Copreci in space adventure
1999/01/01 Kortabarria Olabarria, Beñardo - Elhuyar Zientzia Iturria: Elhuyar aldizkaria
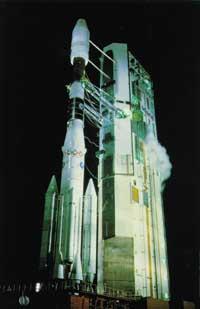
4, 3, 2, 1, 0… At one time, at the beginning of the space adventure, when, on the physics side, a rocket that dominated ignorance had to be sent into space. It was not like playing the lottery, because the basis of science was there, but many held their breath as the countdown began and did not relax their heart until they saw the rocket in the sky. Today, sending a rocket into space is quite common. However, everything must be perfectly interrelated, both the one who depends on the human being and the one who flees from his capacity (for example, the weather circumstances). Otherwise there are no rockets that extend.
Looking for new technologies
Although, as in many other types of technologies, there have been spectacular advances in space technologies, people working in the Copreci cooperative in Aretxabaleta live in a special way rocket launches, especially the Ariane rocket from the European Space Agency. In fact, at the most critical moment to send the Ariane rocket into space, in the countdown, begin to work the sensors that Copreci manufactures for Ariane, the European Space Agency, until now belonging to the ESA.
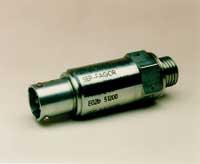
The collaboration between ESA and Copreci is not today. It has been several years since the beginning of this relationship. In the cooperative of Aretxabaleta Copreci, located in the structure of MCC, parts for appliances are mainly manufactured. Currently it allocates 70% of its production abroad, to the European, Asian and American and South American markets, to the appliance companies of these markets. In 1987 MCC decided that it could not stay out of the space race and came into contact with ESA
As a result, the Ariane rocket sensors are currently manufactured in Copreci. To begin this new task, MCC and Copreci sought the acquisition of new space technologies that could be used in the field of appliances. Since the sensor field was extended, Copreci has accumulated knowledge and experience in ultrasonic welding, electron beam welding, microsociality and strain techniques.
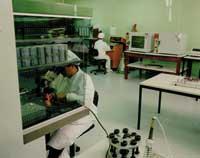
This experience has allowed the cooperative to offer numerous services in the field of welding in other companies, as well as a direct participation in the automotive and appliances sector in numerous projects: Game I, Game II and Esprit, for example.
In addition to technology, knowledge and experience, the sensor area has proven to be a good business, that is, it brings money. In addition, it seems that it can contribute more money, since from 2000 Ariane flights will increase.
Sensors, precision signal
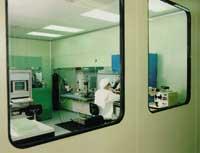
For us to return to the countdown, the role of the sensors they make in Copreci is important right now. The Vulcano engine, of the Ariane rocket, has launched and is slowly warming up to go out into space, among other things, burning a certain amount of hydrogen and oxygen. If not, there will be no shots. Copreci sensors are currently working to measure these amounts of oxygen and hydrogen, which is their function. If you have turned to heaven!
In the last three flights of Ariane the sensors manufactured in Copreci have been used, each with 150. Sensor assembly begins in Bordeaux, at the Société Européenne de Propulsion, where the heart of the sensors is developed.
Although the heart of the sensors comes from outside, the body or costume is made in Copreci. The assembly is done in the white room of the Sensor Area of the workshop, equipped with laminar flow cabins. The situation in this room is special, varying each hour 17.1% of the oxygen, maintaining an average temperature of 20.6 °C and a humidity of 42%. Those who work on it, as in some areas of hospitals, circulate with hair and feet covered, and on the wrist carry iron bracelets placed to avoid static electricity.
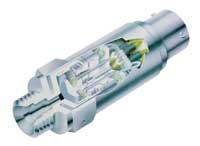
This does not damage the electrical circuits of the sensors. In fact, the electrical connections of the sensors are also welded in the white room using the microwelded system. They use 50 micrometer aluminum and silicon wire, welded by microscopes.
The welding of the machined parts that make up the sensor is done by an electron beam system that allows welding metals of different compositions, obtaining welds that would hardly be done with conventional welding systems. A leak detector is in charge of performing the waterproofing test of welded parts by electron beams, detector able to automatically verify the control of parts with a volume less than 100 liters. The leak detector performs detection in 9 seconds.
As the reliability of the sensor parts is checked at each stage of production, revisions are also made to ensure the correct condition of the sensor after assembly.
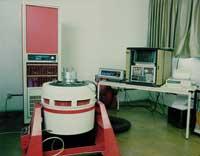
The pressure is measured on the one hand. In fact, the function of these sensors in the Ariane V Vulcano motor is to measure the pressure, so the pressure averages are measured and subjected to pressure. To do this, all sensors are inserted into three pressure machines and different measurements are made. On the other hand, measurements of the sensor's electrical signal are made using a scanner capable of measuring a resistance of up to 30M, a voltage of up to 300V and a temperature of -200ºC to 400ºC.
The sensors are also subjected to vibration, since when they are placed in the rocket they must withstand the vibrations of the Vulcano engine and the vibrations of the turboponps of the rocket. The workshop uses a closed container system to reflect this reality. It consists of vibration generator, vibrator, amplifier and accelerator. When started, the land of Copreci, in addition to a very intense noise, vibrates. Because at the time of launch they will suffer large oscillations, finally temperature tests are carried out with sensors.
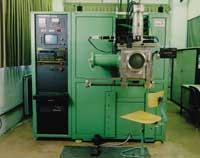
They introduce the sensors into a closed climate container and use them at temperatures between -80ºC and 180ºC. The climate package has a capacity to raise or lower 2ºC in a single minute. If all tests are passed, the sensors are terminated. Hence the Vulcano engine of the Ariane rocket. Although technology has advanced a lot today, and as indicated through these lines is a guarantee of a good, fine and precise work, we are convinced that whenever the countdown of Ariane begins, the heartbeat of those working in the Copreci Sensor Area is faster than usual.
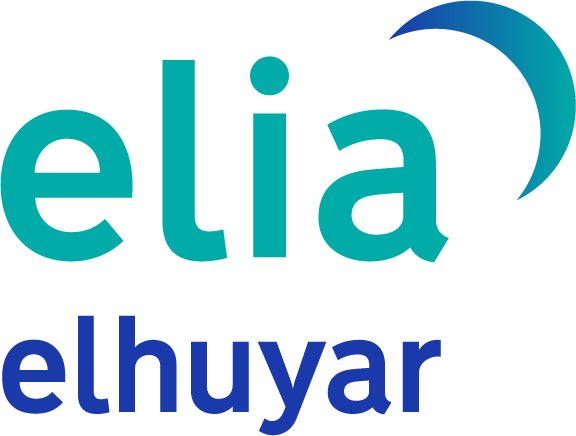
Gai honi buruzko eduki gehiago
Elhuyarrek garatutako teknologia