Airbus A380a, combustible del cielo
2004/02/01 Kortabarria Olabarria, Beñardo - Elhuyar Zientzia Iturria: Elhuyar aldizkaria
Dos motores a elegir
Dependiendo de la opción que realicen las empresas que adquieran el avión, el A380 podrá transportar dos tipos de motores, uno de Rolls Royce y otro de General Electric y Prat Whitney GP7000 Alliance. La empresa ITP de Zamudio colabora con Rolls Royce en la fabricación del motor Trent 900.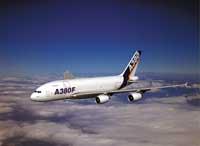
Quedan dos años para que comiencen los vuelos de los aviones A380 de Airbus. Sin embargo, Airbus ya ha recibido encargos para realizar más de 110 A380. No es de extrañar, ya que todos los expertos lo consideran sustituto del Boeing 747.
Le han puesto la siguiente tarjeta de presentación: “Avión A380: Tendrá capacidad para transportar a 550 personas, será tan rápido como seguro, consumirá mucho menos combustible y casi no contaminará el medio ambiente y cubrirá el aumento de la demanda de viajar en avión”. Por supuesto, son palabras de los mandos de Airbus. Sin embargo, está claro que la corona real aérea cambiará de memoria: El boeing 747 deberá entregarlo al A380.
El nuevo Rey se presentará con numerosas novedades de muy diversa índole. El diseño será nuevo, pero se mantendrán las características de los aviones de Airbus. Es decir, el gigante de tres plantas, para dos pasajeros y el subyacente para cargar, tendrá una serie de características que tenían los aviones pequeños. Por tanto, la cabina de los pilotos, los procedimientos de pilotaje del avión y las sensaciones serán similares. Esto significa que los pilotos no necesitarán grandes cursos de formación.
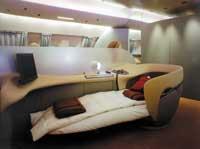
En materiales, el nuevo avión también aporta novedades. El A380 será mayor que los aviones actuales, pero tendrá menos peso y mejor aerodinámica. Esto evitará el trabajo previo de los motores, lo que reducirá el uso de combustibles, reducirá las emisiones a la atmósfera y permitirá volar más barato.
El Glare será el material más revolucionario que trae el A380. El material Glare está formado por finas capas de aluminio y fibras de vidrio intercaladas. Este material es más esponjoso que el aluminio, de menor compacidad y peso, pero más resistente y duradero. Durante la realización de los tests se agrietó una lámina de glare, que tras completar miles de ciclos de vuelo no aumentó la fisura. También reaccionó mejor ante la corrosión y el fuego que ante los materiales convencionales.
El nuevo avión consta de numerosas piezas de fibra de carbono reforzada, como la caja sur que unirá las alas y el fuselaje es de fibra de carbono. Si se hubiera realizado con la mejor aleación de aluminio, tendría un peso de tonelada y media más. La caja para el lema que conduce el avión también se fabricará con este material. El 40% de la estructura y de las piezas se realizarán con fibras de carbono, aleaciones metálicas ligeras y termoplásticas.
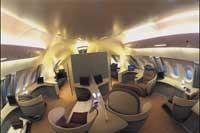
Como si la pérdida de peso se hubiera convertido en una obsesión, además de buscar materiales más ligeros, los diseñadores del nuevo avión de Airbus han realizado otros esfuerzos. Uno de ellos ha sido llevar el centro de gravedad del avión hacia atrás. Con este cambio, han ganado 40 metros cuadrados de suelo para el estabilizador vertical y su correspondiente peso, sin perder por supuesto la estabilidad.
Los cambios en los sistemas hidráulicos también han supuesto un menor peso de los aviones. Debido a la mayor presión de estos sistemas, los tubos y componentes hidráulicos para conseguir la potencia requerida por el avión serán menores y menores. Los aviones militares llevan tiempo usando estos sistemas de presión y ya han demostrado que, a pesar de estar bajo la influencia de la presión, los fluidos no se dañan. Después de todos los cambios, el A380 tendrá 240 toneladas de peso, 10-15 toneladas menos que el 747.
Además de tener un menor peso, se ha tenido en cuenta la seguridad y la estabilidad. El nuevo avión tendrá cuatro sistemas de vuelo. El avión podrá ser controlado por cualquiera de ellos, por lo que si falla algún sistema, el resto permanecerán ahí.
Los autores del A380 han extendido el respeto al medio ambiente a cuatro vientos. Dicen que podrá transportar más pasajeros pero sacando menos ruido y emitiendo menos emisiones a la atmósfera.
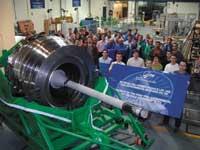
La reducción del ruido es consecuencia de la nueva generación de motores, el diseño de las alas y la tecnología y diseño del tren de aterrizaje. Esto permitirá al avión respetar todos los límites de ruido. Durante su estancia en el suelo, el A380 se desplazará con dos motores, en lugar de los cuatro, con lo que se reduce el ruido.
La reducción de la atmósfera se debe a la disminución del consumo de combustible. Y es que este avión va a necesitar 3 litros de combustible por cada 100 kilómetros y pasajero, el menor consumo que han tenido hasta la fecha los aviones utilizados en viajes largos.
Una de las dudas más importantes que surgen en la construcción de sus grandes aviones es la relativa a los aeropuertos, ya que no todos son capaces de coger aviones de cualquier tamaño. Por ello, antes de su diseño, los técnicos de Airbus han trabajado con 60 aeropuertos internacionales. En consecuencia, el A380 es compatible con las instalaciones de muchos aeropuertos actuales. Tiene grandes alas, pero eso es más una ventaja que un inconveniente. Por ello, y debido a la potencia de los nuevos motores, puede utilizar pistas relativamente cortas de despegue y aterrizaje. También le ayuda el tren de aterrizaje de 20 ruedas principal, ya que la huella que deja el avión es equivalente a varios aviones actuales, señal de que el peso se distribuye bien en veinte ruedas.
El número de pasajeros que puede transportar el A380 también ha provocado la colaboración entre los aeropuertos y Airbus. Se necesitan grandes salas de espera para 550 personas. El sistema de evacuación de las 16 salidas de emergencia también es consecuencia directa del número de pasajeros.
Innovación de procesos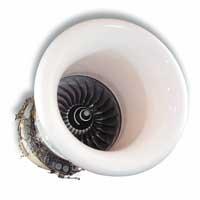
Como es evidente, el A380 de Airbus será un avión grande y nuevo basado en pequeños cambios. Estas pequeñas adaptaciones han supuesto no sólo la renovación del avión, sino también la renovación de su proceso de fabricación. Una de las principales novedades es la propia organización del trabajo. Alrededor de 6.000 personas trabajan con el nuevo avión. Para poder coordinar el trabajo de tantas personas se ha implantado un sistema on line. Dado que los datos están en manos de los participantes en el proyecto, los cambios se pueden realizar de forma más rápida, paso a paso, para evitar sorpresas cuando se inicien los trabajos de montaje.
El gigante está construyendo con nuevas técnicas de fabricación. Algunos de ellos han dado muy buen resultado y ya se han incorporado a los procesos de fabricación de otros aviones. La soldadura por haz láser puede ser un buen ejemplo. Hasta el momento, varios tramos del fuselaje se unían mediante remaches, pero en el caso del A380 se está trabajando en la soldadura por haz de láser. Además de reducir el peso, con esta técnica se unen las partes del avión más rápidamente que con los remaches, disminuyendo el riesgo de fisuras.
Debido al tamaño del avión, algunas de las personas que trabajan han tenido que realizar algunos cambios en sus instalaciones y realizar nuevas instalaciones. Destacan los de Tolosa y Hamburgo, donde se realizarán los últimos montajes.
En Tolosa, cerca del aeropuerto de Blagnac, estaban finalizando en diciembre las instalaciones con una superficie de 50 hectáreas. Allí han realizado, entre otros, los campos de pruebas estáticas y el montaje final. La zona tiene una longitud de 490 metros, una anchura de 250 metros y una altura de 46 metros, lo que equivale a 20 campos de fútbol. Cerca de este lugar se ha construido un edificio de 19.000 metros cuadrados para acoger el simulador de la cabina A380 y otros sistemas.
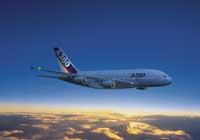
En Hamburgo se comenzó a acondicionar una superficie de 140 hectáreas en noviembre de 2001. El edificio principal, hangar de montaje, se inauguró en mayo del año pasado. El edificio tiene 228 metros de longitud, 120 metros de anchura y 23 metros de altura. Aquí se montan la parte delantera y trasera del fuselaje y los sistemas básicos de vuelo. También se han construido nuevos edificios en Gales, hangares en Getafe y Puerto Real, talleres en Nantes, Saint Nazaire…
El transporte ha dado a los de Airbus tantos quebraderos de cabeza como la construcción de nuevos edificios. El montaje final se realizará en Tolosa. Allí formarán el avión gigante, pero muchas de las partes que se deben llevar son demasiado grandes para los medios de transporte habituales y han tenido que inventar nuevas, como las gabarras especiales. Las partes del avión se llevarán por mar, carretera y río. Cuando el avión se completa con el puzzle de los episodios, recorrerá los cielos de allí y de aquí, realizando largas rutas.
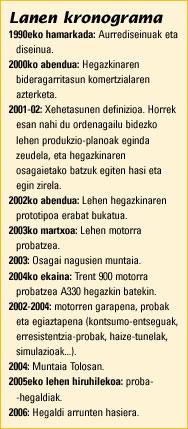
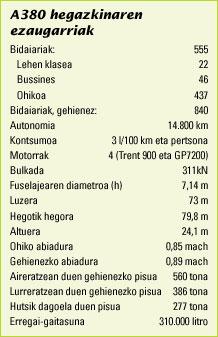
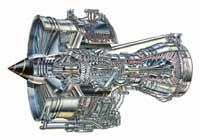
El motor 900 es el último de la familia de los motores Trent de Rolls Royce. La primera cría de esta familia de motor, el motor Trent 700, nació hace 25 años. Las creaciones posteriores se han basado en sus características. La familia Rolls Royce ha sido un éxito, ya que se han hecho miles. Según los británicos, estos motores han conseguido ganar el 80% de los que han entrado en la competición de compra.
El nuevo motor diseñado por Rolls Royce tiene tres ejes: el de alta presión, el intermedio y el de baja presión. En ITP fabrican una turbina de baja presión que soporta la menor presión y temperatura en el interior del motor. The turbine at baja pressure moves the turbine through a pivote. La turbina tiene un diámetro de dos metros, dividida en cinco etapas que conforman los álabes y la estructura fija, aunque es menor que la del motor GP7000, que tiene seis etapas.
El motor Trent 900 se basa en tres ejes. Según el ingeniero de ITP Bittor Olabarria, este motor aúna bajo peso y alta eficiencia a la vez, “con bajo consumo, bajo coste y bajo ruido”. El montaje completo de los motores se realiza en el propio Rolls Royce, en Gran Bretaña, y ITP ya ha comenzado a dar pasos en la fabricación de las turbinas de este motor. Las piezas de las turbinas se realizarán en Zamudio para su posterior montaje en Ajalvir de Madrid. ITP deberá entregar las turbinas en el Rolls Royce, en el Derby inglés, que es el encargado de entregarlas.
Según Olabarria, en cualquier motor el peso es un factor muy importante y en algunos casos puede llegar a tener límites. La versión más pesada del motor Trent tiene unos 5.900 kilos, mientras que el motor de General Electric y Pratt Whitney tiene 100 kilos más. Sin embargo, el motor GP 7000 de General Electric y Pratt Whitney tiene otras características favorables. “Esto es un motor de dos ejes, por lo que puede ser más económico y, en teoría, necesita menos mantenimiento”.
La relación eficiencia/consumo del motor también dice mucho a favor o en contra de un motor, pero el límite real en el desarrollo de un motor es el ruido. “Un motor puede tener mayor o menor consumo, mejor o peor eficiencia y evolucionará o retrocederá con lo que tiene. Con la cuenta de ruido no hay margen. Las restricciones son cada vez más numerosas y las limitaciones que se imponen no pueden ser superadas. Para acercarnos a estos objetivos hemos tenido que utilizar nuevas tecnologías”.
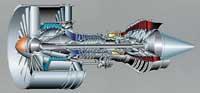
Los Rolls Royce han conseguido reducir el ruido aumentando el diámetro de la turbina en 13 centímetros, reduciendo así la velocidad de salida del gas y provocando el ruido del motor. Al ser el motor Trent 900 de Rolls Royce, también es responsable del ruido que puede generar el motor. Sin embargo, también han tenido que colocar su piedras en ITP. “Como se ha comentado anteriormente, desde el punto de vista del ruido, los aviones tienen grandes limitaciones. Nosotros también hemos hecho esfuerzos para reducir el ruido e introducirlo en los límites, aunque la parte menos ruidosa de los motores sea la misma turbina. El componente más ruidoso es el ventilador delantero”.
Para poder hacer la turbina han tenido que hacer cosas nuevas, trabajar en equipo y superar retos. “Una de ellas corresponde a la aerodinámica de la turbina, ya que hemos realizado un diseño aerodinámico 3D para que el motor sea más eficiente. Se han realizado importantes cambios en el diseño: optimización de discos, carcasa, refrigeración, rodamientos de la estructura, etc. Debido a que la temperatura a la entrada de la turbina es de 1.000ºC, se han tenido que emplear aleaciones de níquel. La mayoría de los materiales han sido fundidos y forjados con exigentes requerimientos de calidad. La mecanización de estos materiales no es fácil, ni la soldadura ni el conformado, debido a que las tolerancias por peso son muy pequeñas. Hemos tenido que realizar numerosas investigaciones y desarrollos”.
A pesar de la importancia de estos detalles, según Bittor Olabarria, el mayor reto para ITP ha sido el tamaño de los componentes del nuevo motor, ya que los criterios utilizados en las turbinas que se han realizado hasta el momento eran o no sabían. No se sabe hasta probarlo y así se abordó en ITP.
El mecanizado y fabricación de discos de turbina, soportes traseros, carcasa de la turbina, álabes estáticos, rodamientos para soportar la estructura y otros componentes se ha realizado por primera vez en Zamudio. Para poder hacer las piezas han tenido que comprar máquinas, aprender a usarlas, y aprender a hacer los ingredientes. El proceso tiene más dificultades de las que parece. “En los componentes de la aviación las tolerancias son muy importantes y difíciles, ya que el material que utilizamos, además de ligero, es duro. Por tanto, hemos tenido que realizar un trabajo de mecanizado muy fino, mejorando y afinando el proceso de fabricación”.
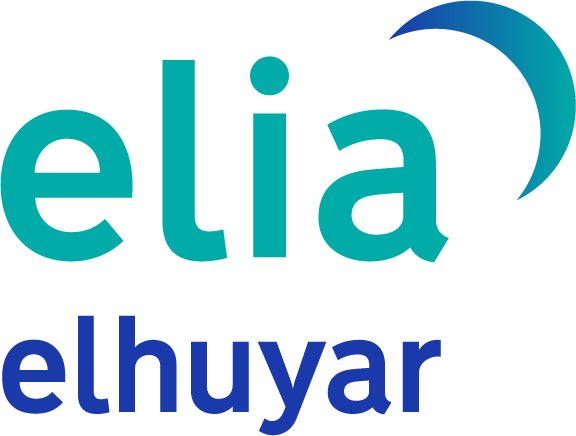
Gai honi buruzko eduki gehiago
Elhuyarrek garatutako teknologia