Motores de plástico en automóviles
1993/09/01 Alargunsoro, F. Iturria: Elhuyar aldizkaria
Algún día estos motores de plástico, aparentemente tan launas y coloridas como el juguete, podrán ser desmontados inmediatamente. Estos motores tendrán una forma de cuatro o cinco piezas en moldes. La reparación del motor será también muy sencilla, ya que cada tarea (absorción, cocción, refrigeración, etc.) tendrá su color. Cambiamos toda la pieza y ya está.
En la actualidad, la compañía Ford ha desarrollado, junto a sus seis proveedores, un motor de automóvil fabricado en plástico casi por completo. La cámara de cocción, con una temperatura aproximada de 1000 ºC, está compuesta únicamente por piezas móviles.
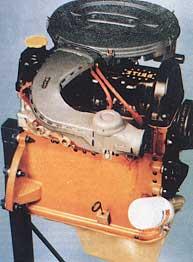
En su centro de investigación en Dunton en Gran Bretaña, el motor de 999 cm3 ha tenido 200 horas de funcionamiento en el banco de ensayos solicitando toda la potencia en 40 horas. Este motor de plástico, diseñado para ser aplicado transversalmente en el automóvil “Ford Fiesta”, emite un tercio menos de ruido que el motor convencional de la misma potencia.
Antes de Ford, la empresa Polymotor de Nueva Jersey había demostrado en 1988 las ventajas que los automovilistas pueden obtener con los motores de plástico. Desde el punto de vista de fabricación bastan cuatro minutos para sacar el bloque del motor del molde y comenzar a montar sin mecanizado de forma inmediata. El montaje puede ser realizado por un operario a media jornada. Además, para reducir los costes de fabricación no es necesario recurrir a series grandes. Y es que, a falta de máquinas de mecanizado, toda la maquinaria necesaria es sólo unas prensas y unos moldes. Por eso, la producción de 5.000 motores es suficiente para moverse a precios de mercado.
En cuanto a las prestaciones del motor, con una cilindrada de 2,3 litros, dieciséis válvulas y dos ejes de levas, tiene una potencia de 175 caballos a una velocidad de giro de 5.800 rpm. El motor sólo pesa 79 kilos, es decir, la mitad de la de fundición de la misma potencia.
El bloque motor y la culata se fabrican en moldes de inyección con resina fenólica (bakelita) reforzada con fibra de vidrio. El cárter se realiza con resina de vinilo poliéster con fibras de vidrio y el piñón de la cadena de distribución con poli(amida-imida).
Se probaron ochenta motores similares a los mencionados en 1988 en bancos de ensayo y carreteras. La firma Ford adquirió tres motores de este tipo y la empresa Polymotor tenía previsto construir una planta de fabricación de 25.000 motores al año. Sin embargo, las intenciones se han anulado y la razón es que los automovilistas no tienen capacidad financiera para sustituir sus equipos de producción de un día a otro. Tienen unas cadenas de fabricación muy costosas, que hay que amortizar con motores durante muchos años.
Es por tanto una cuestión de paciencia. Técnicamente se puede fabricar un motor de plástico debido al gran desarrollo de la química de polímeros. Actualmente existen resinas que soportan temperaturas superiores a 150 ºC, pero el precio puede ser un obstáculo. De hecho, la resina fenólica pasa de 1.000 a 2.000 ptas. (50-100 libras) por kilo, y el kilo de hierro fundido cuesta 60 ptas. (3 libras). Además, hasta que los automovilistas comienzan a fabricar motores de plástico en grandes series no parece que vayan a bajar los precios.
Sin embargo, los automovilistas no han abandonado el camino de los polímeros. Al igual que la casa Ford, los demás experimentan en sus laboratorios.
Bajo el capó del automóvil cada vez entran más piezas de plástico y en el motor. En la actualidad el automóvil lleva una media de más de diez kilos de plástico, excluido el caucho. En el motor, sin embargo, hasta ahora sólo se han utilizado metales. No obstante, filtros de aire, tapas de culata, rampas de inyección de combustible, tubos de entrada del cilindro, etc. están fabricados en plástico porque no tienen problemas de corrosión.
El plástico está penetrando cada vez más en el motor, sobre todo en la parte superior, y no es casualidad. Este aspecto es la parte que no sale de las cadenas automáticas de producción. El bloque motor y el culatín, en cambio, salen de esas cadenas que se amortizan en 15 o 20 años. En cambio, para trabajar el plástico no hacen falta instalaciones tan costosas. El plástico se trabaja en moldes y no tiene mecanizado complejo, ya que en el moldeo se pueden obtener formas muy traviesas. En las tuberías de entrada de aire al cilindro, por ejemplo, a diferencia de las de aluminio, se da una forma ideal a las poliaminscripciones reforzadas con fibra de vidrio, mejorando el rendimiento del motor en un 2%.
Debido a que el plástico es fácil de moldear, en lugar de varias piezas metálicas compuestas (unidas por racores, tornillos, etc.), la de plástico es una pieza única, reduciendo los costes de mecanizado y montaje. En los motores de la casa Peugeot, por ejemplo, en los mecanismos de carburación y explosión el número de piezas ha llegado a la mitad. El mecanismo de encendido del combustible en el interior del cilindro es de óxido de fenileno, tereftalato de polibutileno y totalmente electrónico. Resisten diferencias de potencial de hasta 100.000 voltios y cambios de temperatura de hasta 200ºC.
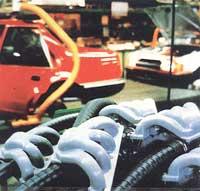
Además, al tener menos piezas, los motores de plástico son más bellos. La estética también afecta a los compradores, por lo que muchos automovilistas están suministrando la parte superior de sus motores con una hermosa tapa de plástico (para ocultar cables, tuberías, etc.). Además de la estética, puede ser importante el color de las piezas de plástico. Por un lado se puede conseguir que sea agradable para el comprador, pero por otro lado se pueden utilizar los colores para diferenciar diferentes circuitos. Por ejemplo, el circuito de refrigeración del motor puede ser de un color, el circuito de absorción de combustible de otro, etc.
Sin embargo, el plástico por el momento tiene algunos aspectos que difícilmente puede abarcar: cilindros, pistones, bielas, cigüeñes y ejes de levas, sobre todo. En estas piezas, las presiones y temperaturas son muy altas (desde 200 hasta 950 ºC) y por el momento se puede decir que están bajo la dependencia de metales. Sin embargo, Opel ha conseguido fabricar piezas móviles (engranajes) en las cajas de cambios de su modelo “Astra” con poliamida de fibra de vidrio. Resultados satisfactorios en ensayos a diferentes temperaturas.
General Electric Plastics también ha conseguido un piñón de poliimida Ultem a 180ºC. Material caro (2.000 pts. o 100 libras por kilo), se reproducirá en breve, al no tener que desmoldar ni mecanizar y el tiempo de fabricación disminuye hasta la décima parte. Además, la poliimida es cinco veces más ligera que el acero. Si antes vemos las cajas de cambio completas de los automóviles también de plástico, no es de extrañar.
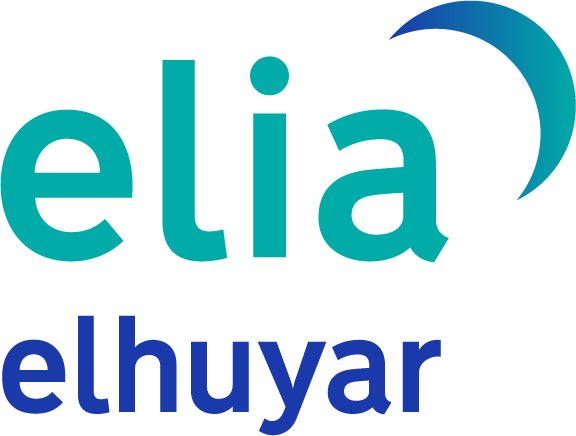
Gai honi buruzko eduki gehiago
Elhuyarrek garatutako teknologia