Liquid coal: looking for a fuel
1989/07/01 Aizpurua Sarasola, Joxerra Iturria: Elhuyar aldizkaria
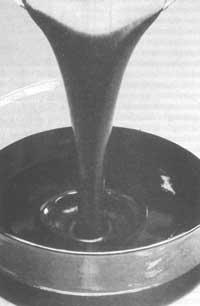
Since coal was used in our homes, it has not been long. When coal was found in solid state, it was not possible to use it in engines or in various applications. For this reason it was practically excluded. In addition, the substances that were thrown into the air by the burning of coal contaminated the atmosphere much more than those emitted from the burning of oil.
On the other hand, there is a growing trend towards the liquid state of fuels. Therefore, research carried out in the field of coal has sought to transform coal into liquid from a solid state.
The liquefaction technique requires very costly means and with the level of knowledge there is liquidated such a small part of the coal reserves that economic viability is not achieved. Gasification has the same drawbacks as liquidation.
For the liquefaction or gasification of coal a modification of the molecular structure of the solid must be produced. In suspensions, on the contrary, the same does not occur. In this case it is necessary to grind the coal until the average size of the grains is that of the flour and scatter this powder in a fluid. The products thus obtained present all the advantages of fluid fuel technologies. Coal suspensions can be divided into two main groups depending on the type of fluid mixed, that is, the fluid is gas or liquid.
The mixture of coal dust and an inert gas is already well known and is used in many industrial areas. The process consists schematically in the accumulation of coal dust in tanks, its transport in pipelines through pneumatic means and its dispersion in combustion chamber with adequate burner. The so produced flame is much like fuel, so some fuel boilers can be transformed for this function without a high cost.
However, those who can compete with petroleum derivatives are mixtures of coal and liquid. Therefore, in the following lines, the incidents of this type of mixtures will be reported.
The mixtures of coal and liquid began to work at the beginning of the oil industry. At that time, mixtures of coal and fuel were worked, but the expansion of petroleum derivatives put those works aside.
Given the shortage of oil or the difficulties in supplying oil, coal/liquid mixtures have been insisted on. On the occasion of the economic crisis around 1920, some ships that used fuel were reconverted to use the coal/fuel mix and during the last World War the Germans fed Diesel engines with carbon/water mix. However, it has been necessary to wait until the last decade to restart this type of mixtures.
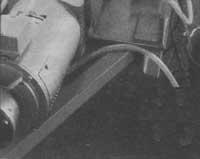
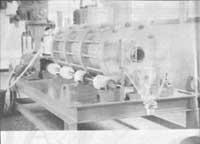
With the beginning of the investigations in 1974, the objective was to save fuel, so in the coal/fuel mix the largest proportion of coal should be achieved. Moreover, it must be taken into account that the heat power of coal (30,000 kJ/kg) is lower than that of fuel (41,800 kJ/kg). In addition, the solid/liquid mixture must meet a number of requirements to avoid fluid loss. The volumetric concentration of the components of the mixture varies depending on the grinding of the solid. If the solid is divided into spherical particles of equal size and is desired to maintain fluidity, its concentration should be less than 65%.
The United States hosted the first exhibition of the coal/fuel mix. The mass concentration of coal did not reach 30%. The boiler was 80 MW and the exhibition lasted one year (1979-1980). As a result of this successful exhibition, in the coming years new ones were made, especially in the US. and Japan. In these trials it was observed that the coal mass should not exceed 45%. The fuel savings thus obtained was less than 30%. In addition, the boiler should be added as special as expensive equipment so that the burnt coal powder did not go into the atmosphere.
Faced with this economic problem, there are two possible solutions: either to reduce conversion investments or to find a more economical mix than coal/fuel. Starting from the first path, it would be possible to demineralize the coal by a previous step (it is the minerals present in the coals, which produce dust in the combustion). Starting from the second track, it is known that fuel is the most expensive in the coal/fuel mix. Therefore, the fuel should be replaced by an abundant and economical liquid, such as water.
The current trend is to treat these two paths together. In addition, the current anti-pollution regulation limits coal dust residue to 0.8%. The way to achieve this is, first, until the average diameter of the ground carbon grains is 4 microns. The coal powder is dispersed through a lot of water. The resulting mixture is an aqueous suspension of coal and some mineral substances.
To this suspension a certain amount of hydrophobic fluid is added and by mechanical agitation the particles collide with each other. The hydrophobic liquid binds mainly to the coal particles and the coal particles begin to adhere to the bond forming agglomerates. When agglomeration has begun, this process is getting faster. At the end of this stage, a sieve collects the agglomerates, passing water and mineral substances through the network of the sieve. Finally, the agglomerates are cleaned with water.
Therefore, coal is ready to mix with water. To maintain the fluidity of these mixtures, the concentration of coal cannot exceed 50%.
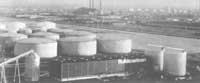
A proportion of water of at least 50%, represents important barriers in both storage and transport. Therefore, after several studies, the proportion of components of the carbon/liquid mixtures has remained as follows: 45%-55% coal, 6- 20% fuel and 30-35% water. The methods used to obtain this composition are different. However, the goal is to obtain the cheapest method for the price of the product to be similar to that of other fuels.
However, the main advantage lies in the abundance of coal. In many nations there is coal. Therefore, it dares some of the obstacles presented by oil and developing countries would not support energy dependence.
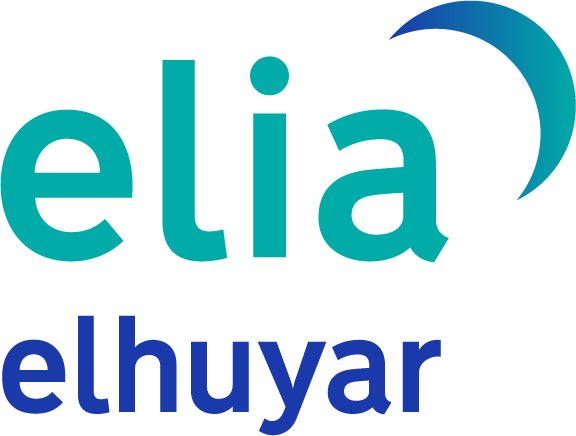
Gai honi buruzko eduki gehiago
Elhuyarrek garatutako teknologia