Machine to save time
2003/04/01 Atxotegi Alegria, Uhaina - Elhuyar Zientziaren Komunikazioa Iturria: Elhuyar aldizkaria
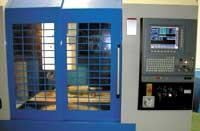
Before conventional machining was studied, that is, the students began to manipulate the machines manually. The hands, on the other hand, fell short of the resources of many instruments and the technology of numerical control has replaced human hands. In fact, with numerical control the operator performs a program and the machine follows the orders. In this type of technology, molds and dies are made of soft steel, which must be treated until hardening. The material is machined through different hardening phases and finally polished. However, as a result of these phases, costs skyrocket and waste a lot of time.
Subsequently, CAM technology (computer-assisted machining) was created to facilitate the work of the operator. Through this system, the student or worker draws by computer what he wants to machine and the computer offers directly a program. Within CAM technology there is more than one strategy, among other things, prepared for systems or new machines and materials designed for old tools and machines.
High Speed Machine
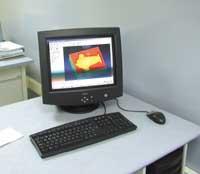
In order to track these three technologies, and always with the aim of saving time, high-speed machines have been created. The new system eliminates the treatment and polishing phases mentioned in numerical control. For example, moulds and dies are made directly from hard steel and do not require any treatment. Of course, this innovative machine must meet a number of requirements: it cannot change speed and, on the other hand, speed should not influence the accuracy of the product even though it occurs more quickly. The result must be equal to that obtained with other technologies.
This type of technology is being worked in different schools of the CAPV, including Vitoria-Gasteiz, Arrasate and the Antonian Polytechnic Institute of Zarautz. A team of teachers from this last center is learning to use this technology for later use by their students. Professor Iñaki Beobide, a member of this project, told us that three years have been imposed to learn high-speed machine technology.
Training and applications
In the last three years, Tekniker has developed this innovative technology in the field of machining. The teachers of the Antonian school approached him to train in this technology and since then they work together.
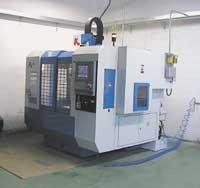
The courses have already been completed. From now on, they want to learn how to handle the machine and software they have recently acquired; they also intend to prepare didactic material for their students to internalize the new system in the most appropriate way possible. If it is not in the next course, they would like to do a test with the students. The idea is to teach high-speed machine technology in the production section of the students of the mechanics team.
For Iñaki Beobide, “this type of technology is mainly used in mold and die processing companies”. It is also used in stamps and ironworks. On the other hand, the process is more expensive, but Professor Beobide believes that “we have to analyze in which cases we have to use it and in which we do not”.
We cannot deny that this technology is innovative. As the name suggests, it helps to save time and reduce expenses for many companies.
Project VIRTOOLThe VIRTOOL project is boiling in the machining area. This project, part of the European IST (Information Society Technologies) initiative, aims to design and develop a new type of learning for machining processes. The Elgoibar IMH started this project in April 2001, in collaboration with a consortium, and will end in October 2003. This consortium consists of companies, research centres and educational centres from several European countries (France, Italy, Germany and Spain). For the design and development of this new type of learning have been used graphics in the three-dimensional system and virtual reality techniques. As a result, four applications have been obtained that offer the necessary tools for machining processes. Application Virtool Master (which defines a conventional machine tool or with CNC by geometry or kinematics), application Virtool Generic (machine customization application), application Virtool Case Generator (which offers the student different types of exercises and offers additional information to be able to perform such exercises) and, finally, application Virtool Machine (application that the student will use to obtain answers to the exercises). |
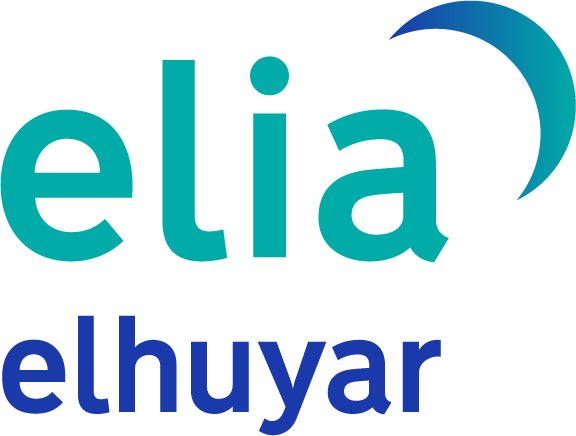
Gai honi buruzko eduki gehiago
Elhuyarrek garatutako teknologia