Iron, precious metal
2003/07/01 Rementeria Argote, Nagore - Elhuyar Zientziaren Komunikazioa Iturria: Elhuyar aldizkaria
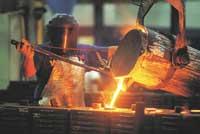
The importance of steel in Euskal Herria is not questioned by anyone. At present and in the previous two centuries, it has undoubtedly been one of the pillars of the Basque economy. Indirectly, the blast furnaces have influenced areas as diverse as the planning of the territory, social movements, etc. More than one will say that iron has contributed to cultivating the character of the Basques.
But the history of the steel mill did not begin with the blast furnaces in Euskal Herria, it comes much earlier. Before, iron was extracted in the ferns and before in the wind.
Although the technique of the winds and the ferns was basically the same, in the ferns a greater production was obtained, since they used the water force of the rivers and streams to move the bellows, which allowed to obtain a higher temperature in the oven thanks to the wind blown by the bellows. In the winds, on the contrary, the ferrones affected the bellows by the force of their arms, so the temperature of the furnace depended on the force used when driving the bellows.
Obtaining pure iron
Although iron is very abundant in nature, it is found mainly in the form of oxide (iron ore), so in the ferns it was necessary to use a reduction reaction to separate the pure iron from the oxygen and the rest of the elements. In this reaction the reducer was carbon monoxide and was obtained by heating the coal with the air of the bellows.
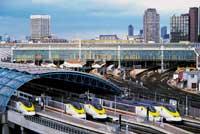
Chemistry is not a simple process. The carbon reaction with the oxygen molecules of the air produces carbon dioxide. This reaction is very exothermic, that is, it gives off much heat. Carbon dioxide reacts with carbon and carbon monoxide is obtained. Carbon monoxide acts as a reducer: it reduces iron oxides and provides pure iron.
The iron ore used in the ferns was mostly hematites (Fe 2 O 3). However, it is difficult to completely reduce hematites, so magnetite remains (Fe 3 O 4) and wüstita (FeO) appear along with the rest of impurities. These iron oxides appear as products of intermediate reactions for obtaining pure metal.
The ferrones crushed the iron ore before putting it in the oven, thus increasing the reaction surface and facilitating the arrival of carbon monoxide to oxide. Subsequently, the charcoal and the crushed mineral were introduced into the oven.
To produce this great quantity of reactions, it was essential to obtain high temperatures in the oven. The furnace was heated up to about 1,400 °C, near the temperature of fusion of iron (1,538 °C), which was maintained for five or six hours. For this purpose, they had to add coal without ceasing. Therefore, faced with problems in the supply of coal, many ferns had to stop working.
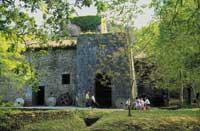
Above 1,100 °C all compounds other than iron are melted. To take advantage of it, the furnaces had a naughty that allowed them to remove the molten impurities out of the oven. Thus explained, the separation of iron and impurities seems simple, but unfortunately the temperature of the furnace was not homogeneous and some impurities (slag) were attached to the iron forming one more. To release the pure iron from the slag, they beat the deck with the deck.
Why the iron?
Iron revolutionized the history of metal, but it was not a day. In addition, because iron extraction requires a very high temperature, which should be maintained for a long time, the technology required in the metal field was very advanced.
When the iron extraction was achieved, the hardest metal known until then was obtained. Therefore, it is not surprising that the Romans exploited several minerals of Euskal Herria, since one of the pillars of the Roman empire was iron. Likewise, the Romans were the ones who experienced the greatest advances in the steel industry. But before, a. C. C. VI. By the twentieth century, the Basques extracted iron, supposedly taught by the Celts.
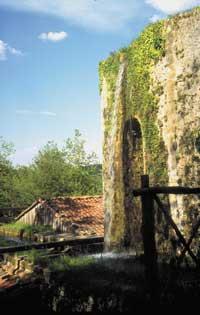
The advances in the steel industry came throughout Europe. It has been observed that the new techniques were spreading rapidly, since the oldest remains of the advances found throughout the continent correspond almost to the same time. But in that diffusion of technology there is a striking exception: XV. In the eighteenth century the high furnace was inaugurated. With this novel method of extraction of iron, a higher yield was obtained, but in the Basque Country this technique should not be adopted. Although the high furnace was used in almost the entire continent, in Euskal Herria the furnace was used from below in the nineteenth century. Until the twentieth century.
It can be thought that they had reasons founded to maintain traditional steel. One of them was the quality of the iron produced. In Euskal Herria they had very adequate raw materials: In the mines of the area of Somorrostro was extracted mineral or mineral rich of iron, with about 60% of iron; in addition, the vegetable coal used as fuel was unique, mainly of beech wood, and if not little, the ports of transport of iron to the outside were near the ferns and the Basque sailors were experienced.
However, when the high oven entered, the ferns stopped working, the traditional steel mill was lost and the time was eliminating traces.
Ferrería de Agorregi
With the aim of knowing better that era so important in our history, we have tried to recover the work of the ferns. For this purpose, numerous ferns have been cataloged and restored. This is the work done by Arkeolan in the Agorregi ironworks of Aia.
The oldest document of the Agorregi ironworks is the XV. Despite its twentieth century, the building that today can be seen restored is XVIII. Logically, the initial work in the recovery process was data collection, since the documentation and analysis of historical texts are the basis of archaeology. But Arkeolan's team was a step later in Agorregi, where the ironworks were launched and, following the old method, they managed to extract the iron. This type of work is called experimental archaeology and the program used in Agorregi became a model of work in international experimental archaeology.
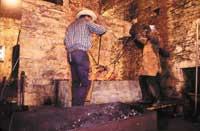
The work after the documentation was the obtaining of raw materials. But, how to get iron coal and mineral like those of yesteryear? Luck has to be in favor, no doubt. They took the mineral from a sunken ship that appeared at the mouth of the river Oria and that, apparently, came from Somorrostro to supply Agorregi and other nearby ferns. For its part, the charcoal was obtained from the tests that were carried out in Zerain to recover the work of the carboneros.
At the same time, the building will be reformed and channels, antennas, etc. They had to be cleaned. When everything was ready, the iron extraction sessions began. However, since the process and tooling were not accurately described, they had to perform more than one trial, introducing improvements in each test to correct errors.
They realized that that that of Agorregi was an unusual ironwork. The name of Agorregi comes from Agorria, a name that indicates that it is a dry medium. And probably it is due to the variable flow of the streams of the area. However, the start-up of the bellows requires twenty liters of water per second and more to move the hammer. With the aim of dealing with this variable water flow, the ironwork has three reservoirs and two very peculiar slopes, technology and architecture. century.
Hydrogeological study for the viability of ferrería. So they knew that they had enough work to start it between May and September, and that in winter, if it does not rain often, the forge stopped. Therefore, the Agorregi ironwork was not very successful in the manufacture of iron, but it is a valuable heritage for archaeologists and contemporary historians.
Age of Iron
The extraction of iron meant a revolution in the metal industry in the Bronze Age, harder than the strongest metal known until then, bronze. Given the advantages of using iron, steel was easily extended. And the Bronze Age was moved to the Iron Age.
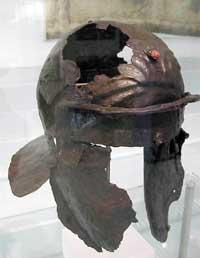
The origin of the Iron Age is located in Asia Minor. About 1200 years, approximately during the Trojan war. However, it is still not clear where and when the first iron extraction occurred. It seems that the extraction of iron was achieved in different places at a time, as in Europe, Asia Minor and China.
Also in Africa a. C. C. Many villages were able to extract iron for the fifth century, using small ferns.
The steel mill acquired great strength in India and was one of the largest iron producers of antiquity, proof of this was Delin, a. C. C. There is an iron column of 400 years.
Since then, iron has not lost prominence and is one of the most used raw materials today. Who could say that the Iron Age ended?
Curse of the Iron
According to the Legend of Sisyphus, the gods Sisisyphus condemned him to climb a great stone to the top and every time he tried in it the stone fell again and again to the hillside.
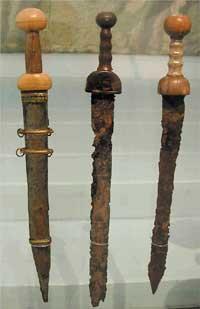
Something similar happens with iron: although from the iron oxides, pure iron is obtained, it tends to reoxidize. This is because the oxide is more stable than pure iron.
Iron is oxidized in contact with air or water, since iron atoms tend to bind to oxygen atoms by forming iron oxides.
With the aim of dealing with this curse, at that time they experienced various alloys to obtain metals that oxidized more easily by mixing iron with other substances.
Currently, the tools and iron objects are painted, greased or coated in plastic to avoid direct contact with air or water. Another way to protect iron is to put it in contact with a metal that is oxidized more easily.
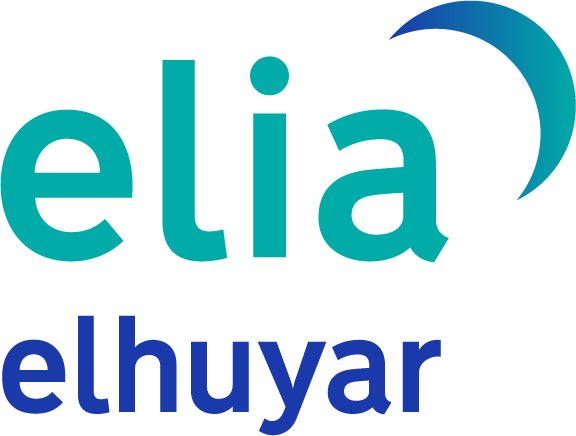
Gai honi buruzko eduki gehiago
Elhuyarrek garatutako teknologia