Flexible systems: CAD/CAM component
1987/10/01 Aizpurua Sarasola, Joxerra Iturria: Elhuyar aldizkaria
Introduction
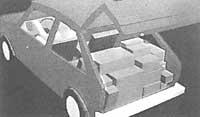
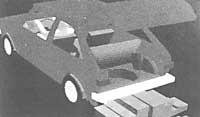
As a reference, the CAD is equipped with computer assisted design and drawing functions.
On the other hand, the CAM analyzes the processes and prepares the data of machine, machining, assembly, inspection with the help of the computer.
With the increased cost of machinery with advanced technology, the real economic solution would require three shifts of work. But improving quality of life is increasingly against the third shift.
Therefore, if you want to cover the costs of facilities and machinery, you need to operate as independently as possible from the workforce.
One of the most fixed solutions is flexible production automation, the use of flexible systems.
Under the FMS there are machines, systems and equipment with high and low complexity microprocessors that meet the following requirements to work processes:
- Flexibility: is the ability of a machine or system to automatically run different types of products.
Reprogrammability: the person responsible for the system, which is the ease of adapting this system to a new product.
In what technological areas are flexible systems applied?
Thanks to the microprocessor, most machines have automated their working cycles. Thus, grinding machines, bending machines, punching machines, pipe bending machines, shears, saws, filling presses, etc. (not forgetting machining and turning centers).
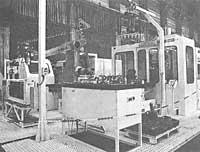
Within this broad field, we limit our explanation to machining chip starter parts. We will analyze, among others, five areas:
- CD directed machinery.
- Automatic chip removal
Automatic
tool change
Automatic parts transfer
CD Directed Machinery
Flexible manufacturing has encouraged manufacturers to review the design of structures and calculations. Therefore, the following characteristics must be taken into account:
- Stiffness of structures, minimizing deformations caused by static and dynamic effect.
- Precise machining and geometric control of the fixing planes and the treads, so that parallels and joints are optimised.
Today most machining and turning centers are built on modular chassis, widely dimensioned and ribbed in chassis. Calculations are done by computer and thermal changes are taken into account to avoid unexpected deformations.
Displacements are carried out by roller skates minimizing driver clearance. Each drive shaft is equipped with a ball screw. The screw is added without torsion and without slack to an engine without reducer. The position is controlled by sensors.
Audit in process
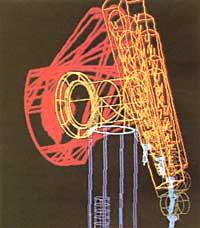
It seems that the trend of automated inspection is to eliminate final control. Parts are controlled during the manufacturing process. The functions listed below are based on multiple direction sensors/palpators. The latter are formed by a body and a wedge.
a) Automatic measurement of parts in process The
tool is replaced by an electronic measuring probe and the part is retained in several points. The
emitted signals are sent to the CD and it will order the necessary program changes.b) Automatic tool
adjustment Another probe controls the tool before and after working. Away from chip and cooling liquid and subject to machine chassis.c) Tool life control If a tool
works automatically and flexibly, it may be able to overcome its theoretical life. To avoid this problem, after working for a certain time, the tool changes.d) Automatic part
alignment In the machining of several parts, the position of the part must be maintained in relation to the working plane. Simply touch the part with a sensor in two points so that the CD can calculate the angular error and make the necessary corrections.e) Compensation of thermal
differences Often errors in machining are due to thermal variations. These phenomena are not easy to measure. However, approximate data can be obtained through sensors and palpators.f) Adapter control
In this field the control of the cutting power of the main motor is followed. Thus, even if the tool suffers wear, modifying the feed can maintain the cutting conditions without modifying the maximum load of the engine.
Automatic tool change
A manipulator or automatism changes the tool as directed by the CD. The change is done once the tool life is finished or when it can be finished within the machining of a part.
Automatic parts change. Industrial robot
The palos carousel is used in machining centres for parts change.
A robot manipulator is sufficient in turning centres. Not eight or ten axes, but four or more.
Automatic chip removal
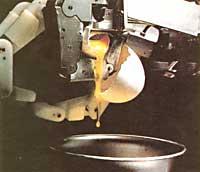
One of the most important factors to consider is the removal of chips in an unsupervised system.
There is no solution to remove chips from the stand, but the following factors will help us:
- Use plenty of cooling fluid Change the viscosity of the cooling fluid Change the
- Combine the mechanical brush with the oil shower.
position and quantity of the vents Mix the air jet with the oil showers Use the time needed to overcome this problem,
as it can then be expensive.
Flexible cell
There are many cell constructions, but although most are automatic, they are not flexible. When the flexible word is added to an automatic cell, the batches of parts passing through it are minimal and the batch can be unitary. In order to respond to this form of production, CD machines must be complemented with the following areas and technological features:
- Automatic identification of parts at the entrance of the cell by means of deregulated systems (vision, touch,...).
- Minicomputer with full cell control
Automatic transfer of parts between machines.
The machines, already without pallet carousel, are located next to an industrial robot. This robot must have the following particularities and control characteristics
- axles for 6 levels of
freedom - polar, cartesian or articulated structure
- load capacity 40/60
kg - interchangeable hands
Automatic inspection
Flexible workshops
These workshops have several flexible cells with several CD machines.
This type of workshop will take into account the following factors:
- Automated internal transport: robot/truck is used for this purpose. It is used for the transport of parts and tools.
- Complete foot control: there may be one or more mini computers. One is oriented to factory manufacturing and the other to production and warehouse management.
Automatic deposits: computer maintenance and automatic deposit, update inventory.
Last warp
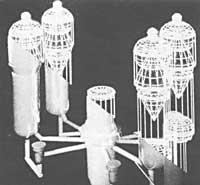
Flexible systems fully affect the field of machine tools. The importance of this sector in the Basque Country is well known. Although the crisis has hit our companies since the mid-19th century, it seems that some companies are beginning to resurface. Reduction of labor, technological innovation, etc. have been necessary. In short, productivity has improved and it is very rare to see machinery without numerical control. Most have integrated this system.
But in 1992 another black wolf threatens our economy, that is, the member states of the European Economic Union will constitute a free market. Therefore, tariffs protecting certain products will disappear. Among other things, Spain will appear in this situation and, of course, Euskal Herria as well. Therefore, competitiveness will increase at the peninsular level by the influence of foreign companies and if you want to survive you will have to improve productivity.
This improvement will come from flexible systems. Yes, each company or product will need its own systems. Moreover, the design and location costs of a flexible system are excessive for small and medium-sized enterprises. It is true that the Research Centres of the Basque Country have directed their research to this line, but in other countries the same is happening. Therefore, the future can be dark if the researchers and politicians of our country do not agree.
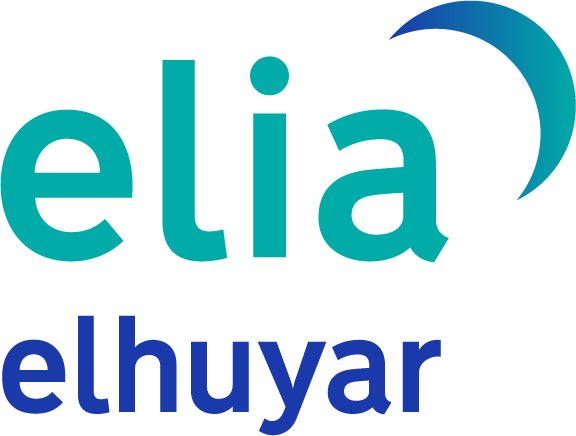
Gai honi buruzko eduki gehiago
Elhuyarrek garatutako teknologia