Robic III: climbing robot for hazardous environments
1998/03/01 Ugarte, Haritz Iturria: Elhuyar aldizkaria
The second week of November was held the seminar on Applied Robotics for Electrical Industry at the headquarters of the CEIT technology center in Donostia. There was presented the mobile robot created by the CEIT technology center within the SRT project, sponsored by the companies Robic III, Iberdrola and Endesa. This robot is able to ascend on vertical surfaces thanks to a system of suction cups and is equipped with sensors and cameras to find cracks. Its first task will be to inspect the pipes and waste deposits of nuclear power plants in search of cracks. This project was created to avoid the risk of radiation suffered by workers doing this type of work in nuclear power plants.
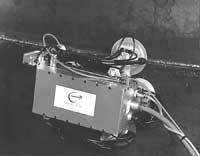
The robot, created by the Chilean members of CEIT Leoncio Briones and Paul Bustamante, has as main objective the inspection, operation and maintenance of nuclear plants. In addition, the design has sought to make the size, weight and operating cost of the robot as minimal as possible. Consequently, the Robic III climbing robot is fast, compact, cheap and robust, and can be built with easily locatable elements on the market. Along with a relatively simple mechanical system, more sophisticated control hardware and software are required, including camcorders, vacuum sensors, electrovalves and electronic components. Figure 1 shows the body of Robic III. In this body is the locomotor system on one side and the ultrasonic sensor and video cameras on the other.
Locomotion mechanism
In the central unit of the robot there are two cylinders without stems of 100 mm in length and 10 mm in diameter. The transverse conductors that slide through these cylinders carry two absorption cups on each side of the robot. The other two absorption cups are fixed and are located at the front and back of the robot.
The robot works thanks to the mobile and fixed absorption cups, described below:
- It acts on the fixed front and rear absorption cups of the robot to be stuck on the wall.
- Mobile absorption cups are carried forward.
- Mobile absorption cups are affected and fixed absorption cups are stopped.
- The moving absorption cups are delayed to the top of the cylinder, generating the advance movement of the robot.
The moving absorption cups have rotation movement with respect to the transverse guides. This can involve a rotational and transversal movement of the robot.
Vacuum system
In prototypes prior to climbing robots the biggest problem was the high weight of conventional vacuum generators and pneumatic cylinders. Therefore, for Robic III it was decided to create a more compact vacuum generation system and a new positioning subsystem to reduce weight and volume. It can be observed that the vacuum generator has a rotation axis that allows the movement of the robot on cylindrical and spherical surfaces.
Control system
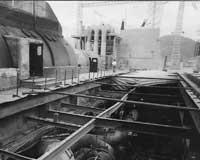
The control system consists of a control table based on the Intel 89535 processor. Although all valves are on-off type, each cylinder has a position sensor to precisely control the movement of the robot. Each absorption cup has a vacuum sensor whose measurements are used to determine whether each step of the control algorithm has gone well or not. If a step has not gone all right, a series of short strokes is repeated until the proper failure is achieved. This ensures the proper functioning of the robot during welds and irregularities. The robot is teleoperated via a personal computer with different cameras and sensors.
The first task of the climbing robot Robic III will be to inspect under radiation of 1.2 Gy/h a deposit containing the radioactive residue of the nuclear power plant of Santa María de Garoña. This will allow inspecting the environments in which the personnel cannot reach, both through sensors and cameras.
The SRT project was promoted by ENDESA and IBERDROLA in 1994 with the aim of creating robotic inspection and operation systems in Spanish nuclear power plants.
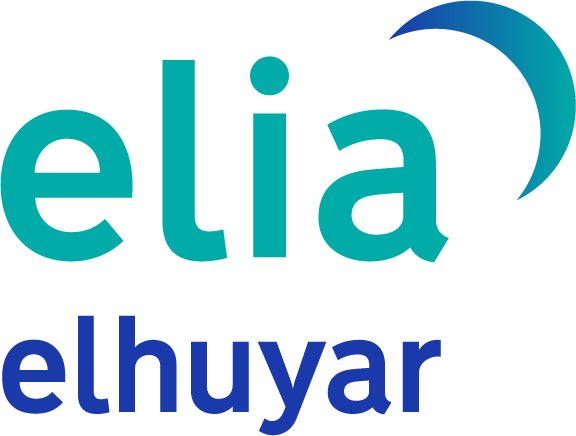
Gai honi buruzko eduki gehiago
Elhuyarrek garatutako teknologia