Stretch and stretch without breaking
2006/01/01 Urdanpilleta, Marta - Ingeniaritzan doktorea Iturria: Elhuyar aldizkaria
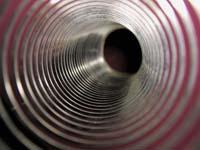
In Belgium there is an old joke about the Dutch who say they invented throwing a coin and so they managed to make the first cable from Amsterdam to Rotterdam. It is clear that the joke is an abuse because there is no metal that lengthens so much. However, aside from the greed of some, it is surprising how much metal material can be lengthened.
Most metal materials are lengthened between 50% and 100%, up to a maximum of double length, but not all. Some materials can be longer, between 200% and 1,000%. And an alloy of lead and tin can be extended by 7,000%, that is, seventy times more. Think we have a dessert spoon made with this alloy, because if we pull both sides at once, it would reach a length of 10 meters. No wonder this material is called superplastic.
The term superplastic indicates that these materials have an enormous stretch capacity. Although they are metals, they are 'very soft' within a temperature range and have a small enough tension to stretch. Normally, the material is more easily extended over half of the melting temperature. For example, nickel alloy has a melting temperature of about 1,300ºC, being the greatest superplasticity at about 950ºC.
The microscopic study of metals allows us to observe how this phenomenon occurs. Remember that in general the metallic materials are polycrystalline, that is, they are constituted by small crystallines. Within each crystalline, atoms are ordered periodically. The size of these crystals varies greatly depending on how this metal structure is formed: some metals have microscopic crystals, others have a millimeter or centimeter size, and some metal fragments are monocrystals, that is, the whole piece is a single crystal.
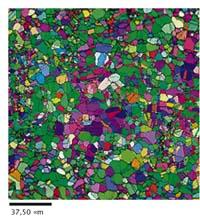
Well, in superplastics the size of these crystals is small, only a few microns (one micron is one thousandth of a millimetre), and the key to their stretch is in that small smallness of crystals: throughout the deformation the crystals do not increase. Remember that the metal must be heated to have a superplastic behavior, and according to the base physics, this heating extends the crystals and makes them larger. But this does not happen with superplastic metals, as the microscopic structure maintains a certain size of the glass.
The size of the crystals does not change when stretching the material, but changes the size and position of these crystals. In addition, they are normally biphasic materials, since superplastic metal is formed by two types of crystals of different chemical composition. Finally, there are other factors, perhaps more technical: for example, crystals must be able to turn at a large angle.
Industrial application
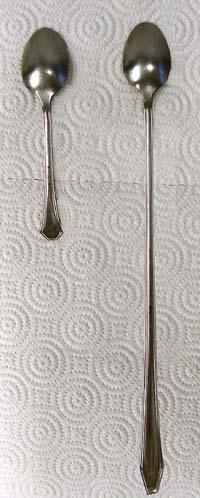
It was necessary in the industry, especially in the aviation industry. Titanium, aluminum and nickel alloys are mainly used in this field, combining superplastic forming and diffusion welding to produce complex morphology parts. The combination of both procedures allows the parts to be obtained in a single operation, reducing the cost of the material and reducing the production time compared to conventional techniques. The pieces obtained have an excellent surface finish and are very light. However, this technique also presents disadvantages such as that the starting material is expensive and that the thickness of the finished parts is not uniform.
There are many ways to work with superplastics, perhaps the most common technique is the so-called inflation shaping. This procedure has the form of glass blowing: in a watertight device, in a superplastic sheet located next to a mold argon gas is introduced at a not very high pressure and the foil adopts the shape of the mold. Extreme pressure machines are the usual ones in the industry, but to treat superplastic metals only 10 megapascals, that is, approximately one hundred times the atmospheric pressure.
The fact that not much pressure is needed does not mean that it is an instant process. To lengthen a piece of metal it heats up to the optimum temperature and takes many minutes, sometimes hours. Therefore, for the procedure to have an industrial interest, the deformation speed must be as high as possible to reduce the production time. At that speed also influences the size of the crystallines. In general, the smaller the crystalline ones, the higher the deformation speed. Therefore, the microscopic characteristics of superplastic metal are very important when treating this material. They are specific materials very difficult to perform and therefore expensive.
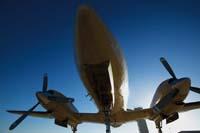
In the industry diffusion welding is often used along with superplastic forming. It began to expand in the 1960s and is currently used mainly in the aeronautical, nuclear and space technology industries. This process involves the diffusion of superplastic material between two or more equal materials, with moderate pressure and high temperature. As a result, after a small macroscopic deformation, the two pieces come together. To improve the quality of the joint a small pressure can be placed on the gas.
Basque Country
This technique allows different types of geometries to be obtained. Combining industrial conformation with deformation order device simulations, numerous applications are currently being developed, increasingly controlling all parameters. This technology also applies to companies in the Basque Country. For example, the aeronautical company ITP, located in the Technological Park of Zamudio, manufactures aircraft engines by superplastic forming, with an important R&D effort in this field.
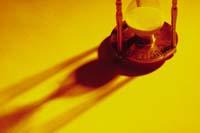
The future of superplasticity seems interesting and as deformation parameters are better controlled new applications are being created. High-speed superplasticity has also generated hope. It is possible that in the future it can be applied in undeveloped techniques. The truth is that superplasticity still has a long way to go.
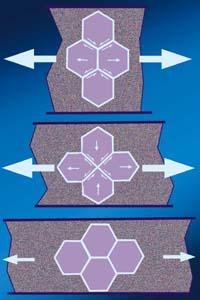
The author of this article, Marta Urdanpilleta, has made a thesis to investigate superplasticity through the collaboration of the technological centers ITP and CEIT.
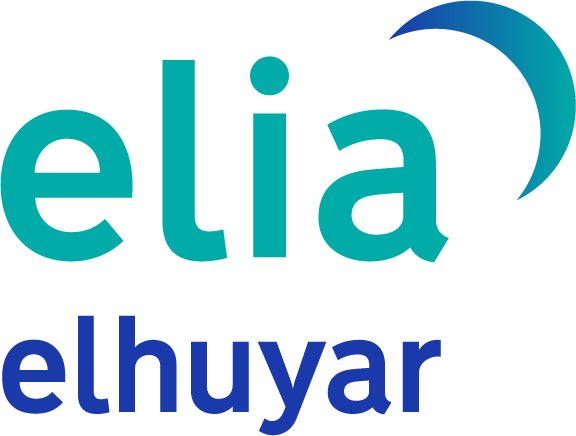