Process engineering
1992/02/01 Sarriegi Eskisabel, Andoni Iturria: Elhuyar aldizkaria
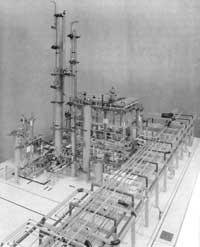
Any industrial activity is based on the transformation of matter and energy. The processes used from chemistry to metallurgy, the composites industry, oil, electrochemistry, medicine kit, textile, leather, paper, etc., to the agri-food industry are a major economic challenge. It is estimated that the process industries of developed countries contribute around 25% of the industrial added value. The problems posed by these industries are also numerous and of a diverse nature. On the other hand, the processes themselves have to respond to market demands and adapt to competition in the near future.
However, facilities designed from laboratory data present a technically and financially dangerous extrapolation period. From the laboratory to the factory thousands of scale factors are common and in some cases they can be tens. Among the thousand good laboratory ideas can be developed a hundred of them, of which perhaps only about twelve come to enter the commercial process.
The installation of this process, after the investigation of its proper functioning and the quality control of the manufactured ones, requires complex controls and numerical models of simulation. Finally, another absolute requirement is that processes are reliable, easy to maintain, safe and non-polluting, but at the same time practically insecure for man and the environment.
How has the traditional industry responded to these problems? In general and so far, except for exceptions, unwise. Each area has developed its own techniques and has focused on the productions it had to manufacture, always under the meaning of “trade”. Among the different areas, moreover, there seemed to be very few things in common. At least in advance there was not much to do with “chemicals”, “cement workers” or “yogurts”. This mentality no longer serves to adequately respond to the needs of today's industry. Precisely, the engineering sciences have been developed to offer the concepts and tools necessary for the study of “industrial systems”. At present, process engineering, dubbed “procedural”, is a methodology generally applicable to all procedures, regardless of the type of production and activity performed.
The procedure, therefore, proposes a transversal and interdisciplinary vision that facilitates not only the appearance of the initial concepts, but also the development of very tractor investigations. In this case, it is a generalization of “chemical engineering” methods. Chemical transformation is a complex process in which the tuning of production scales poses serious problems: chemical reactions, heat and matter exchanges, fluid and solid exchange, material behavior, etc. mix.
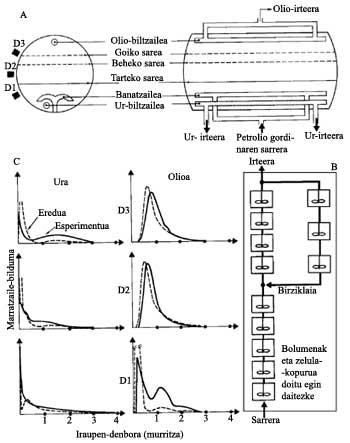
To solve all this it has been necessary to devise new solutions and not simple combinations of conventional chemistry, thermotechnics and mechanics. This new discipline is based on a set of knowledge and works of this type. Americans have named this mixture “paradigm” and here at least some will be mentioned.
First of all, the “unit operation” can be cited. This concept, already in 1915 A. D. It was proposed by the little American, distillation, filtration, drying, etc. to designate operations like these. Of course, an analysis of all operations is interesting, regardless of the nature of the substances involved. In this way the application of laws that define their effectiveness is achieved and, consequently, the appropriate industrial equipment is designed. For example, mechanical mixing operation can be studied in depth. This operation is performed in a tank using a rotating device. It is important to select and size the right type of mixer for each use, depending on the rheology that the mixture should contain, the fineness of gas bubbles or the dissolution that solid particles must maintain. They have to see the size of the tank, the image, the proportions, the mixing power, the rate of equitable dispersion of this power and other important parameters.
The second outstanding “paradigm” in process engineering is the “systemic approach”. The analytical vision of traditional sciences decomposed, fragmented, and concentrated matters into microscopic structures. The systemic approach tends to gain a global view of structures and behaviors. It deals with the response dynamics of very varied systems such as the catalyst grain, the distillation column or the production workshop, that is, the assemblies organized with respect to a target to be achieved. In other words, the forest is more than a tree. These visions, for example, have been widely analyzed by J. de Rosnay in his work Le macroscope.
The third "paradigm" or set of knowledge on which process engineering is based refers to the links between reactions and transformation processes, especially between solids/gases and two immiscible fluids. For example, in catalytic reactions transfer and reaction occur respectively. If the former is simple and the latter is difficult, the latter controls the speed of transformation, that is, the “chemical regime”. If it is the other way around it is diffusion.
But chemistry is not the only one who does. Living systems also have to do with reaction/shredding operations.
In 1970, for example, A.C. Nevo and R. Rikmenspoel, from the consumption of oxygen and the diffusion of the energy vector of the ATP protoplasma, took the length of the scourge of the sperm. Nature therefore conforms to the limit between the chemical regime and the diffusion regime. Therefore, the above is only an example of the heuristic value of a procedural concept in the natural sciences.
In process engineering methods two important characteristics stand out: their universality and their scalability character. Therefore, they can be applied to both industrial systems and natural phenomena if transformations of matter and energy occur during the process. But in process engineering another important topic is included, which is the basis of the existence of universal relationships between numbers without dimensions. This allows to treat a large number of seemingly very different problems.
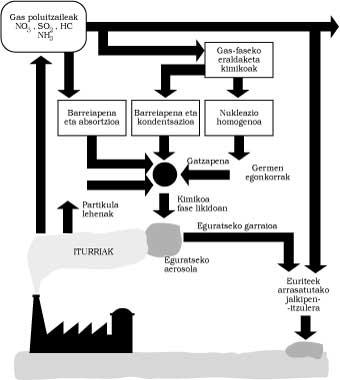
Despite being a well-known vision in mechanics and thermology, chemical engineering has enriched considerably by introducing many dimensionless numbers involved in transformation operations.
On the other hand, the last paradigm related to operations is to give priority to the global vision of problems, that is, to take into account simultaneously all the requirements of a process, including the techniques of analysis of the final product and the environment. An elegant laboratory synthesis process aimed at a new product with excellent properties could fail due to lack of market, high cost, equipment that does not withstand corrosion, necessary insecurity, etc. The problem considered chemical can be, for example, material or electrical resistance. Here you cannot walk with a multidisciplinary approach!
For example, since 1925 the chemicals pursued the manufacture of acetic acid (vinegar) by catalytic reaction with methanol, but the process did not work industrially due to corrosion of equipment. The solution is due to a special alloy, molybdenum and nickel called Hastelloy, which was applied to the industry from 1960.
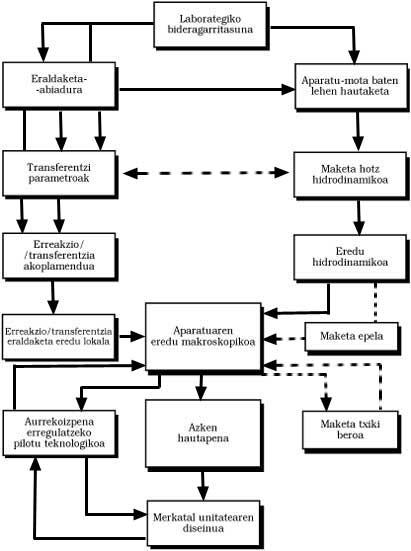
What are, therefore, the main industrial challenges arising from the procedure? Some are:
- The first is methodological. How to quickly and economically develop a new process, that is, how to move from laboratory to factory, how to design the right equipment? Is it possible that in the second decade of this century, when the first concepts of chemical engineering emerged, the classical scheme used was moved to other areas?
The serious problem of mathematical modeling versus experimentation. In other words, will factories designed entirely from laboratory data become current without conducting pilot or demonstration installations? For simple transformations (simple fluids, etc.) seems possible, but it looks far for the complex ones. In any case, designers will have to rely increasingly on process engineering. - The next point is quality control. In a world of competition, only industrialists remain capable of ensuring a strict level of product quality. Here raw materials are important but also the process itself. In continuous manufacturing chains, capturing the random nature of inputs through produced statistical samples and systematic process errors allows the use of the Statistical process control training method, which has been developing in the industry for years. But here it is also a question of rigorously understanding the mechanisms that lead the “real path” towards proper modelling. Quality
control, of course, should never forget energy expenditure and in this sense, since 1974, process engineering has contributed decisively to its reduction. In this area, the programmatic framework of the French Energy Control Agency (AFME) should be highlighted. - The third precision refers to the safety of processes and the protection of the environment, and in this field, the ideal that tries to reach any industrial process is that there are no errors or that it is zero defects, zero events, zero waste. The delicate sensitivity of the population to these problems has forced the public authorities to begin to perceive them and in recent years important research efforts have been made in some places, despite being still far from doing enough.
- The industrialization of biological transformations also explains the fourth type of challenge, which is fundamental for process engineering: the control of living materials.
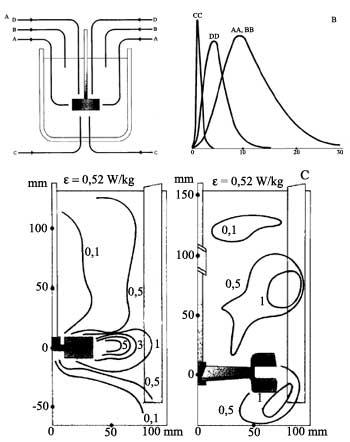
Genetic engineering makes available to us the programming of microfactories, that is, cells. However, to achieve an industrializable process, it is necessary to put favorable conditions to achieve the best production of the desired metabolites and this stage is at least as important as the previous one.
In this sense, another area in which the presence of process engineering is strongly demanded is that of biotransformations in the food industry. What has so far been an artisanal process, would be to industrialize especially, but preserving the organoleptic qualities of the products and obtaining a total hygiene (superclean factory).
The solution of these obstacles, of course, poses many problems to the investigation and, at least, three are mainly: the intervention of the “complex means”, the area of particular rheological behavior and the obtaining by commission of a “property”.
If we delve into all this, we would go into the physical call of disorder or the physical call of chaos, where we would enter the world of unknown behaviors that confusions have in different temperatures, pressures and conditions. Therefore, process engineering also offers new objectives to study the physics of chaos.
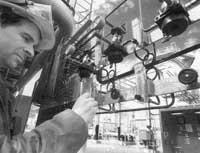
Once they reach these spaces, in the field of artificial intelligence it also appears close, at least in that of the approaches. The possibilities offered by neural networks and the attention of procedural researchers begin to attract. These machines, formed by small interconnected logical organs, are able to respond to a given input signal by a given output signal. They are also able to learn, to structure the interior and to know the information that it offers them. Last year, at the French Atomic Energy Station, A. L. The researcher at the Allanic Nancy School of Chemical Industries was able to design an auxiliary system for the management of radiated fuel reprocessing facilities.
It is also necessary to expect the implementation of process control systems using mathematical models to advance in parallel if they are developed simultaneously by aligned intelligent sensors and tend to the collection of real-time information in operation units.
Finally, it is worth mentioning the so-called self-adaptive method. They propose it in Nancy and turn the process into a “black box.” After some initial tests, a mathematical model based on real physical behaviors is built step by step and requires a number of tests lower than the blind statistical project.
Therefore, the systematics are in a position to contribute decisively to most of the great strategic challenges of the year 2000, both in terms of rational use of energy resources and raw materials, as well as in matters of food, health protection, safety of industrial processes and products, environmental protection or third world development. All these and other issues were widely discussed at the Karlsruhe World Congress.
Obviously, both in the field of basic principles and industrial acts, important research efforts are necessary. Highlights include the publication in the United States of the prestigious report “Amundson” (“Frontiers in chemical engineering”, 1988), the report of the twenty-six working groups of the European Federation of Chemical Engineering in Europe (1989) and the first French congress of process engineering of Nancy (1987) and the new orientation followed by all of them. It is a true cultural revolution. The honorable classification by Auguste Comte ceases to be the appropriate framework for industrial production system technology. In this field, the focus of the sciences of interdisciplinary engineering is on the need to accommodate and the procedural is only its publication.
The fertilization of these new sciences marks the end of the old distinction between so-called fundamental research (natural things) and applied research (industrial issues).
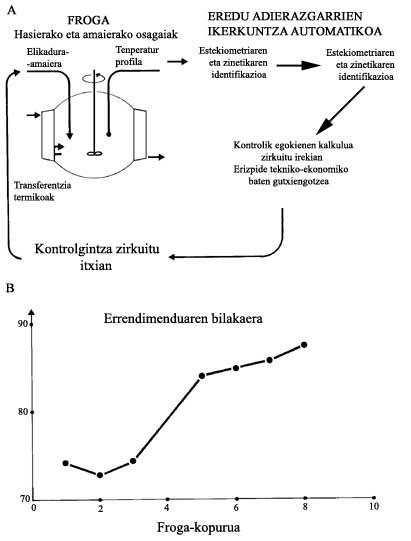
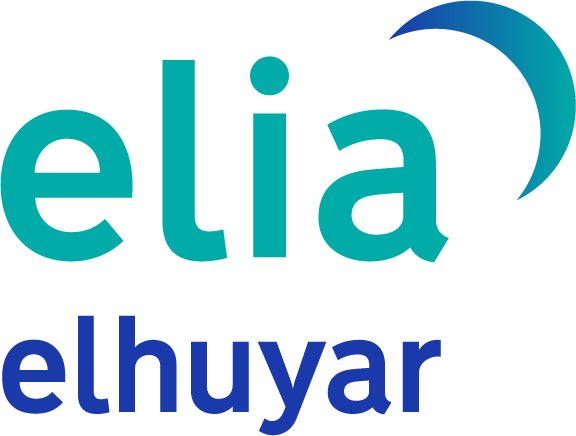
Gai honi buruzko eduki gehiago
Elhuyarrek garatutako teknologia