Acier: ni liquide, ni solide
2014/01/01 Kortabarria Olabarria, Beñardo - Elhuyar Zientzia Iturria: Elhuyar aldizkaria
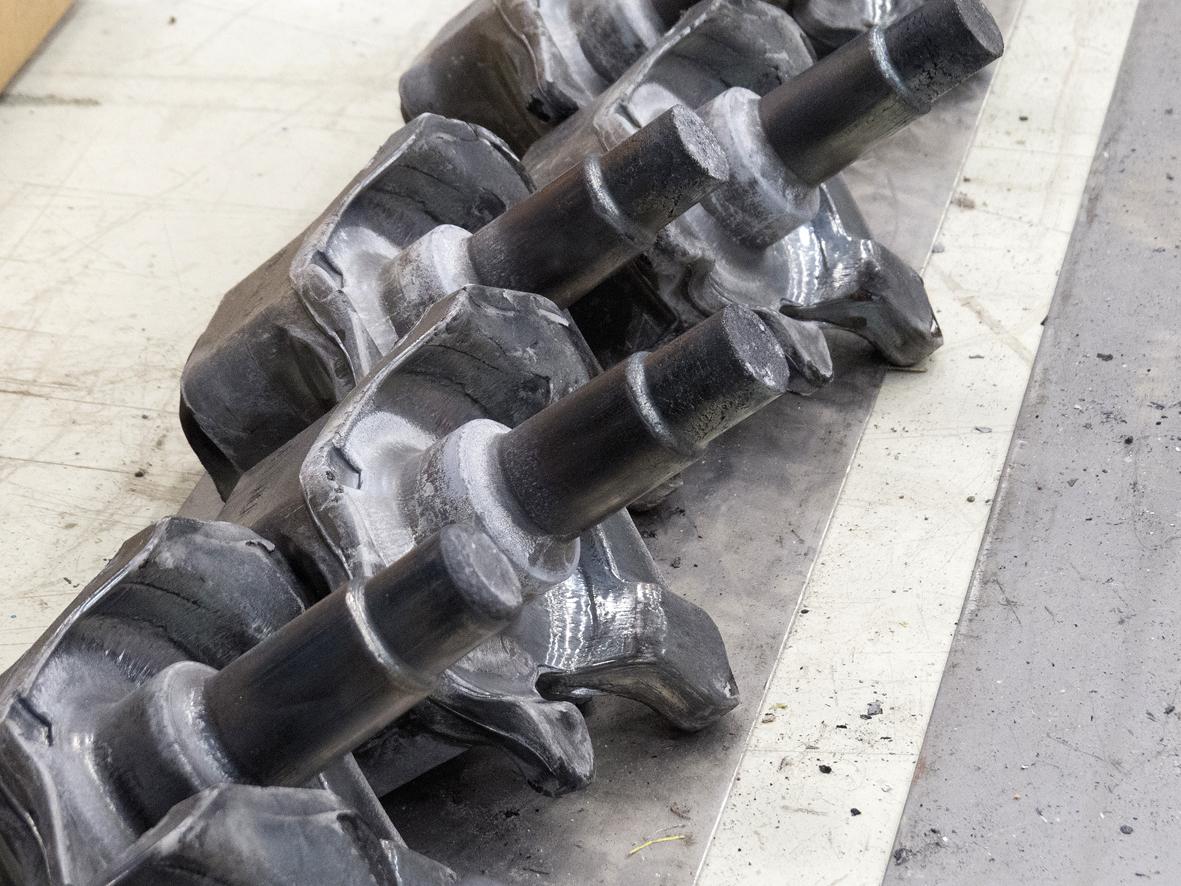
Mondragon Unibertsitatea, CIE Automotive et CIC Margune collaborent pour transférer la technologie du tixoformage à l'industrie de l'acier. En fait, les séances de laboratoire effectuées à ce jour ont montré que la tixoconformation peut être une réelle opportunité de travailler l'acier. "Au niveau industriel, il n'est pas encore utilisé - les mots sont de Jokin Lozares, chercheurs travaillant à Mondragon Unibertsitatea sur la tixoconformation. Dans le cas de l'aluminium, il y avait quelque chose, mais aujourd'hui, il ne devient pas trop. Le magnésium, pour sa part, est un processus industriel appelé tixomolding. Dans le monde de l'acier, personne ne fabrique des pièces par tixoconformation, ce qui en fait un processus innovant ».
-— Voir “Travailler avec de l’acier souple”, reportage de Teknopolis
De l'aluminium au fer
Jokin a mentionné l'aluminium. Il y a quelques années, à Mondragon Unibertsitatea, un projet a été réalisé pour travailler l'aluminium par la tixoconformation. C'est parce que la mise en semi-liquide semi-solide facilite la coupe et le moulage. Cet état semi-solide rend le matériau spécial, tout comme le dentifrice, qui se trouve en forme solide dans le pot, mais qui doit être "liquéfié" pour son extraction et recompacté ou augmenter la viscosité lorsqu'il est à l'extérieur pour maintenir sa forme, c'est-à-dire que les efforts de coupe diminuent la viscosité en augmentant la fluidité et, lorsque ces efforts disparaissent, la viscosité revient aux valeurs antérieures. Il s'agit d'un comportement tyxotrope qui est obtenu à une température donnée.
L'aluminium est l'un des métaux les plus utilisés dans l'industrie – derrière le fer – pour sa légèreté et sa résistance malgré son poids. Cependant, la forge traditionnelle et l'injection sont les formes les plus courantes de fabrication de pièces en aluminium, une en solide et une en liquide. En revanche, son état semi-solide permet d'obtenir des pièces beaucoup plus complexes que la forge, obtenant à son tour une porosité beaucoup plus faible et de meilleures propriétés mécaniques que lorsqu'il est totalement liquide.
Il faut d'abord chauffer l'aluminium. Chauffer jusqu'à 700ºC et laisser refroidir. Le secret est de battre l'aluminium à 620ºC quand il commence à se solidifier. Il est placé dans un champ magnétique et comme il est agité, l'aluminium va acquérir une structure spéciale, en changeant la taille et la forme du grain ou du grain. Au lieu de la structure dendritique ramifiée et allongée qui caractérise l'aluminium, on obtient une structure granulaire plus arrondie.
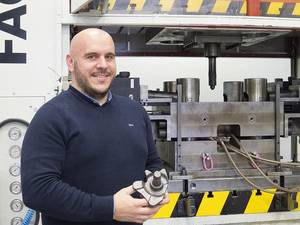
Chez Mondragon Unibertsitatea, ils sont convaincus que cette méthode permet d'obtenir des formes plus complexes et de meilleure qualité que la forge traditionnelle, en misant sur elle. Le défi est maintenant l'acier, selon Jokin Lozares, et ils sont testés avec une pièce réelle portant les voitures: "C'est une pièce qui est placé sur un modèle de voiture, un pivot situé sur la roue sur laquelle va, entre autres, le frein à disque. C'est une pièce critique de géométrie complexe ».
Cette pièce est actuellement fabriquée chez CIE Legazpia. Mikel Intxausti est responsable de la production de l'usine de Legazpi. "Le processus commence par une barre laminée. En le coupant nous obtenons un morceau ou un morceau d'acier. Ces morceaux sont chargés dans l'installation et chauffés à 1.250 degrés dans un four à induction. Puis, dans une presse mécanique d'environ 2.500 tonnes, le premier coup est donné et le talon est tiré. Nous donnons un deuxième coup à la sentinelle, d'où sort une forme semblable à celle de la fin. Avec un troisième coup, la pièce est finie et les bavures sont retirées à côté d'une autre presse mécanique jusqu'à ce que la pièce finale soit atteinte ».
De 3 à 1 coup
La technique de Mondragon Unibertsitatea est plus courte que celle de Lantegi. « Nous le faisons en un seul coup, dit Jokin Lozares-, c'est-à-dire le processus qui nécessite aujourd'hui trois étapes, nous le faisons en un seul. Nous chauffons le billard de près de trois kilos au four. Une fois réchauffé, le billard est placé dans le moule et façonné avec une presse en un seul coup ».
Selon la chercheuse de Mondragon Unibertsitatea, en plus de faciliter le processus, cette technique a permis d'économiser du matériel. Comparé à la pièce réalisée à Forja, le procédé de tixoconformation permet d'économiser 20-25 % sur le poids de la pièce, notamment en raison de l'absence de bavure.
Selon Jokin Lozares, la température est la clé pour bien former l'acier: "Dans notre cas, nous mettons du liquide entre 15 et 20% du billard, restant à l'état solide. Lorsque la force est appliquée, la viscosité du matériau diminue, elle devient plus douce. Et c'est ce qui permet de faire la pièce en une seule étape ».
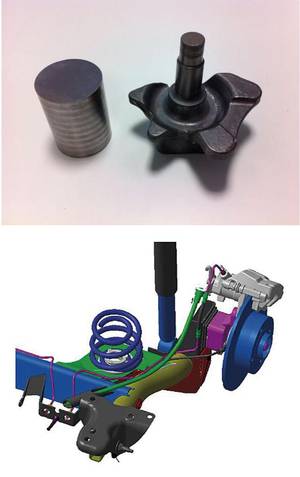
Ils placent l'acier à environ 1.400 ºC, 200 ºC de plus que dans la forge conventionnelle. Dans la forge chaude tout est solide, ne passe jamais à l'état liquide. En raison de la nécessité d'un chauffage homogène dans la tixoconformation, ils ont eu du mal à maintenir l'acier à une température homogène, sans le fondre, car il a été difficile pour eux. "Mais nous l'avons dépassé, dit Lozares-. La température est le facteur critique ».
Bien qu'ils aient déjà dépassé les fluctuations de température, tout au long du processus ont eu d'autres difficultés. Selon Lozares, la durée des matrices a été l'une d'elles. "En fait, dans la tixoconformation il y a une grande différence de température entre la maçonnerie et le levier, un à 300 degrés et l'autre à 1.400 degrés. Pendant la force de la presse, un fort choc thermique se produit et la fatigue thermique conséquente provoque des fissures».
La réduction de la durée de la découpe n'a pas été un problème d'aucune sorte et pour le combattre, des sprays à cire ont été utilisés. De cette façon, les problèmes thermiques ont été résolus, mais les restes de cire peuvent également être collés à la découpe.
Les comportements tixotropes ne sont pas nouveaux. XX. Ils sont connus depuis les années 70 du XXe siècle. Les céramistes, par exemple, connaissent très bien le comportement thixotrope. Dans les aciers a commencé à être étudié à partir des années 80. Mondragon Unibertsitatea veut aller plus loin: "Nous travaillons maintenant avec l'acier pour voir comment gérer ces températures élevées et nous envisageons également de passer à d'autres matériaux avec une température de fusion plus élevée, comme le titane."
Le défi du laboratoire à l'atelier
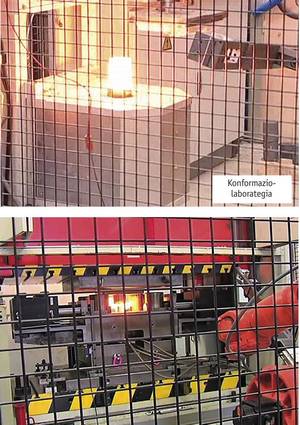
Dans le laboratoire, on regarde loin, mais selon Mikel Intxausti, il faut encore travailler la tixoconformation avant d'entrer dans l'atelier. « Il n'est pas encore pleinement impliqué dans le processus, dit Intxaustik. Si à Tixoforja il y a quelques difficultés à se forger totalement industriellement, il faut souligner que la durée des matrices est un gros problème et que la seconde est d'obtenir des caractéristiques mécaniques adéquates des pièces. Dans le laboratoire, nous avançons sur le chemin, mais nous ne pouvons pas encore intégrer le processus productif ». Il reste donc encore un chemin à parcourir.
Jokin Lozares parle aussi ainsi. "La tixoconformation nous permet de construire des murs en acier plus fins, la possibilité de faire plus de nerfs, des surfaces plus précises, c'est-à-dire la capacité de faire des pièces complexes. Contrairement à la forge, nous réaliserons des pièces plus complexes, mais pas aussi complexes que celles obtenues par fonderie. Moins de matière est également utilisée, le même billard initial est de 20-25% inférieur et ne se rebondit pas dans le processus. En ce qui concerne les caractéristiques mécaniques, les pièces présentent de meilleures propriétés mécaniques qu'en fonte, mais pires que les forges. Tel est le défi ».
Le projet est en attente d'améliorer les caractéristiques des pièces et d'ajuster le processus de production à l'industrie. Le président du CIC Margune, Iñigo Loizaga, voit cependant de bons yeux le projet: « La tixoconformation n'est pas nouvelle, mais elle n'a pas suffisamment avancé. Quand nous avons commencé à montrer notre intérêt pour ce sujet, à l'Université d'Aachen, une référence en Europe, ils nous ont dit que nous trouverions de grands inconvénients. Et nous les avons eu, mais pas tellement. Dans un délai raisonnable, nous obtenons des résultats optimistes et des pièces complexes. La société elle-même a vu que la tixoforja peut passer de laboratoire à la fabrication. Non seulement cela, mais nous avons réalisé que nous pouvons aller au-delà de l'automobile et de l'acier, par exemple, à l'aéronautique, avec des matériaux essentiellement de titan".
De plus, du point de vue du CIC, Iñigo Loizaga affirme que l'expérience est excellente. « Étant donné que la tixoconformation est un saut technologique relativement important, l'implication des chercheurs en recherche fondamentale est indispensable, mais avec une vision très compétitive et totalement traditionnelle de l'industrie forge », a-t-il souligné.
Les deux mondes, les besoins de recherche et d'industrie, la collaboration entre entreprise et université, reconnaissent qu'il n'a pas été facile, car les formes de travail sont très différentes. Cependant, ils ont réussi à former une équipe qui depuis des années ensemble, agile et dynamique, ce qui les amène à voir que les choses sortent. « Nous voyons qu'il a un avenir, si nous surmontons les difficultés qui restent, si nous brisons les barrières, nous aurons un avantage qui nous aidera à être plus compétitifs », a affirmé Loizaga.
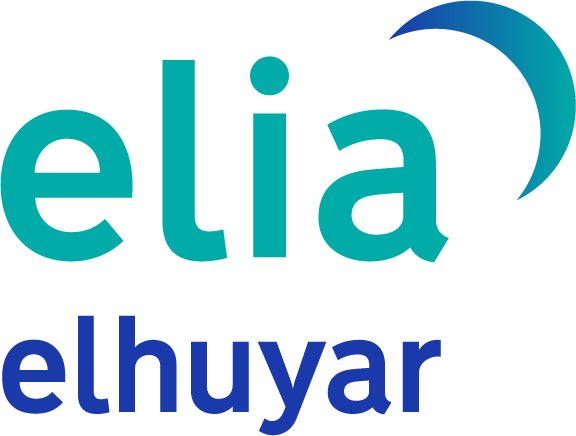
Gai honi buruzko eduki gehiago
Elhuyarrek garatutako teknologia