Fer, métal précieux
2003/07/01 Rementeria Argote, Nagore - Elhuyar Zientziaren Komunikazioa Iturria: Elhuyar aldizkaria
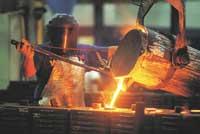
L'importance de la sidérurgie en Euskal Herria n'est mise en doute par personne. Aujourd'hui comme au cours des deux siècles précédents, il a certainement été l'un des piliers de l'économie basque. Indirectement, les hauts fourneaux ont influencé des domaines aussi divers que l'aménagement du territoire, les mouvements sociaux, etc. Plus d'un dira que le fer a contribué à cultiver le caractère des Basques.
Mais l'histoire de la sidérurgie n'a pas commencé avec les hauts fourneaux en Euskal Herria, vient bien avant. Auparavant, le fer était extrait dans les forges et avant dans les éoliennes.
Même si la technique des vents et des forges était fondamentalement la même, dans les forges on obtenait une plus grande production, puisqu'ils utilisaient la force de l'eau des rivières et des ruisseaux pour déplacer les soufflets, ce qui permettait d'obtenir une température plus élevée dans le four grâce au vent soufflé par les soufflets. Dans les vents, au contraire, les ferries affectaient les soufflets par la force de leurs bras, de sorte que la température du four dépendait de la force utilisée lors de l'actionnement des soufflets.
Obtention de fer pur
Bien que le fer soit très abondant dans la nature, il se trouve principalement sous forme d'oxyde (minéral de fer), donc dans les forges il fallait utiliser une réaction de réduction pour séparer le fer pur de l'oxygène et du reste des éléments. Dans cette réaction le réducteur était monoxyde de carbone et on obtenait en chauffant le charbon avec l'air des soufflets.
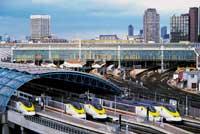
Chimie n'est pas un processus simple. La réaction du carbone avec les molécules d'oxygène d'air produit le dioxyde de carbone. Cette réaction est très exothermique, c'est-à-dire dégage beaucoup de chaleur. Le dioxyde de carbone réagit avec le carbone et le monoxyde de carbone est obtenu. Le monoxyde de carbone agit comme réducteur : il réduit les oxydes de fer et fournit du fer pur.
Le minerai de fer utilisé dans les forges était majoritairement hématite (Fe 2 O 3). Cependant, il est difficile de réduire complètement l'hématite, de sorte que les restes de magnétite (Fe 3 O 4) et de wüstita (FeO) apparaissent avec le reste des impuretés. Ces oxydes de fer apparaissent comme des produits de réactions intermédiaires pour l'obtention de métal pur.
Les ferries broyaient le minerai de fer avant de le mettre dans le four, augmentant ainsi la surface de réaction et facilitant l'arrivée du monoxyde de carbone à l'oxyde. Par la suite, le charbon de bois et le minéral concassé étaient introduits dans le four.
Pour que cette grande quantité de réactions se produise, il était indispensable d'obtenir des températures élevées dans le four. Le four chauffait jusqu'à 1.400 °C, près de la température de fusion du fer (1538 °C), à laquelle il était maintenu pendant cinq ou six heures. Pour cela, ils devaient ajouter du charbon sans cesse. C'est pourquoi, face à des problèmes d'approvisionnement en charbon, de nombreuses forges devaient cesser de travailler.
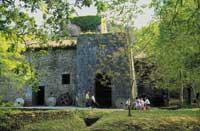
Au-dessus de 1100 ºC se fondent tous les composés autres que le fer. Pour en profiter, les fours avaient une coquine qui leur permettait de sortir les impuretés fondues hors du four. Ainsi expliqué, la séparation du fer et des impuretés semble simple, mais malheureusement la température du four n'était pas homogène et quelques impuretés (scories) restaient attachées au fer formant un autre. Pour libérer le fer pur de la scorie, ils frappaient le maillet avec le maillet.
Pourquoi le fer?
Le fer a révolutionné l'histoire du métal, mais ce n'était pas un jour. En outre, parce que l'extraction de fer nécessite une température très élevée, qui doit être maintenue pendant une longue période, la technologie requise dans le domaine du métal était très avancée.
Quand l'extraction de fer a été obtenue, le métal le plus dur connu jusqu'alors a été obtenu. Il n'est donc pas surprenant que les Romains exploitent plusieurs minéraux d'Euskal Herria, car l'un des piliers de l'empire romain était le fer. De même, les Romains ont connu les plus grands progrès dans l'industrie sidérurgique. Mais avant, a. C. VI. Pour le XXe siècle, les Basques extrayaient le fer, soi-disant enseignés par les Celtes.
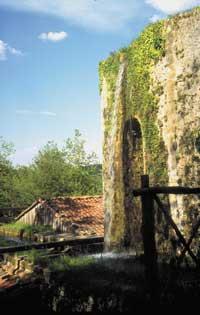
Les progrès de la sidérurgie arrivaient dans toute l'Europe. On a observé que les nouvelles techniques se propageaient rapidement, puisque les restes les plus anciens des progrès trouvés sur tout le continent correspondent presque à la même époque. Mais dans cette diffusion de la technologie il y a une exception frappante : XV. Le haut four fut inauguré au XVIIIe siècle. Avec cette nouvelle méthode d'extraction du fer on obtenait une meilleure performance, mais au Pays Basque on ne devait pas adopter cette technique. Bien que dans presque tout le continent on utilisait le grand four, en Euskal Herria on continua à utiliser le four d'en bas au XIXe siècle. Jusqu'au 20ème siècle.
On peut penser qu'ils avaient des motifs fondés pour maintenir la sidérurgie traditionnelle. L'une d'elles était la qualité du fer produit. En Euskal Herria ils avaient des matières premières très adéquates: Dans les mines de la zone de Somorcara on extrayait du minerai ou du minerai riche en fer, avec près de 60% de fer; en outre, le charbon végétal utilisé comme combustible était unique, principalement en bois de hêtre, et si c'était peu, les ports de transport de fer à l'extérieur étaient près des forges et les marins basques étaient expérimentés.
Cependant, lorsque le four est entré, les ferries ont cessé de travailler, la sidérurgie traditionnelle a été perdue et le temps a été d'éliminer les traces.
Ferrería de Agorregi
Afin de mieux connaître cette époque si importante de notre histoire, on a essayé de récupérer le travail des ferreries. Pour cela, de nombreuses ferries ont été cataloguées et restaurées. C'est le travail réalisé par Arkeolan dans la forge Agorregi d'Aia.
Le document le plus ancien de la forge d'Agorregi est le XV. Malgré son XXe siècle, le bâtiment qui aujourd'hui peut être restauré est du XVIIIe. Logiquement, le travail initial dans le processus de récupération a été la collecte de données, car la documentation et l'analyse des textes historiques sont la base de l'archéologie. Mais l'équipe d'Arkeolan a été un pas plus loin à Agorregi, où la forge a été lancée et, suivant l'ancienne méthode, ils ont réussi à extraire le fer. Ces travaux sont appelés archéologie expérimentale et le programme utilisé à Agorregi est devenu un modèle de travail dans l'archéologie expérimentale internationale.
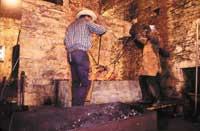
Le travail post-documentation a été l'obtention de matières premières. Mais comment obtenir du charbon de bois et du minerai de fer comme ceux d'autrefois ? La chance doit être en faveur, sans doute. Ils prirent le minerai d'un bateau coulé qui apparut à l'embouchure de la rivière Oria et qui, semble-t-il, provenait de Somorcara pour approvisionner Agorregi et d'autres ferreries voisines. Pour sa part, le charbon de bois a été obtenu à partir des essais réalisés à Zerain pour récupérer le travail des charbonniers.
En même temps, le bâtiment sera rénové et les canaux, antennes, etc. seront installés. ils ont dû être nettoyés. Quand tout était prêt, les séances d'extraction de fer ont commencé. Cependant, comme le processus et l'outillage n'étaient pas exactement décrits, ils ont dû effectuer plus d'un essai, introduisant des améliorations dans chaque test pour corriger les erreurs.
Ils ont réalisé que celle d'Agorregi était une forge inhabituelle. Le nom d'Agorregi vient d'Agorria, un toponyme qui indique qu'il s'agit d'un milieu sec. Et c'est probablement dû au débit variable des ruisseaux de la zone. Cependant, la mise en service des soufflets nécessite vingt litres d'eau par seconde et plus pour déplacer le marteau. Dans le but de faire face à ce flux d'eau variable, la forge a trois réservoirs et deux pentes, technologie et architecture très particulière. siècle.
Étude hydrogéologique pour la viabilité de la forge. Ils ont ainsi su qu'ils avaient assez de travail pour le mettre en marche entre mai et septembre, et qu'en hiver, s'il ne pleut pas souvent, la forge s'arrêtait. La forge d'Agorregi n'a donc pas eu beaucoup de succès dans la fabrication du fer, mais c'est un précieux patrimoine pour les archéologues et historiens contemporains.
Age du Fer
L'extraction du fer a représenté une révolution dans l'industrie du métal à l'âge du bronze, plus dure que le métal le plus fort connu jusque-là, le bronze. Compte tenu des avantages de l'utilisation du fer, la sidérurgie a été facilement étendue. Et l'âge du bronze a déménagé à l'âge du fer.
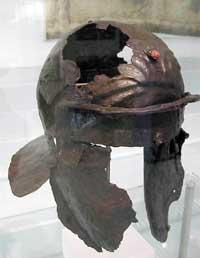
L'origine de l'âge du fer est située en Asie Mineure. Vers 1200 ans, environ pendant la guerre de Troie. Cependant, on ne sait toujours pas où et quand la première extraction de fer a eu lieu. Il semble que l'extraction du fer a été obtenue à différents endroits à la fois, comme en Europe, en Asie Mineure et en Chine.
Aussi en Afrique. C. Beaucoup de villages ont pu extraire du fer pour le cinquième siècle, en utilisant de petites ferreries.
La sidérurgie a acquis une grande force en Inde et a été l'un des plus grands producteurs de fer de l'Antiquité, la preuve en était Delin, a. C. Il y a une colonne de fer de 400 ans.
Depuis lors, le fer n'a pas perdu de son importance et est l'une des matières premières les plus utilisées aujourd'hui. Qui pourrait dire que l'âge du fer a pris fin?
Malédiction du fer
Selon la Légende de Sisiphe, les dieux Sisisif le condamnèrent à monter une grande pierre jusqu'au sommet et chaque fois qu'il y essaya, la pierre tombait encore et encore sur le versant.
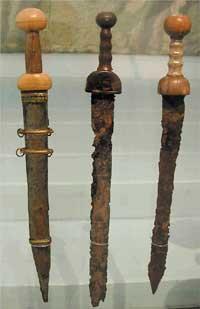
Quelque chose de semblable se produit avec le fer: même si à partir des oxydes de fer on obtient du fer pur, il a tendance à rouiller à nouveau. C'est parce que l'oxyde est plus stable que le fer pur.
Le fer est oxydé en contact avec l'air ou l'eau, car les atomes de fer ont tendance à rejoindre les atomes d'oxygène formant des oxydes de fer.
Dans le but de faire face à cette malédiction, à cette époque, ils ont connu divers alliages pour obtenir des métaux qui s'oxydaient plus facilement en mélangeant du fer avec d'autres substances.
Actuellement, les outils et objets en fer sont peints, enduits de graisse ou recouverts de plastique pour éviter un contact direct avec l'air ou l'eau. Une autre façon de protéger le fer est de le mettre en contact avec un métal qui s'oxyde plus facilement.
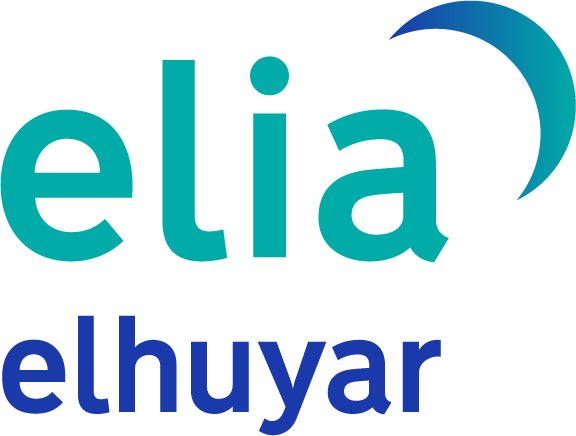
Gai honi buruzko eduki gehiago
Elhuyarrek garatutako teknologia