Electromagnetic fields in automotive
2007/10/01 Kortabitarte Egiguren, Irati - Elhuyar Zientzia Iturria: Elhuyar aldizkaria
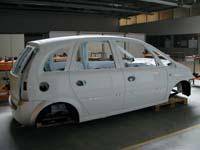
In the Autonomous Community of the Basque Country there are more than 800 companies related to the metal forming industry. It is a sector that grows every day. Currently, this sector also focuses on sustainable development, lightweight components and structures, reduced fuel consumption and emissions into the atmosphere of gases. In this sense, the automotive sector is working on the development of materials and processes that reduce the weight of cars, always maintaining their safety and maximizing comfort. This is because the lighter the cars are, the less they will consume fuels and thus emit less CO 2 into the atmosphere. It has been estimated that a 10% reduction in car mass represents a 7% reduction in fuel consumption.
The Automotive Department of the Labein-Tecnalia Research Center works on this. New materials are being developed to reduce the weight of cars. In particular, new processing processes for these materials are being studied.
Among other things, they have found that the mass of cars would be lightened by 15 to 25% using advanced high-strength steels --Ultra High Strength Steels (UHSS)- and optimizing manufacturing processes.
The problem is that UHSS steels are very resistant and difficult to deform. Like steel, aluminum and magnesium have other drawbacks with conventional forming techniques. For example, if magnesium is not heated to about 200ºC, acceptable deformations cannot be obtained.
To address all these problems, we propose, above all, the electromagnetic deformation technique of metals, for the possibilities it adds to conventional deformation techniques.
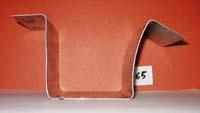
At high speeds
The electromagnetic field force is used in the metal electromagnetic deformation technique to shape the part. The piece should be conductive. It is a type of forming that occurs at high speeds. The material is formed at very high speed and, in general, it is possible to lengthen more than normal metals. For example, if aluminum is lengthened by 20%, an increase of 40% can normally be achieved by applying certain electromagnetic fields.
The basic components of this process are the condenser bank, electromagnetic coil and sheet metal.
The energy extracted from the general electrical grid is captured by a parallel system of capacitors, directing the discharged energy to the coil through a conductive circuit. The latter generates an electromagnetic field. The coils are generally copper and may have eleven geometries built with conductive materials, depending on the type of deformation. That is, depending on the shape you want to achieve, the shape of the coil is different.
Capacitors are charged with energy captured from the grid and release accumulated energy in microseconds. For this purpose, quick action switches are integrated into the system, the mercury vapour ignitrois being the most known or used.
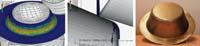
In short, when the coil is placed near a metal conductor and receives energy from the condenser bank, an electromagnetic field is created between the metal part and the coil. This electromagnetic field generates an electric current in the metal part that generates an electromagnetic field in the opposite direction. The interaction between both zones generates a force or impulse. And a whole boost. The piece is deformed at full speed from 50 to 200 m/s.
In the hydraulic press, one of the usual metal deformation techniques, the part normally reaches a deformation speed of 1-5 m/s. From there we get the bills! The initial thrust projects the part at high speed and the inertia it adopts makes the material deform more than conventional methods.
Working at incredible speeds they use a high-speed camera to collect what happens in this process. If not, human vision is not able to see what happens at those speeds.
This process allows the deformation of parts for eleven uses. Applications can be classified according to the format of the material. In fact, the applications of the sheets and tubes are very different.
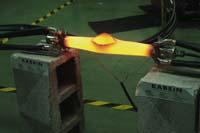
The only industrial application that has been made known in automotive is the link of metal tubes. The axles and associated elements are the ideal parts to carry out this application. This technology offers a great advantage for the development of material connections that prevent welding problems. The application of Txap remains an application in research.
As for the disadvantages, researchers have the biggest problem with the coil generating electromagnetic fields. And it is that all this force that is given to the piece is received by the coil itself. The blow caused by this violent force causes the coil to break and the sparks cause the coil to explode. Labein-Tecnalia researchers try to produce coils capable of overcoming this problem. With the electromagnetic field, many studies and simulations are carried out to predict coil response and experimentally develop new applications.
On the other hand, it has been proven that the process works best to form metals such as aluminum or copper that are good conductors of electricity. However, it can also be adapted to smaller drivers such as steel. Higher material electric transport capacity, better. Aluminum is better conductor of electricity than steel, so it can be deformed with less energy. As for steel deformation, much energy is required, so the risk of coil breakage is higher.
Although the Labein-Tecnalia research centre is developing automotive research, this technology offers outstanding applicability in other fields such as aeronautics, aerospace engineering and metal packaging manufacturing.
Other techniques
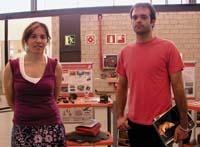
In addition to electromagnetic deformation, the Labein-Tecnalia Automotive Department works with two other main lines of research. On the one hand, they use heat for metal deformation (tube and sheet) and, on the other, the rotary forging (Rotary Forging).
For example, UHSS steels heat them up to about 1000°C and then put them in the press. At these temperatures, the material is much softer and deforms much more. However, for this purpose a furnace --heating, ready-- is needed, to subsequently manipulate the part at these temperatures another device is needed.
On the other hand, with the rotating forging, spectacular deformations are obtained. Different types of parts can be obtained from a normal metal sheet. In short, the metal part is taken and conformed, just as the lathe is used to make cylindrical objects in ceramics. In the case of metals, the part is pushed in some way with two tools to achieve the required length or deformation in each case. In some cases the piece rotates, in others the tools... It can be done both cold and hot.
This technique achieves an excellent surface finish of the part. This is because there is a great friction between the part and the tool. This technology also allows material lengthening considerably. However, its main disadvantage is time. It is a technique that takes a lot to take with patience. All this is reflected in the production process of the parts. In fact, if 10 parts per minute are produced in the hydraulic press, it is possible that with the rotating forging one piece per minute is obtained.
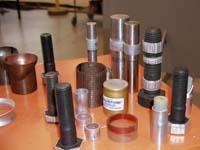
These time counts exceed the aforementioned electromagnetic deformation technique. Companies in this sector are constantly looking for process optimization, which means improving the quality of the final product, increasing productivity and reducing quantities of broken products. Therefore, one of the future alternatives could be electromagnetic deformation.
In the former Soviet Union the first studies of electromagnetic deformation of metals were released in the 1950s. It can be said that research has now been resumed, since there are important reasons for this, such as the environmental and safety objectives of automotive passengers.
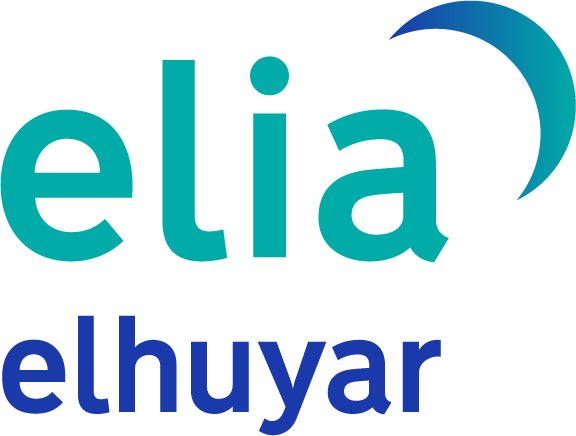
Gai honi buruzko eduki gehiago
Elhuyarrek garatutako teknologia