Plastic motors in cars
1993/09/01 Alargunsoro, F. Iturria: Elhuyar aldizkaria
Some day these plastic motors, apparently as launas and colorful as the toy, can be disassembled immediately. These engines will have a shape of four or five pieces in molds. Engine repair will also be very simple, as each task (absorption, cooking, cooling, etc.) will have its color. We changed the whole piece and it is already.
At present, the company Ford has developed, along with its six suppliers, a car engine made of plastic almost completely. The cooking chamber, with an approximate temperature of 1000 °C, is composed only of moving parts.
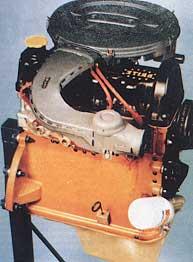
At its research center in Dunton in Britain, the 999 cm3 engine has had 200 hours of operation in the test bench requesting full power in 40 hours. This plastic motor, designed to be applied transversely in the “Ford Fiesta” car, emits a third less noise than the conventional motor of the same power.
Before Ford, the Polymotor company in New Jersey had demonstrated in 1988 the advantages that motorists can get with plastic engines. From the manufacturing point of view it takes four minutes to remove the engine block from the mold and start assembling without machining immediately. The assembly can be carried out by a half-day operator. In addition, to reduce manufacturing costs it is not necessary to use large series. And because, in the absence of machining machines, all the necessary machinery is only a few presses and some molds. Therefore, the production of 5,000 engines is enough to move at market prices.
In terms of engine performance, with a displacement of 2.3 liters, sixteen valves and two cam axes, it has a power of 175 horses at a turning speed of 5,800 rpm. The engine weighs only 79 kilos, that is, half of the casting of the same power.
The motor block and cylinder head are manufactured in injection molds with phenolic resin (bakelite) reinforced with fiberglass. The crankcase is made with polyester vinyl resin with glass fibres and the pinion of the distribution chain with poly(amida-imide).
Eighty engines similar to those mentioned in 1988 were tested on test benches and roads. The firm Ford acquired three engines of this type and the company Polymotor planned to build a manufacturing plant of 25,000 engines a year. However, the intentions have been cancelled and the reason is that motorists have no financial capacity to replace their production equipment overnight. They have very expensive manufacturing chains, which must be amortized with engines for many years.
It is therefore a matter of patience. Technically, a plastic motor can be manufactured due to the great development of polymer chemistry. Currently there are resins that support temperatures above 150 ° C, but the price can be an obstacle. In fact, phenolic resin goes from 1,000 to 2,000 ptas. (50-100 pounds) per kilo, and the kilo of cast iron costs 60 ptas. (3 pounds). In addition, until motorists start making plastic motors in large series, it doesn't seem to lower prices.
However, motorists have not abandoned the path of polymers. Like the Ford house, others experiment in their labs.
Under the hood of the car more and more plastic parts enter and into the engine. Today the car carries an average of more than ten kilos of plastic, excluding rubber. In the engine, however, so far only metals have been used. However, air filters, cylinder head caps, fuel injection ramps, cylinder inlet tubes, etc. are made of plastic because they have no corrosion problems.
Plastic is penetrating more and more into the engine, especially at the top, and it is no coincidence. This aspect is the part that does not leave the automatic production chains. The engine block and the cylinder head, instead, come out of those chains that are amortized in 15 or 20 years. In contrast, there is no need for such expensive installations to work plastic. The plastic is worked in molds and has no complex machining, since in the molding you can get very naughty shapes. In air inlet pipes to the cylinder, for example, unlike aluminium pipes, fiberglass reinforced polyaminscriptions are ideally shaped, improving engine performance by 2%.
Because plastic is easy to mold, instead of several composite metal parts (bonded by fittings, screws, etc. ), plastic is a unique part, reducing machining and assembly costs. In the engines of the Peugeot house, for example, in the carburizing and explosion mechanisms the number of parts has reached half. The ignition mechanism of the fuel inside the cylinder is phenylene oxide, polybutylene terephthalate and fully electronic. They withstand potential differences of up to 100,000 volts and temperature changes of up to 200ºC.
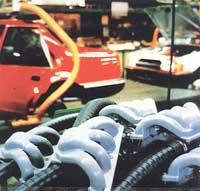
In addition, having fewer parts, plastic motors are more beautiful. Aesthetics also affect buyers, so many motorists are supplying the top of their engines with a beautiful plastic cap (to hide cables, pipes, etc. ). In addition to aesthetics, the color of plastic parts can be important. On the one hand it can be made pleasant for the buyer, but on the other hand colors can be used to differentiate different circuits. For example, engine cooling circuit can be one color, other fuel absorption circuit, etc.
However, plastic at the moment has some aspects that it can hardly cover: cylinders, pistons, cranks, crankshafts and camshaft, especially. In these parts, the pressures and temperatures are very high (from 200 to 950 ° C) and for the moment it can be said that they are under the dependence of metals. However, Opel has managed to manufacture moving parts (gears) in the gearboxes of its “Astra” model with fiberglass polyamide. Satisfactory results in tests at different temperatures.
General Electric Plastics has also achieved an Ultem polyimide sprocket at 180ºC. Expensive material (2,000 sts. 100 pounds per kilo), will be reproduced shortly, not having to unmold or mechanize and manufacturing time decreases to a tenth. In addition, polyimide is five times lighter than steel. If before we see the complete gearboxes of also plastic cars, it is not surprising.
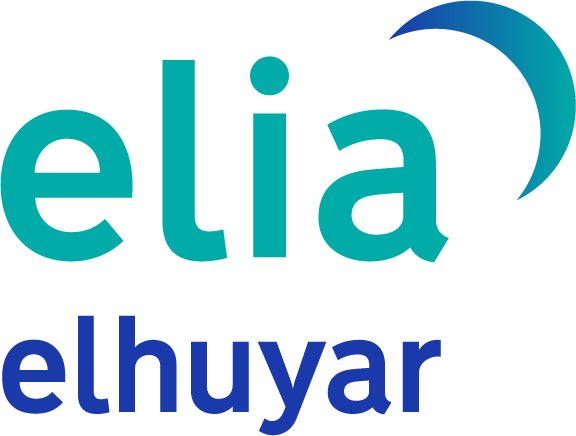
Gai honi buruzko eduki gehiago
Elhuyarrek garatutako teknologia