How to solve the risks of fire in public transport?
1996/05/01 Azpiazu, A. | Gondra, Koldo | Madariaga, L | Vergara, J. Iturria: Elhuyar aldizkaria
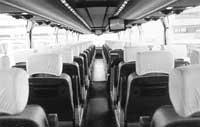
As mentioned above, plastic products have undergone significant development in recent years. Each year new resins appear, but the behavior of phenolic resins in front of fire, that is, the low toxicity and opacity of smoke, has contributed to stimulate interest and increase research (Forsdyke and Hemming, 1989; Gupta, 1986; Dayley, 1989; Ellis, 1988; McQuarrie and Lake, 1986; Savey, 1989). Fiberglass reinforced plastics include polyester, epoxy and phenol.
The bad fire behavior of polyester and epoxy resins, as well as safety regulations in transport, have been the most prevalent phenol resins lately. The recovery and research of these resins are making great efforts. Currently phenol resins are used in aviation and the naval sector (for the manufacture of interior parts), transport (for the realization of seats), machine tool (for the manufacture of friction and cutting discs) and carpentry (for the manufacture of plates and agglomerates). In this article we will limit ourselves to transport applications.
Aviation
The requirements to be met by the materials used in this field are: low specific weight, good mechanical properties, rigidity (in wings and spoilers) and good fatigue resistance to maintain the bending and vibration processes of the wing blades, spoilers and helicopters.
The advantages of composites over traditional materials, especially aluminium and special alloys, are their lower cost, lower specific weight, ease of complex shapes and dimensional stability.
From a historical point of view, composites began to be used during World War II. In 1943 the first glass reinforced polyester fuselages began to be used. In 1955, asbestos and aramid reinforced phenol composites were tested. In 1960, fiberglass reinforced epoxy composites were used on the “Windecker” plane. In 1972, taking into account the fire advantages of phenol resins, it was decided to use them in interior parts of the “Concorde” aircraft. In 1973 the first structural parts of the plane “Concorde” with epoxy resin reinforced with carbon were made.
On the other hand, the company Bakelite presented at the fair Verbundwerk’93 new materials that could have application in aviation, specifically hybrid composites epoxy/phenol. In these materials, epoxy materials act as additives and phenolic compounds improve their fire properties.
The company Ciba-Geigy manufactures the panels used inside the plane with different materials. According to their mechanical characteristics, the surface of these materials is phenolic resin and the center is made of rigid foams of aluminum or synthetic material, or of the same material and in the form of honeycomb.
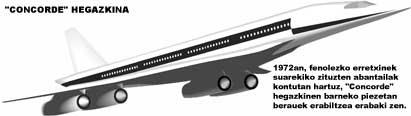
Spaces
The materials used in the spaces are carbon fibres, boron and/or aramid, thermoset resins (epoxy and phenol) and ceramic materials especially in parts subjected to high temperatures. The advantage of plastic composites over other materials is their low density.
The most relevant applications of composites in this sector are summarized in Table 1.
USE | PIECE | MATERIAL |
Space | Panels. | Epoxy/precluded |
Telecommunications satellites. | Central pipe. | Epoxy/carbon composite. |
Ballistics projectile. | Parts must undergo temperature changes. | Phenol resin reinforced with granite fiber. |
Shipbuilding
In the 1950s, glass reinforced polyester composites were used in the naval industry. Today, carbon and aramid reinforcements and epoxy resin are used in very special applications.
The characteristics required for the materials in this matter are grouped in the following lines: being resistant and resistant to the marine environment, easy maintenance and repair, resistant to impact, with good anti-magnetism and dielectric properties, resistant to stride, with the possibility of redirecting the reinforcement and, of course, cheaper than the competing materials.
Table 2 summarizes the applications of these materials in the naval industry and the materials used for these applications.
Railway
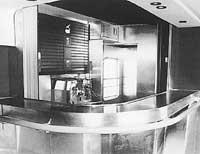
Although it has already been commented, it is good to remember that the use of polyester and phenol composites is important in the transport sector. The use of polyester improves the appearance of the surface, but we cannot forget its bad behavior against fire. For its improvement is mandatory the use of halogen compounds. Improves, but also increases the toxicity and opacity of smoke. Therefore, if you want to reduce the risk of users in case of fire, the use of phenol compounds is recommended.
For example, to address the technical problems generated by the trains of the Spanish State, glass reinforced ignition polyesters (instead of phenol resins) have been used, which has increased the risk of passengers in case of fire.
The main composites used in Spanish trains are:
- RENFE. E 444-5 cab front in the three series of long travel electric trains.
- Metro of Madrid. Various body elements in glass-reinforced polyester have been manufactured on the 2000 series electric trains. They are classified as M1 to fire.
- F.C. Barcelona Metropolitano. Some trains in the 2000 series incorporate ignifted polyester elements. They are classified as M1 to fire.
- RENFE. In the three series of electric trains U-446 and UT-447, the interior of the cabin and its seats have been made with glass-reinforced polyester. They are classified as M1 to fire.
- Metro of Madrid. On the 2000 series electric trains, the interior of the cabin and its seats are made of ignifted polyester. They have the M1 classification.
Phenol resin has been used more in Europe and the world, such as: In the Paris Metro, the body; in the Caracas Metro, the seats and the interior supply; in the San Francisco Metro, the interior supply; in the London Metro, the station supply; in the Metro Aramis of Matra, the entire trolley, the seats and trolley, the seats and the interior parts; in the Railway of England, the console of the dashboard; in the Metro of Rome
USE | MATERIAL |
Sports boat structures. | Polyester reinforced with |
Projectile fuselages used in underwater exploration. | Fiberglass reinforced |
Water and fuel collection | Polyester reinforced with |
Methods of execution
According to the method chosen, the transformation of composites requires three simultaneous or simultaneous steps: incorporation of reinforcements, molding of composite materials and hardening of the material and extraction of the mold part.
GAIKER has analyzed the different processing methods and performed the characterization of the obtained parts.
Manual molding
It was the first method used for the manufacture of plastic laminates. Today it is still the most used.
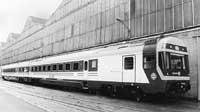
Having the most economical method for short series and large surface parts and not needing specialized personnel are its main advantages. On the contrary, slow production, the need for a lot of labor, the good appearance only of a part of the piece and the lower physical and chemical properties compared to other methods.
This method, in the case of phenol resin, is used for the manufacture of the train gurteria, using acids as a catalyst for the realization of the grid.
RTM
The RTM device works as a syringe. First suck the resin and catalyst mixture and then inject the mold with fibers.
Due to the low pressures and temperatures used in this processing, the molds can be heated or not heated, being the finish of the part attached to the appearance of the mold surface and the catalyst used.
Depending on the temperature of the mold, external or internal demolders can be used in the processing, while for modifying material properties and reducing process costs charged resin can be used.
The following are the companies and products that produce phenolic composites: WES Plastics, military elements; Flexadux Plastics Ltd., train bodies; Move-Vigo Ltd., large parts (3 m x 3 m x 22 mm) and Plasteck Thermoset Tectronic, aircraft components.
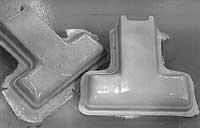
Analyzing the current trend, it is estimated that RTM technology will reach adequate levels of automation and technology in the coming years, which allows predicting its use in the manufacture of components for aviation. Plasteck Thermoset Tectronics is the company that is conducting the most important research in this field.
Cold pressing
This method is used to produce between 1,000 and 10,000 pieces per year. Due to low pressing pressure, composite molds can be used. The viscosity of the resin used is medium and to reduce the formulation price and increase the rigidity of the part loads are added.
The mold must have good mechanical properties and dimensional stability at temperature to properly withstand the stress and fatigue caused by pressing. Ex-press Plastics Ltd., the Docklands train seat and Scandura Seal Tex use this method to manufacture automotive parts.
Previous SMC/BMC
The manufacturing process of SMC/BMC phenol precludes consists of three steps:
- Manufacture of precontaminants. In the SMC machine the paste is mixed with resin, charge, catalyst and different additives with the reinforcement, obtaining a semi-product in the form of a coil.
- Curing precursors. The process is performed in the chamber that controls humidity and temperature.
- Pressed. It is performed at 160°C and at a pressure of 30 to 90 kg/cm 2.
As for phenol SMC, the applications currently performed are:
- Building panels and coatings.
- Transport elements (train seats, window frames, headrest, car hood interior, aircraft interior panels, supply components, etc. ). On the other hand, the Bakelite-Isole corporation also uses this technology to manufacture complex and impossible parts of aircraft.
- Electrical parts (machines, electrical parts, housings, etc.) ).
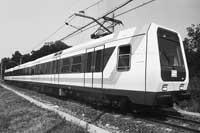
DSM UK Resins Dynochen UK, Norsolor, Western division of Chemical Corporation, Scandura Sealtex, Fers Resins S.A. and Bakelite-Isole are the companies that have developed technology for the manufacture of SMC.
Previous
In the case of phenol resin, it is the most widespread method in aviation and the processing is carried out in two phases: in the first one the appropriate diluent resin is dissolved and later the diluent is removed with the temperature. Viscosity and low water content levels obtained (60 10 6 cps.) is usually adequate. There are two ways of extracting parts of these precutees: pressing (with pressure of 90 kg/cm 2 and temperature of 160 ° C) and molding (vacuum is used for the first time for the evacuation of volatiles and then the grid is made with a temperature of 110-130 ° C and a pressure of 2-5 kg/cm 2).
The main disadvantages of this process at this time are the time it takes to process and, in the case of complex parts, its great decrease. Moreover, in applications that require good mechanical properties, carbon or aramid fabrics are frequently used.
Transport rules
In addition to the tests commonly used in the laboratory to measure the fire behaviour of plastic materials and the toxicity and opacity of smoke, special standards have been established in the transport, aircraft, construction and shipbuilding sectors. These standards include:
- BS 6853, 1987 “British Standard Code of ractice for Fire Precaution in the Disign and of Railway Paspasenger Rolconstructsling”, an English standard that takes into account the specific trials developed by London Underground Ltd. These tests are based on accurate measurements of the indices corresponding to smoke temperature and flammability.
- Royal Navy has developed specific standards for the classification of materials used in the naval industry: NES 705 “Selection of Material on the Basis of Their Fire Characteristics (May 1983)”. They classify the materials according to the parameters obtained by relating the opacity of smoke, the toxicity of gases and oxygen.
- As for aviation, the standards that phenol materials must meet are ASTM 1000.001 for air transport and the University of Ohio (USO) test.
- The standards to be met by construction materials in Spain are UNE 23-102 and UNE23-721 to UNE-23-730. Its function is to classify the materials used in construction according to their fire behavior. Moreover, at the present time, there is no specific standard for measuring the opacity and toxicity of fumes. French transport standards are used in this area.
- Standard NF X 10-702. It measures the optical density of combustion gases and pyrolysis of materials.
- Standard NF X 70-100. Method of tubular furnace. It focuses on the analysis of gases from combustion and pyrolysis of materials.
- Standard NF F 16-101. Regulates behavior against fire. Used in material selection.
Conclusions
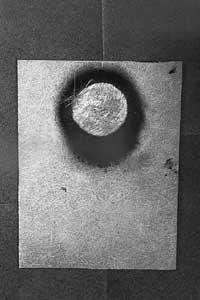
In recent years the use of plastic materials in the transport sector has seen a remarkable increase, reducing the weight of the parts has reduced energy consumption and has managed to reduce the pollution generated. However, given the severe results of the fires, the use of good fire performance materials to improve user safety has become a priority goal. Currently, resins that have shown better fire properties and lower costs are phenol.
But since the conditions for the transformation of these materials are not adapted, Basque and Spanish companies do not dominate the transformation of phenolic resins. At GAIKER we are improving the transformation conditions of phenolic resins and the shape and properties of the surface of the obtained parts. Among the steps taken in this regard, and taking into account existing rules and which will appear in relation to fire, the use of phenolic composite in construction and transport has been focused.
In addition, the technology has been developed to replace polyester and epoxy composites with phenol in parts that must meet fire standards. The results of this effort can already be seen in the steps taken in the manufacture and transformation of phenol precludes and their application in aviation in the industry of the Autonomous Community of the Basque Country, culminating in the adaptation of the manufacturing processes of components for the construction and transport by manual molding, RTM or pressing in injection and cold.
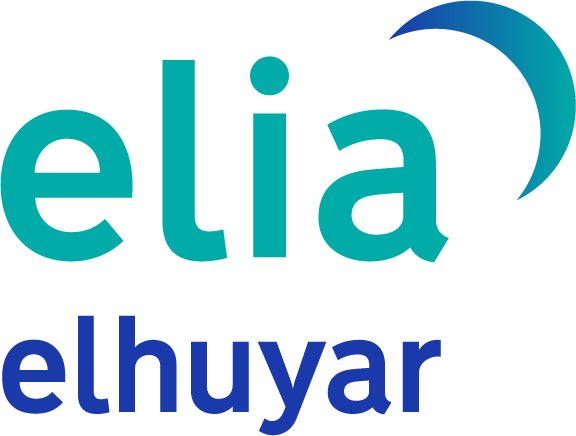
Gai honi buruzko eduki gehiago
Elhuyarrek garatutako teknologia