Metallic coatings (III): solutions
1999/06/01 Etxaide, Maider Iturria: Elhuyar aldizkaria
This section will explain the improvement of cleaning techniques, leaving wastewater treatment solutions for the future. The last section will show some improvement experiences in the coating industry.
Prolongation of bath life
The electrolytes accumulate contaminating metals from base materials and degradation products of the electrolyte additives.
In order to extend the life of the baths, the main components of the electrolyte (salts, surfactants, etc.) should be continuously analyzed and adjusted to theoretical values. On the other hand, it is important to know well the reasons why you want to renew the bathroom, that is, the accumulated substances that deteriorate the quality of the bathroom and the concentration in which these substances begin to produce negative effects.
Due to the variety of impurities or contaminants present in the bathrooms, the cleaning processes or techniques to be used are varied and specific. These techniques eliminate contaminated heavy metals, precipitate salts and eliminate degraded organic additives, impurities or insoluble particles. Some of these techniques are:
- Continuous removal of impurities and particles by filtration
- Elimination of pollutants or degraded additives by active carbon.
- Removal of contaminants (e.g. Use of selective electrolysis by low-density current in copper and nickel zinc electrolytes.
- Removal of contaminating metals in very acidic electrolytes (e.g. chromium III and iron of chromic electrolytes) by cationic exchange resins.
- Oxidation of chromium III to VI by small surface anode.
The most effective technique for the maintenance of degreasing processes is the use of oil separators. As for pickling, on the other hand, maintenance measures have a low practical viability, so the most appropriate preventive measure consists of proper prior cleaning.
Minimization of arrastres
It is called liquid attached to the surface of parts from previous arrastres, baths or cleanings. The reduction of arrastres, especially in installations with drum, is the most effective preventive measure both from the environmental point of view and pocket. Some measures to achieve the minimization of arrastres are:
- Lengthen draining time after extraction of frames and bonds containing process parts.
- Optimization of draining by slowly extracting the bath bulbs and establishing the proper drum rotation regime. This measure is fundamental in the sifting facilities.
- Suitable design of frames and bulbs.
- Modification of the physical characteristics or components of the bathroom, e.g. Sometimes arrastres can be reduced with a simple increase in bath temperature.
- Suitable design of parts avoiding concave parts, holes and grooves.
Cleaning technique optimization
Before tackling the improvement of the cleaning technique, the degree of quality sought in the washing waters of each operation should be foreseen, since the improvement of the cleaning technique will be useless if the desired degree of cleaning is not known in advance. In fact, most of the time it is cleaned much more than enough, even 1,000 times more. In addition, we must bear in mind that currently the costs of water supply, discharge rate and chemicals for water treatment are increasing.
The simplest methodology for defining quality is the washing quality criterion, that is, the quotient between the concentration of the bath in operation and the final phase of washing. For example, the 1,000 criterion indicates that it is diluted 1000 times less than the last wash bath.
In any case, although working with an adjusted quality criterion is the first step in water saving, the selected cleaning technique is the most decisive for the amount of water used.
Main cleaning techniques
The trend of most of the techniques that optimize the washing process is the repeated reuse of the washing water. In this way it is possible to concentrate the pollutant load in a smaller volume, which facilitates not only the return to the bathroom of the dragged electrolyte, but also the treatment of semi-concentrated waters more economically and safely.
The number of washing stages after each operation is critical to achieving efficiency with low water flow. It is advisable to have three stages for coverage operations and two for pretreatment (degreasing and pickling).
The main techniques used are:
- Cascading cleaning: this is called when the washing stage is associated with several series. The water is poured against the current of the parts, being immediately reused. This system is very useful.
- Watertight cleaning: cleaning the parts in a tank without continuous water supply. Although this system consumes little water, the washing quality is variable. Use combined with other systems is highly recommended.
- Closed cycle cleaning: Also called deionized cleaning. The collection of the pollutant load is done by an ion exchange equipment that allows the continuous reuse of water. This method generates small volumes of water but with high investment costs.
- Cleaning in the shower: it consists of using the shower system between the bathrooms in operation or between the different stages of washing. Allows to eliminate the greatest drag of the parts present in the frame with a low flow of water. For the shower the water of the last phase of washing is used, except justified cause (sanitary reasons, etc. ).
- Combined techniques: waterfall and closed cycle cleaning, waterfall and waterfall cleaning. These combinations are advantageous as they provide the advantages of both systems.
Type of bathroom | Cleaning quality criteria (Co/Cn) |
• Degreasing | 500-1,000 |
• Pickling | 1,000-2,000 |
• Zinc plated (without cyanide) | 1,000-5,000 |
• Other metallized (cyanide free) | 2000 to 10,000 |
• Cyanide zinc | 5,000-10,000 |
• Other cyanides (Cu, Ag, Brass) | 10,000 |
• Decorative chrome | 10,000 to 50,000 |
• Chrome steps | 200-2000 |
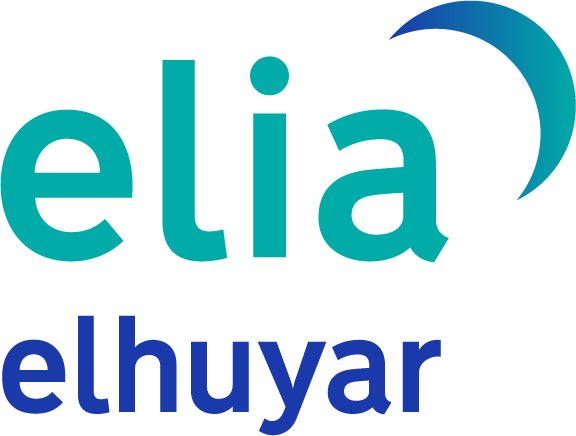
Gai honi buruzko eduki gehiago
Elhuyarrek garatutako teknologia