fases duras y metálicas sean químicamente compatibles. Por otra parte, para compactar el material, las dos fases deben adherirse entre sí. Las parejas que cumplen estos requisitos están constituidas por los carburos (WC, TiC, TaC, ...) y boruros (TiB 2 , ZrB 2 , ...) de algunos metales de transición y los Fe, Co y Ni del grupo VIII del primer período de metales de transición.
En estos materiales híbridos hay que mencionar los carburos cementados WC-Co, que fueron los primeros (inventados en 1929). La fase metálica es líquida en la sinterización de estos materiales. De este modo, en la refrigeración los ejemplares cerámicos sólidos quedan fijados en la microestructura. Dado que la fase líquida actúa como cemento, estos cermets se denominan cementados. En base al par WC-Co, las herramientas de la familia (WC, TiC, TaC)-(Co, Fe, Ni) son las más utilizadas en los procesos de corte del acero, siendo los componentes principales WC y Co mencionados (Figura 10)
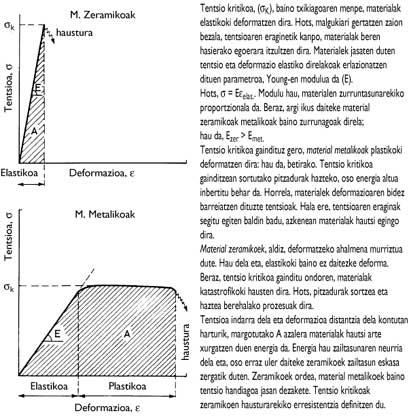
Mirando hacia delante
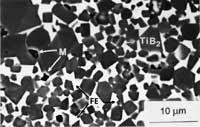
Debido al impulso dado en el campo de los cerámicos, muchas de las herramientas cerámicas existentes en el mercado actual se diseñan especialmente para algunas aplicaciones de corte. Dejando casi atrás las cerámicas monolíticas, investigan los sofisticados diseños de los composites cerámico-cerámicos. Es decir, controlando la morfología, tamaño, orientación, distribución y otras variables de las partículas, se pueden obtener microestructuras ‘favoritas’ de cada una de ellas. Por tanto, la tendencia actual es continuar con el diseño de materiales cerámicos en función de las propiedades mecánicas requeridas por las necesidades industriales.
En cuanto a los requisitos, TiB 2 -(Fe, Ni) investiga a su nueva familia (Figura 11). Con este cermet se pretende sustituir tanto el cobalto como el carburo wolframio. La producción de cobalto está en manos de muy pocos estados, porque es un elemento estratégico. Asimismo, el polvo de cobalto, debido a su origen cancerígeno, es muy peligroso. Por otra parte, dado que el compuesto TiB 2 es más resistente que el WC, las herramientas TiB 2 (Fe, Ni) que ya han probado, han mostrado un mejor comportamiento que las cermet “clásicas” en procesos de corte de alta velocidad.
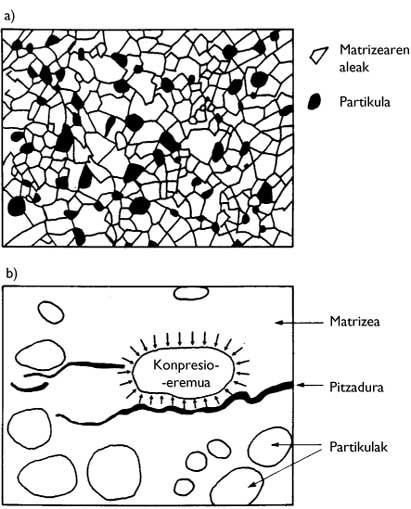
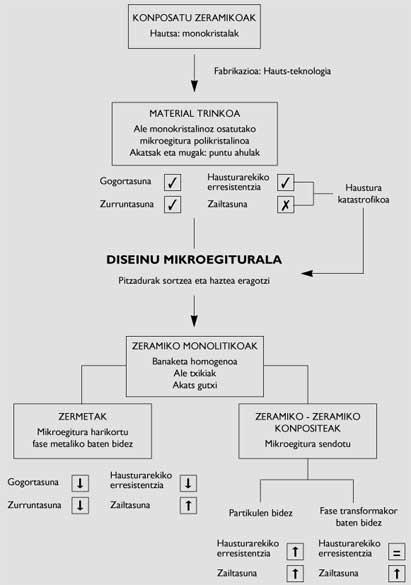
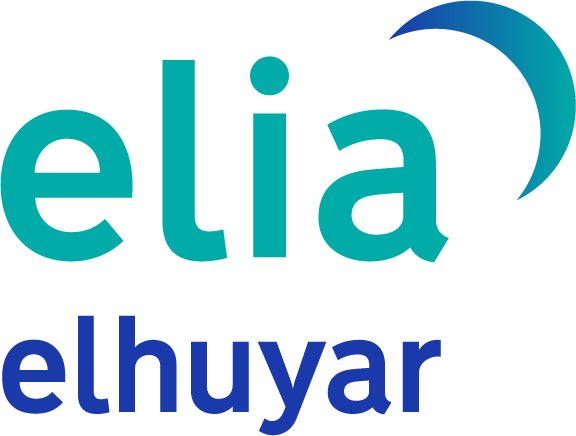
Gai honi buruzko eduki gehiago
Elhuyarrek garatutako teknologia