Powder metallurgy: old concepts but new products
1991/01/01 Rodriguez Ibabe, Jose Maria Iturria: Elhuyar aldizkaria
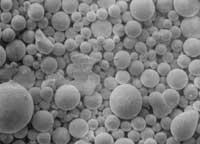
Powder metallurgy itself is not a new technology. The first examples that confirm the use of metallic powders are more than 4,000 years ago. That should not surprise us. In addition to powder metallurgy, in the rest of the procedures it is necessary to melt the metals, so in most cases high power ovens are needed. Therefore, the only working procedure formerly dominated by high melting point metals was the use of powders. In the following table XX. Some examples of the advance of this branch of metallurgy until the nineteenth century are mentioned.
Use of powder metallurgy in antiquity:
* Iron column in Delhi
(India) * High quality swords (Arabia)
* Precious metal parts (Peruvian
cechuars)
* Platinum ingots (Great Britain)
* Copper coins (Germany)
List
of
jobs
A.D. Year 400
A.D. Year
1000 year
1500 year 1826
year 1840
At the beginning of this century, when Goolidge developed the tungsten filament, modern powder metallurgy emerged. As an industrial process for the first time I. It was launched before the World War producing pomegranates of iron dust. Since then this procedure is being used with very different types of metals. Some of the best-known materials are tool steels, stainless steels, ferromagnetic alloys, refractory alloys, copper and its alloys, aluminum and titanium alloys, etc.
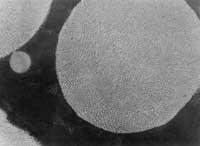
In the classic powder metallurgy, which we will then analyze the latest systems, compact parts are manufactured by pressing and sintering metal powders. In the case of the simplest procedure, iron powder is mixed with graphite and a lubricant such as zinc stearate. It is then compacted by hydraulic or mechanical press until one piece or tablet is obtained. The density of these pieces ranges from 6 to 7 g/cm 3, being enough to handle this level without manually undoing. Since this density is even smaller than the theoretical one, that is, the one corresponding to the totally compact piece, the process of the piece is incomplete. The product of this phase (i.e., that the powder is only compacted) is called “green”.
To achieve a higher density it is necessary to sintering the “green” product. To do this, the piece is inserted into the oven and with high temperatures, first the lubricant is burned and then the powders are joined reducing the number of holes, increasing the density. Sintering reduces the volume of the part. Therefore, the phenomenon of reduction must be taken into account in advance so that the final dimensions of the piece are within a tolerance interval. The properties of the obtained product are related to the density value.
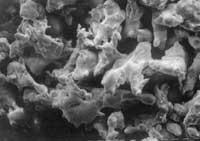
The less space the material has, the better its mechanical characteristics. The different variables that appear in the process must be properly controlled to get the best density. Some variables are the size, shape and quality of powders, temperature and sintering time, lubricant, etc.
In many applications the mechanical properties of a carbon steel are not sufficient. In these circumstances, steel will be alloyed with different elements for better properties. This also occurred in the applications of powder metallurgy, which fifteen years ago replaced iron powders with alloyed powders.
There are different procedures for obtaining alloyed powders. The following are two systems: water fracture and gas breakage.
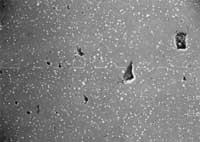
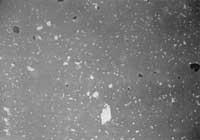
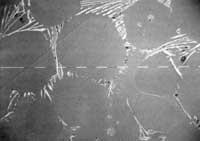
Photo 1: T = 1240C, many gaps still unclosed.
Photo 2: T = 1250C, optimum condition
Photo 3: T = 1280C, the temperature has been too high and the resulting microstructure, very different from the other two microstructures, has poor mechanical properties.
The alloy steel ingot obtained by a conventional procedure in the water fork is melted. When the alloy is poured down the bottom of the spoon, the liquid is quickly broken down into high-pressure water jet drops. The droplets thus formed solidify very quickly and, as for their properties, each powder can be considered as a “microingot”. Below are the powders that are ready to be marketed in case of a drying process. A lot of energy is consumed in the process, especially by giving water the necessary pressure.
The geometry of the powders is very irregular and its surface is formed by oxides. This last characteristic defines when it is possible to apply the water fracture procedure, since these oxides prevent the processes of association between powders that must be carried out in the compaction process. Some of the applications of these powders are stainless steels and tool steels. In the first case, powders are poorly oxidized and in the second, once a reduction procedure is applied, oxides can disappear. However, if the reduction procedure is inadequate, for example in the case of titanium alloys, this powder generation system will not be adequate.
In gas breakage, water is replaced by gas in liquid spraying. The powders thus formed are spherical and their surface appearance is very soft. Since gas is normally inert, for example argon, there is no oxidation process and high-quality powders can be obtained. This system is more expensive than water burning and is used for the preparation of special alloy powders.
The application of alloyed powders is related to parts that require good mechanical properties. As mentioned above, mechanical properties depend on density. Therefore, the final density of the product should be almost 100% and new industrial procedures have been developed to address this technological problem. Liquid sintering, hot forging of powders and hot isostatic compaction are discussed below.
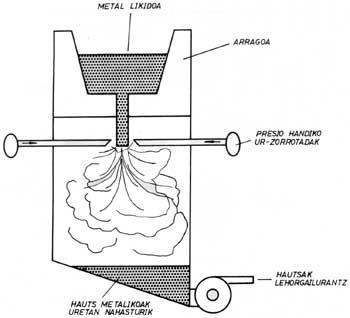
In liquid sintering, the “green” is heated in the metal to form a liquid phase. The amount of liquid phase is usually low, so once all the gaps in the green product are filled, the density of the part is 100%.
What has been said so far has always been achieved with high temperatures. It is easy to understand that the application of high pressure to the product at high temperatures can improve the results obtained. The isostatic forging and compaction of powders are based on this.
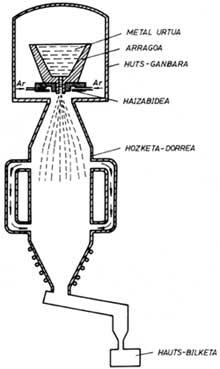
In the first case, the powders are compacted and sintered. Then, since the number of holes is still high (10-30%), hot forging is applied to the product, closing the gaps and bringing it closer to the theoretical value of density.
In the hot isostatic compaction (BTI), the part is heated and at the same time a large pressure is applied through a gas. The combination of temperature (1000 C for example) and pressure (250 MPa) allows closing the gaps.
BTI technology works with powders obtained by breaking gas. After compacting cold powders, they are inserted into a sweet steel container. The container is closed by removing all the gases from the inside using a vacuum pump. The container enters the press and if the chosen temperature and pressure values are adequate, in an hour the density of the product can reach 99%. The BTI procedure is very suitable for obtaining the final shapes and dimensions of the parts, without the need for further machining. Due to its high cost, it is especially used for the production of parts of titanium alloys, superalloys and other high cost materials.
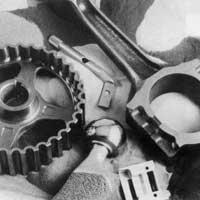
In short, we can say that powder metallurgy has advantages over traditional ingot metallurgy. Some of them are related to the quality of the product, facilitating the obtaining of homogeneous material. In other cases, the most important thing is the economic aspect. For example, if the dimensions and shapes of the parts obtained by powder metallurgy are very similar to those required by the products, the final machining processes are significantly reduced.
Finally, in solid state you can mix any type and quantity of powder. To obtain a ingot, first of all, it is necessary to melt all the metals that form the alloy, taking into account the solubility relationships that exist between the different elements. Consequently, the lack of this limit in powder metallurgy allows obtaining new alloys still unknown. The advantages described above show us the impact of this technology in the coming years.
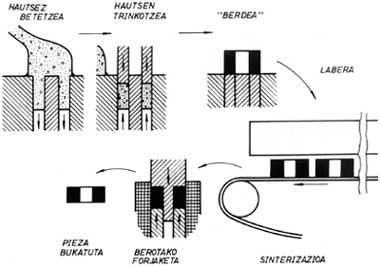
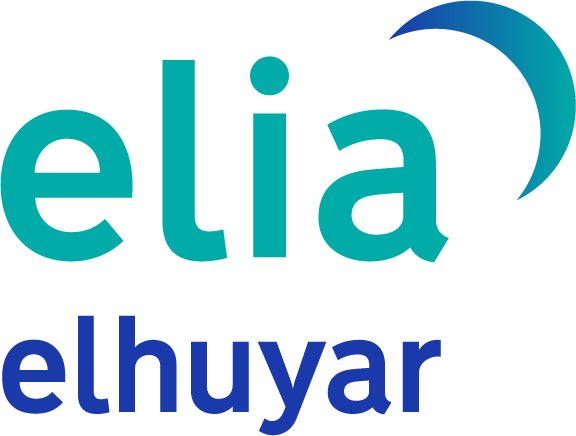
Gai honi buruzko eduki gehiago
Elhuyarrek garatutako teknologia