Airbus A380a, sky fuel
2004/02/01 Kortabarria Olabarria, Beñardo - Elhuyar Zientzia Iturria: Elhuyar aldizkaria
Two engines to choose from
Depending on the option made by companies that purchase the aircraft, the A380 will be able to transport two types of engines, one from Rolls Royce and one from General Electric and Prat Whitney GP7000 Alliance. The company ITP de Zamudio collaborates with Rolls Royce in the manufacture of the Trent 900 engine.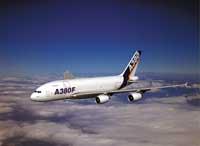
There are two years left for the flights of Airbus A380 aircraft to begin. However, Airbus has already received orders for more than 110 A380. No wonder, as all experts consider it a substitute for the Boeing 747.
You have been given the following business card: “A380 aircraft: It will be able to transport 550 people, will be as fast as it is safe, will consume much less fuel and almost will not pollute the environment and will cover the increased demand for air travel.” Of course, these are words from the Airbus controllers. However, it is clear that the royal aerial crown will change memory: The boeing 747 must be delivered to the A380.
The new King will be presented with numerous novelties of very different kinds. The design will be new, but the features of Airbus aircraft will remain. That is, the three-storey giant, for two passengers and the underlying to load, will have a series of features that had small planes. Therefore, the cockpit of the pilots, the piloting procedures of the plane and the sensations will be similar. This means that drivers will not need large training courses.
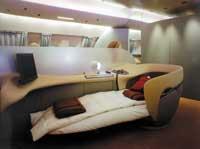
In materials, the new aircraft also brings novelties. The A380 will be larger than current aircraft, but will have less weight and better aerodynamics. This will prevent the previous work of the engines, which will reduce the use of fuels, reduce emissions to the atmosphere and allow to fly cheaper.
The Glare will be the most revolutionary material the A380 brings. The Glare material consists of thin layers of aluminum and interspersed glass fibers. This material is more fluffy than aluminum, less compactness and weight, but more resistant and durable. During the tests a glare sheet was cracked, which after completing thousands of flight cycles did not increase the fissure. It also reacted better to corrosion and fire than to conventional materials.
The new aircraft consists of numerous pieces of reinforced carbon fiber, such as the south box that will link the wings and the fuselage is carbon fiber. If it had been made with the best aluminum alloy, it would have a tonne and a half more weight. The box for the motto that drives the plane will also be manufactured with this material. 40% of the structure and parts will be made with carbon fibres, light metal alloys and thermoplastics.
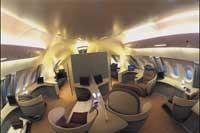
As if weight loss had become an obsession, in addition to looking for lighter materials, the designers of the new Airbus aircraft have made other efforts. One of them has been to take the center of gravity of the plane back. With this change, they have gained 40 square meters of floor for the vertical stabilizer and its corresponding weight, without losing of course the stability.
Changes in hydraulic systems have also meant lower aircraft weight. Due to the increased pressure of these systems, the tubes and hydraulic components to achieve the power required by the aircraft will be smaller and smaller. Military aircraft have long been using these pressure systems and have already shown that, despite being under the influence of pressure, fluids are not damaged. After all the changes, the A380 will have 240 tons of weight, 10-15 tons less than 747.
In addition to having a lower weight, safety and stability have been taken into account. The new aircraft will have four flight systems. The plane can be controlled by any of them, so if any system fails, the rest will remain there.
The authors of the A380 have extended respect for the environment to four winds. They say that it will be able to transport more passengers but taking out less noise and emitting less emissions into the atmosphere.
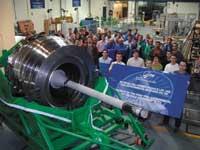
Noise reduction is a consequence of the new generation of engines, wing design and technology and landing gear design. This will allow the aircraft to respect all noise limits. During your stay on the ground, the A380 will move with two engines, instead of four, reducing noise.
The reduction of the atmosphere is due to the decrease in fuel consumption. And is that this plane will need 3 liters of fuel for every 100 kilometers and passenger, the lowest consumption that have had to date the planes used in long trips.
One of the most important doubts that arise in the construction of its large planes is that related to airports, since not all are able to catch planes of any size. Therefore, before its design, Airbus technicians have worked with 60 international airports. Consequently, the A380 is compatible with the facilities of many current airports. It has big wings, but that is more an advantage than an inconvenience. Therefore, due to the power of the new engines, you can use relatively short take-off and landing tracks. It also helps the main 20-wheel landing gear, since the footprint left by the aircraft is equivalent to several current aircraft, a sign that the weight is distributed well in twenty wheels.
The number of passengers the A380 can carry has also led to collaboration between airports and Airbus. Large waiting rooms are needed for 550 people. The evacuation system of the 16 emergency exits is also a direct consequence of the number of passengers.
Process innovation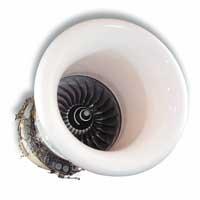
As is evident, the Airbus A380 will be a large and new aircraft based on small changes. These small adaptations have meant not only the renewal of the plane, but also the renewal of its manufacturing process. One of the main novelties is the organization of the work itself. Around 6,000 people work with the new plane. In order to coordinate the work of so many people, an online system has been implemented. Since the data is in the hands of project participants, changes can be made faster, step by step, to avoid surprises when mounting jobs are started.
The giant is building with new manufacturing techniques. Some of them have done very well and have already been incorporated into the manufacturing processes of other aircraft. Laser beam welding can be a good example. So far, several sections of the fuselage were joined by rivets, but in the case of the A380 laser beam welding is being worked. In addition to reducing weight, this technique binds the parts of the plane faster than with rivets, reducing the risk of cracks.
Due to the size of the plane, some of the people who work have had to make some changes to their facilities and make new facilities. Outstanding are those of Toulouse and Hamburg, where the last assemblies will be held.
In Toulouse, near the airport of Blagnac, the facilities with an area of 50 hectares were finishing in December. There they have carried out, among others, the static test fields and the final assembly. The area has a length of 490 meters, a width of 250 meters and a height of 46 meters, which equals 20 soccer fields. Near this place a building of 19,000 square meters has been built to accommodate the simulator of the A380 cabin and other systems.
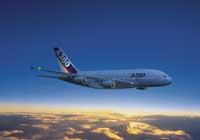
In Hamburg an area of 140 hectares was started in November 2001. The main building, assembly hangar, was opened in May last year. The building is 228 meters long, 120 meters wide and 23 meters high. The front and rear of the fuselage and the basic flight systems are mounted here. New buildings have also been built in Wales, hangars in Getafe and Puerto Real, workshops in Nantes, Saint Nazaire…
The transport has given Airbus as many headaches as the construction of new buildings. The final assembly will be held in Toulouse. There they will form the giant plane, but many of the parts to be carried are too large for the usual means of transport and have had to invent new ones, such as special cabinets. The parts of the plane will be taken by sea, road and river. When the plane is completed with the puzzle of the episodes, it will travel through the skies there and here, making long routes.
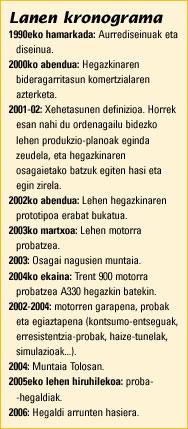
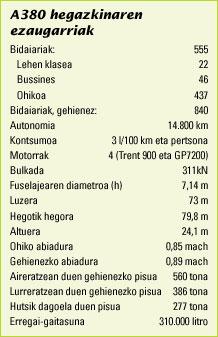
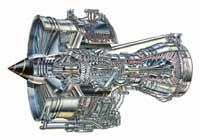
The 900 engine is the latest in the Rolls Royce Trent family. The first breeding of this motor family, the Trent 700 engine, was born 25 years ago. Later creations have been based on their characteristics. The Rolls Royce family has been a success, as thousands have been made. According to the British, these engines have managed to win 80% of those who have entered the buying competition.
The new motor designed by Rolls Royce has three axes: high pressure, intermediate and low pressure. ITP manufactures a low pressure turbine that supports the lowest pressure and temperature inside the engine. The turbine at baja pressure moves the turbine through a pivote. The turbine has a diameter of two meters, divided into five stages that make up the blades and the fixed structure, although it is smaller than that of the GP7000 engine, which has six stages.
The Trent 900 engine is based on three axes. According to ITP engineer Bittor Olabarria, this engine combines low weight and high efficiency at the same time, “with low consumption, low cost and low noise”. The complete assembly of the engines is carried out in the Rolls Royce itself, in Britain, and ITP has already begun to take steps in the manufacture of the turbines of this engine. The turbine parts will be made at Zamudio for later assembly at Ajalvir in Madrid. ITP must deliver the turbines at the Rolls Royce in the English Derby, which is responsible for delivering them.
According to Olabarria, in any engine weight is a very important factor and in some cases it can have limits. The heaviest version of the Trent engine is around 5,900 kilos, while the General Electric and Pratt Whitney engine is 100 kilos more. However, the General Electric and Pratt Whitney GP 7000 engine has other favorable features. “This is a two-axis engine, so it can be cheaper and theoretically needs less maintenance.”
The efficiency/consumption ratio of the engine also says a lot for or against an engine, but the real limit in the development of an engine is noise. “An engine can have higher or lower consumption, better or worse efficiency and will evolve or recede with what it has. With the noise account there is no margin. Restrictions are increasing and the limitations imposed cannot be overcome. To get closer to these goals we had to use new technologies.”
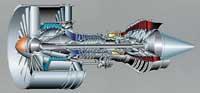
The Rolls Royce have managed to reduce noise by increasing turbine diameter by 13 centimeters, thus reducing gas output speed and causing engine noise. Being the Rolls Royce Trent 900 engine, it is also responsible for the noise that the engine can generate. However, they have also had to place their stones on ITP. “As mentioned above, from the noise point of view, aircraft have great limitations. We have also made efforts to reduce noise and introduce it to the limits, although the less noisy part of the engines is the same turbine. The loudest component is the front fan.”
In order to make the turbine they had to do new things, work as a team and overcome challenges. “One of them corresponds to the aerodynamics of the turbine, since we have made an aerodynamic 3D design to make the engine more efficient. Important design changes have been made: disc optimization, housing, cooling, structure bearings, etc. Since the temperature at the turbine inlet is 1,000ºC, nickel alloys have been used. Most materials have been cast and forged with demanding quality requirements. The machining of these materials is not easy, neither welding nor forming, because the weight tolerances are very small. We’ve had to do a lot of research and development.”
Despite the importance of these details, according to Bittor Olabarria, the biggest challenge for ITP has been the size of the components of the new engine, since the criteria used in turbines that have been performed so far were or did not know. It is not known until it was tested and so it was addressed in ITP.
Machining and manufacturing of turbine discs, rear supports, turbine housing, static blades, bearings to support the structure and other components was first performed at Zamudio. To make the pieces they have had to buy machines, learn how to use them, and learn how to make the ingredients. The process has more difficulties than it seems. “In aviation components tolerances are very important and difficult, since the material we use, in addition to light, is hard. So we had to do very fine machining work, improving and refining the manufacturing process.”
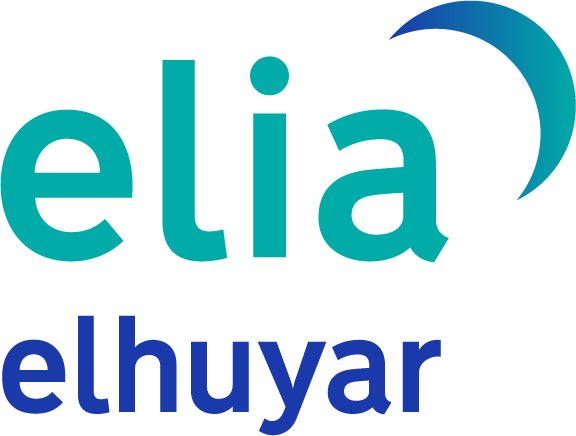
Gai honi buruzko eduki gehiago
Elhuyarrek garatutako teknologia